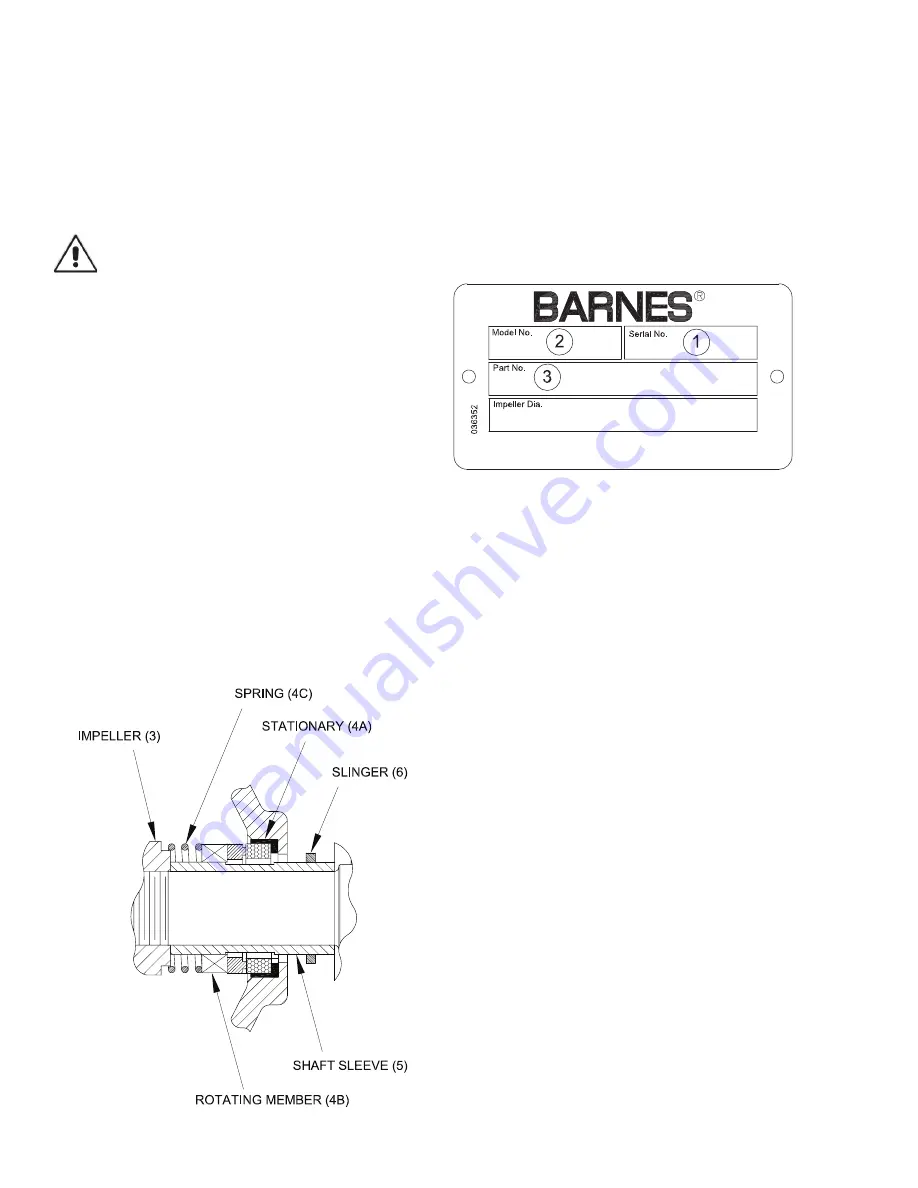
6
E-2) Shaft Seal Service:
To expose the seal for examination or replacement, remove
volute and impeller as outlined in Section E-1. Remove
spring (4C) and rotating member (4B) from shaft sleeve (5).
All of the components of the shaft seal are now exposed for
examination or repair. If any part of the shaft seal shows wear
or damage, replace entire seal assembly.
When stationary member (4A) needs replaced, press used
stationary member (4A) from pedestal (8).
CAUTION! - Handle seal parts with extreme care.
DO NOT scratch or mar lapped faces.
Lightly oil and replace shaft sleeve (5) and stationary member
(4A), press stationary member (4A) over shaft sleeve and
into pedestal (8). Lightly oil shaft sleeve and inner surface of
bellows of rotating member (4B). With lapped surface facing
pedestal, slide rotating member (4B) onto shaft sleeve until
lapped faces of (4A) and (4B) are together. If fi nger pressure
is not suffi cient, use a piece of tubing making sure to press
ONLY on bellows tail section not on metal retainer. Make
sure driving lugs in retainer are mated in carbon washer.
Place spring (4C) on shaft sleeve and in place on rotating
member (4B) making sure it is seated on metal retainer and
not cocked or resting on bellows tail. Reassemble remainder
of pump.
E-3) Shaft and Bearing Service:
Remove volute, impeller and shaft seal as outlined in
Sections E-1 and E-2. Remove cap screw (19), and
lockwashers (18), and pull bearing cap (17) from pedestal
(8). Tap on drive end of shaft (13) with a block of wood and a
hammer to drive the shaft (13) and bearings (15) and (9) from
pedestal (8). Examine all parts and replace those showing
wear and/or damage. If bearings need repacked use a grease
such as SOHIO FACTRAN EP-3, or equal. Reassemble
remainder of pump.
SECTION: F REPLACEMENT PARTS
F-1 ORDERING REPLACEMENT PARTS:
When ordering replacement parts, ALWAYS furnish the
following information:
1. Pump serial number and date code. (F-4)
2. Pump model number. (F-3)
3. Pump part number. (F-2)
4. Part description.
5. Item part number.
6. Quantity required.
7. Shipping instructions.
8. Billing instructions.
F-2 PART NUMBER:
The part number consists of a six (6) digit number, which
appears in the catalog. A one or two letter suffi x may follow
this number to designate the design confi guration. This
number is used for ordering and obtaining information.
F-3 MODEL NUMBER:
This designation consists of numbers and letters which
represent the discharge size, series horsepower, motor phase
and voltage, speed and pump design. This number is used
for ordering and obtaining information.
F-4 SERIAL NUMBER:
The serial number block will consist of a six digit number,
which is specifi c to each pump and may be preceded by
a alpha character, which indicates the plant location. This
number will also be suffi xed with a four digit number, which
indicates the date the unit was built (Date Code).
EXAMPLE: A012345 0490.
Reference the six digit portion (Serial Number) of this number
when referring to the product.
Summary of Contents for 029676
Page 9: ...9 ...
Page 12: ...Notes ...