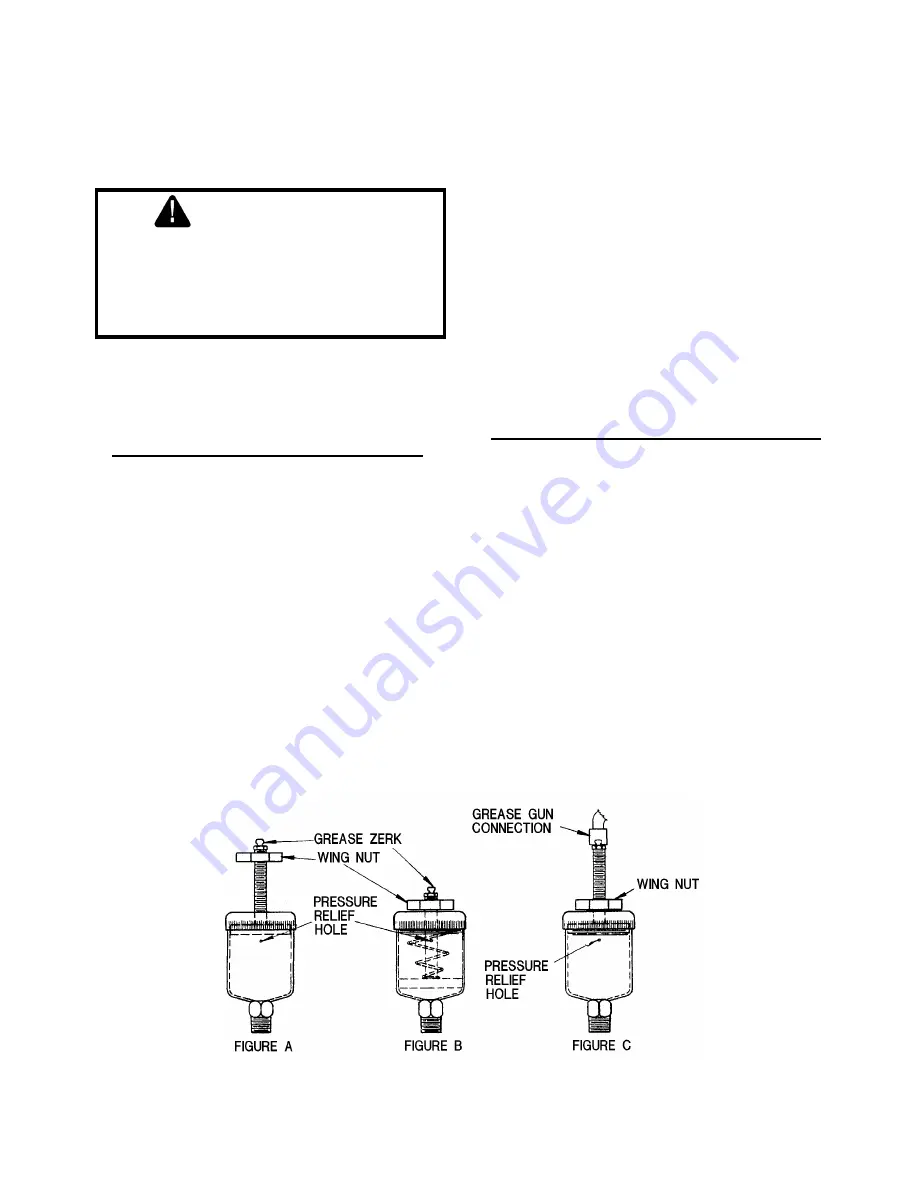
Use a strainer on suction line to prevent the entrance of
oversize solids. This strainer should be submerged deep
enough to prevent air from being drawn into the suction line,
thus reducing the pump’s capacity and pressure.
CAUTION!
THIS PUMP SHOULD NOT BE OPERATED WITHOUT
A STRAINER ON THE END OF THE SUCTION LINE
TO PREVENT STICKS, STONES, RAGS AND OTHER
FOREIGN MATTER FROM BEING DRAWN INTO THE
IMPELLER. THE STRAINER SHOULD BE CLEANED
REGULARLY TO INSURE FULL FLOW.
B-3) Discharge:
Connect discharge hose or pipe to discharge on pump.
If Discharge hose is used, protect it from being driven over.
Do not use quick closing check valves.
SECTION C: OPERATION RECOMMENDATIONS:
1. Fill the pump case with liquid prior to starting the pump.
A self priming pump does require the case to be at least
2/3 full of liquid in order to self prime. Operate at sufficient
speed to prime pump. Generally speaking, the pump will
prime faster if it is operated at a fast speed.
2. Place the self-feeding grease lubricator in operation by
turning the wing nut on the threaded plunger shaft counter
clockwise as far as it will go.
Do not force the plunger
into the grease cup as this can cause a seal failure
.
See Maintenance Recommedations, Paragraphs 1 and 2
for instructions on filling the grease cup.
3. In cold weather operation, the pump will not freeze as
long as it is running. However, it may freeze if it is not
drained while standing idle. To drain the pump, remove
the drain plug at the bottom of the pump case and rotate
the impeller at least once to assure removal of all the
water.
4. The discharge of a self priming centrifugal pump may be
closed briefly without damaging the pump. However, the
water will soon heat up and this can damage the pump
seal.
5. It is not desirable to run the pump without liquid in the
pump case. If the pump must be run in order to check the
operation of the engine or motor, fill the case with
sufficient water to keep the rotating seal wet. This will
eliminate damage to the seal and other pump parts.
6. If the pump has been idle for some time, the impeller
may appear to be stuck or locked in place. This is usually
caused by a film of rust or dirt between the impeller and
volute. A little extra force on the crank may break it loose.
If not, the pump must be dismantled.
SECTION D: MAINTENANCE RECOMMENDATIONS:
D-1) Seal Lubrication:
A self-feeding lubricator is provided to supply grease to the
shaft seal of the pump. The grease cup is empty when the
wing nut, positioned at the outer end of the threaded plunger
shaft, recedes to the cap of the grease cup. To refill the
grease cup, rotate the wing nut clockwise as far as it will go,
attach a zerk gun to the zerk fitting, then fill until grease oozes
from the relief hole on the side of the cup. For operation,
return the wing nut to the end of the plunger.
Never force
the plunger into the grease cup as this can cause seal
failures.
(See Fig. 1)
A #1 grease is normally recommended. However, where
high ambient temperatures are encountered, such as in
direct sunlight, a #2 grease can be used. Use a water
resistant, nonfiberous grease. Lithium base greases are
excellent and molydisulphide is acceptable. Normally, the
sodium soap base greases are the only non-water resistant
types that are not acceptable for mechanical seal lubrication.
FIGURE 1
6
Summary of Contents for burks pumps WB12
Page 8: ...FIGURE 3 8 ...