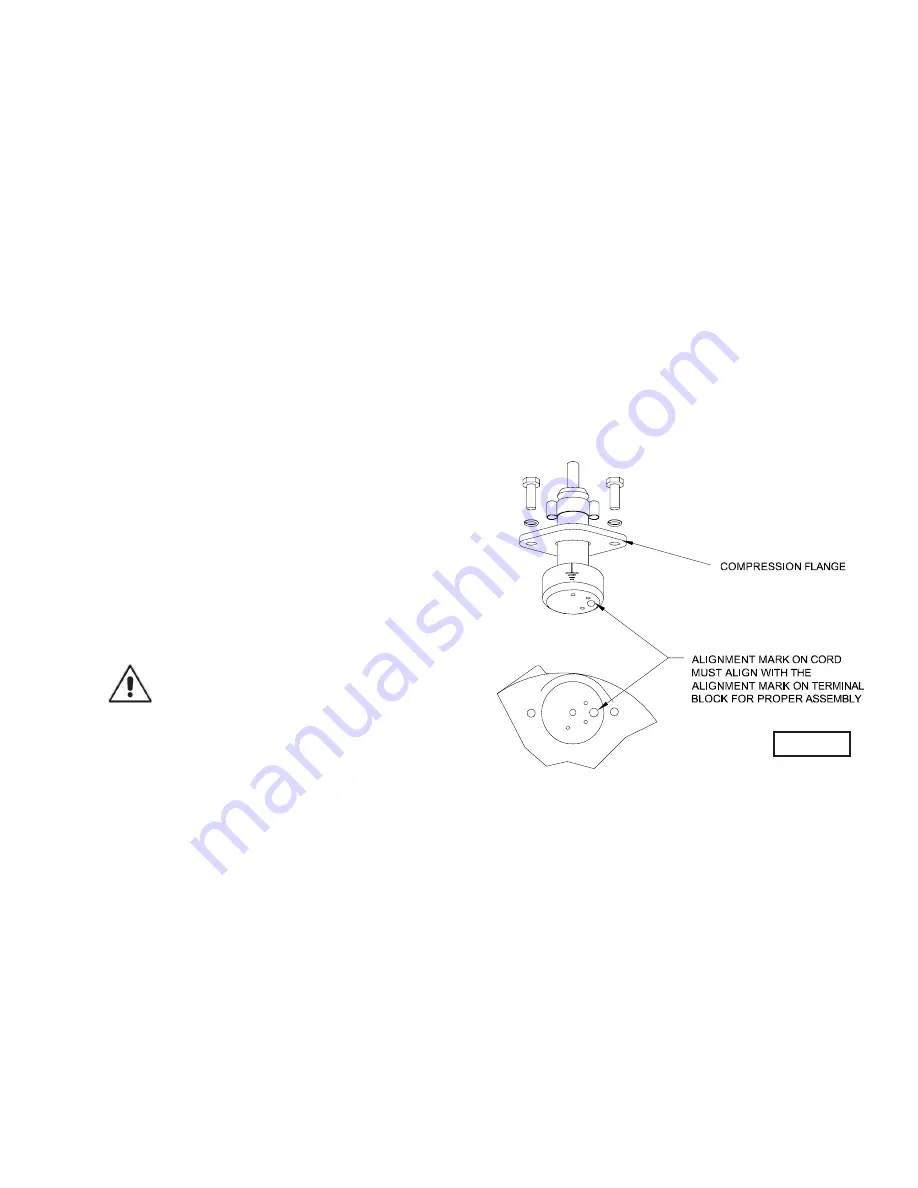
13
Position unit upright, using blocks to avoid resting unit on
shaft. Unscrew cable hex bolts (11) and remove compression
flange (16a) and power cord (16). Remove snap ring (19) with
a flat head screwdriver. Pull the terminal block (21) out of the
housing (6) using a T-bolt or a pair of pliers and a .25-20 screw
in the threads of the terminal block (21). Be sure to leave slack
on the motor leads connected underneath.
Use needle nose pliers to pull each female connector off of the
pins on the underside of the terminal block (21), see Figure 11.
The unit voltage should be noted. Repeat cable and terminal
block removal procedure for any control cables (56) if equipped.
Remove socket head cap screws (47). Vertically lift the motor
housing (6) from seal plate (5) by lifting handle (13). Inspect
square ring (27) for damage or cuts. Remove the motor bolts
and lift motor stator from seal plate (5). Disconnect capacitor
leads from capacitor (9, single phase units). Examine bearing
(25) and replace if required. If replacement is required, remove
bearing (25) from motor shaft using a wheel puller or arbor
press, see Figure 13.
Check motor capacitor (9, single phase units) with an Ohm
meter by first grounding the capacitor by placing a screwdriver
across both terminals and then removing screwdriver. Connect
Ohm meter (set on high scale) to terminals. If needle moves
to infinity (∞) then drifts back, the capacitor is good. If needle
does not move or moves to infinity (∞) and does not drift back,
replace capacitor (9). If moisture sensors (4, optional) are
damaged, disconnect leads by removing machine screws (45)
and washers (46) from probes (4). Remove probes (4) from
seal plate (5). To test the temperature sensor (50, optional),
check for continuity between the black and white wires. If
found to be defective, contact a motor service station or Barnes
Pumps Service department. Inspect motor winding for shorts
and check resistance values. Check rotor for wear. If rotor or
the stator windings are defective, the complete motor must be
replaced.
IMPORTANT! - All parts must be clean before
reassembly.
F-4.2) Reassembly:
Moisture Sensors -
If pump is equipped with optional moisture
sensors, reassemble by applying thread compound to threads
on probes (4) and install in upper seal plate (5), see Figures 18
& 19. Connect wire assemblies (53) to probes (4) with washers
(46) and machine screws (45).
Thermal Sensors -
If pump is equipped with optional
thermal sensors use terminal connectors (52) to connect wire
assemblies (51) to sensor leads. If found to be defective,
contact a motor service station or Barnes Pumps Service
department.
Bearings -
When replacing bearing, be careful not to damage
the rotor or shaft threads. Clean the shaft thoroughly. Press
bearing (25) on the motor shaft, position squarely onto the
shaft applying force to the inner race of the bearing only, until
bearing seats against the retaining ring (24) (Included with
motor).
Motor -
Slide lower bearing (25) and motor shaft squarely
into the seal plate (5) until bearing seats on the bottom. Place
stator over rotor, lining up motor bolts with holes in seal plate
(5). Position capacitor (9, single phase units) so that it will lay
on the opposite side of the cable entry bosses of the motor
housing (6). Reconnect capacitor leads. Torque motor tie bolts
to 17 in-lbs. Set square ring (27) in groove on seal plate (5).
F-4.3) Wiring Connections:
Check power cord (16) and control cord (56, if used), for
cracks or damage and replace if required (see Figure 15).
Make internal wiring connections which are independent of
the terminal block as shown, using connectors (48) and wire
assemblies (49) as required. Do not use wire nuts. Slip motor
leads and ground wire through fiberglass sleeve. Lower motor
housing (6) down onto seal plate (5) while aligning holes and
stringing motor leads through the cord entry bore(s). (Slipping
cords inside a 1 ft. length of .5” conduit makes this easier).
Place socket head cap screws (47) through seal plate (5) into
motor housing (6) and torque to 60 in-lbs. Reconnect motor
and optional control leads to the underside of the terminal
block(s) (21), (54 optional) as shown in Figure 14. Note that
the pins are numbered underneath the terminal block. Place
o-ring (20) into groove in terminal block and lubricate with
dielectric oil. Press the terminal block (21) into the housing so
it seats completely below the snap ring groove. Place snap
ring (19) into groove in cord entry bore of housing. Repeat
terminal block installation for control cable, if equipped.
FIGURE 14
Summary of Contents for BARNES STEP-DS Series
Page 15: ...15 FIGURE 16 CONTIUED ...
Page 17: ...17 FIGURE 17 STEP SS Single Seal ...
Page 18: ...18 FIGURE 18 STEP SS Single Seal ...
Page 19: ...19 FIGURE 19 STEP DS Double Seal ...
Page 20: ...20 FIGURE 20 STEP DS Double Seal ...
Page 23: ...23 Notes ...
Page 24: ...24 Notes ...