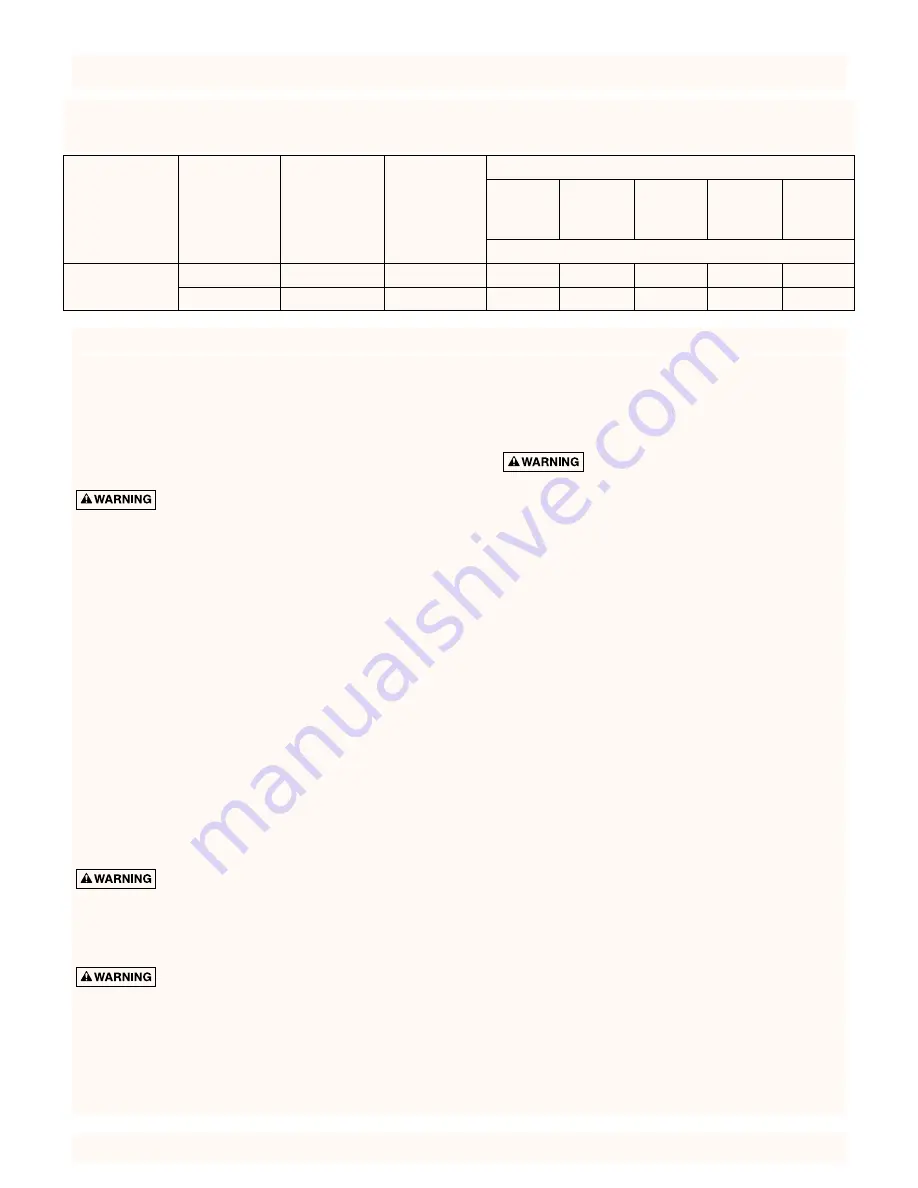
ELECTRICAL
MAINTENANCE
Lubrication
It is not necessary to lubricate the pump or its motor.
The motor bearings are lubricated for life. The me-
chanical shaft seal in the pump is water lubricated and
self-adjusting.
Draining for Winter
Risk of electric shock. Disconnect
power before working on unit.
Pump should be drained whenever it is disconnected
from service or is in danger of freezing.
1. DISCONNECT POWER.
2. Open faucet and relieve all pressure on system be-
fore proceeding.
3. Disconnect pressure switch tube (Key No. 17, Page
12) at barbed elbow on pressure switch (Key No.
28) and allow tube to drain.
4. Open draincock (Key No. 22, Page 12) on pump
body and allow pump to drain.
5. Remove priming plug to vent pump; disconnect
hose (Key No. 6, Page 14) at tank end and drain
pressure tank and all piping to a point below the
frost line.
6. Be sure to drain any piping that may be cut off from
normal system drain due to check valve installation.
Vinyl Bag Removal
Be sure ALL air pressure has been re-
leased from tank before removing nuts from
flange. Failure to do this may result in serious or
fatal injury. Do not attempt to open tank unless
all pressure has been relieved!
Risk of electric shock. Disconnect
power before working on unit.
1. DISCONNECT POWER TO PUMP.
2. Drain system as follows:
A. Open faucet closest to tank.
B. Open draincock (Key No. 22, Page 12) on pump
body.
C. Remove hose (Key No. 6, Page 14) from tank
elbow.
3. Relieve (expel) ALL air pressure in system by re-
moving valve core.
4. Disconnect outside piping from tank and pump.
To avoid serious or fatal injury, be
sure all air pressure has been released from
tank before proceeding to step 5.
5. Remove nuts and washers from tank inlet flange
(Key No. 2, Page 14). Tap inlet flange to break seal.
Remove flange.
6. Wherever convenient, hold bag with pliers and cut
with single-edge razor blade or sharp knife. Bag will
not come out in one piece. Continue pulling and
cutting until bag is removed.
7. Clean and dry inside of tank.
8. Place replacement bag on a clean surface with
opening up. Flatten bag and force air out.
9. Tightly roll bag towards center opening.,
10. Before center opening is covered up, force air out
of remaining portion of bag. Finish rolling bag.
11. To make bag easier to insert into tank, sprinkle out-
side of bag with talcum powder.
12. Being careful not to break valve, stand tank on end.
Push tightly rolled bag into tank.
13. Reach into bag and push out sidewalls. You need
not remove all wrinkles.
14. Clean center opening ring on bag and lip on tank.
15. Pull ring on bag through tank opening and fit over
tank lip. BE SURE it seats properly in groove on tank
lip.
16. Clean sealing surface of inlet flange and place on
studs.
17.
NOTICE:
Tighten nuts as follows:
A. Hand tighten all nuts.
B. Tighten one nut snug.
C. Tighten opposite nut snug.
D. Proceed, tightening opposite pairs to a snug fit.
E. Recheck all nuts, using same pattern. Be sure all
nuts are tight and you have a good seal.
7
Table II Wiring Chart
Recommended Wire and Fuse Sizes
Distance in Feet from Motor to Meter
Branch
0’
101’
201’
301’
401’
Max.
Fuse*
to
to
to
to
to
Motor
Load
Rating
100’
200’
300’
400’
500’
Horsepower
Volts
Amps.
Amps
Wire Size
115
8.8
15
14
12
10
8
8
1/2
230
4.4
15
14
14
14
14
12
Summary of Contents for 390.252156
Page 15: ...15 ...