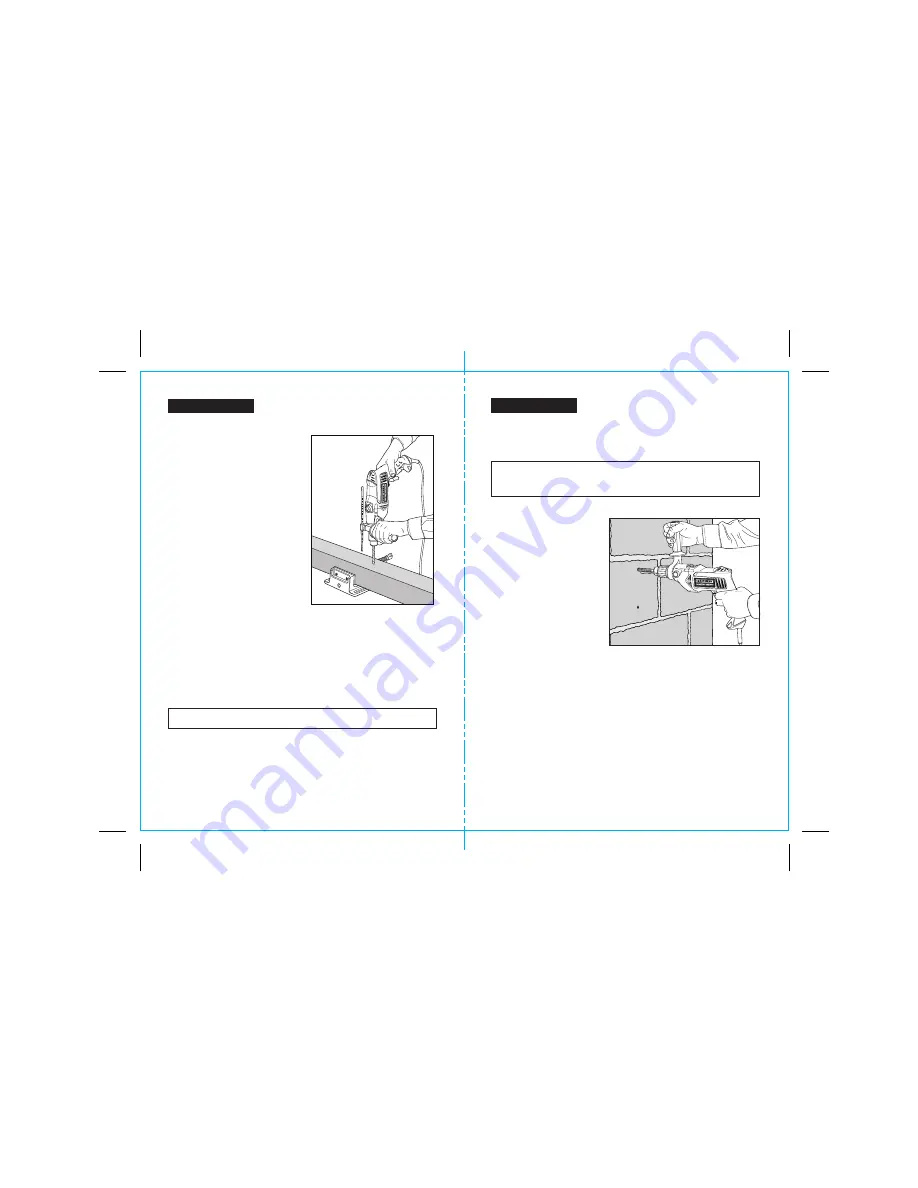
19
OPERATION cont.
NOTE: When unplugging the drill, first make sure that the Power Lock-On
Feature is not engaged, by pressing on the trigger switch to release it. Failure
to do so will cause the hammer drill to start immediately the next time it is
plugged in. Property damage or serious personal injury could result.
HAMMER DRILLING (Fig. 15)
1. Always unplug the drill when
installing or removing bits and
accessories.
2. When hammer drilling in masonry
such as brick, concrete, cinder
block, stone and tile, use only
carbide tipped bits rated for
percussion drilling and be certain
that the bit is sharp.
3. Make sure that the hammer drill
mode is selected and that the bit
is securely installed in the chuck.
4. Use a constant and firm force on
the hammer drill to drill effectively.
A smooth, even flow of dust from
the hole indicates the proper
hammer drilling rate.
5. Start hammer drilling at slower speeds and increase to full speed while applying firm
pressure on the hammer drill.
6. When hammer drilling, use just enough force on the drill to keep it from bouncing
excessively or “rising” off the bit. Too much force will cause slower drilling speeds,
overheating, and a slower drilling rate.
7. Drill straight and keep the bit at a right angle to the work (the bubble level will help).
Do not exert side pressure on the bit when hammer drilling, as this will cause clogging
of the bit flutes, overheating, and a slower drilling speed.
8. When hammer drilling deeper holes, pull the bit partially out of the hole frequently
(with the drill still running), to help clear debris from the hole. This will help keep the bit
form overheating and produce a cleaner drilled hole.
OPERATING THE DRILL AS A HAMMER DRILL
When using your drill for percussion hammer drilling applications, make sure you have the
Rotary and Hammer Drilling Selector Switch
in the Hammer Drilling position
(see Page 13, Fig. 4).
Fig. 15
18
OPERATION cont.
NOTE: Large holes in steel (5/16 to 1/2 inches) can be made more easily if a
pilot hole 5/32 to 3/16-inch is drilled first.
ROTARY DRILLING (Fig. 14) cont.
6. Always clamp the workpiece firmly. If
drilling thin material, use a wood “back-up”
block to prevent splintering or damage to
the workpiece.
7. Always apply pressure in a straight line
with the bit. Use enough pressure to keep
the drill bit biting, but do not push hard
enough to stall the motor or deflect the bit.
8. Hold the hammer drill firmly to control the
twisting action of the hammer drill and bit.
9. IF HAMMER DRILL STALLS, it is usually
because it is being overloaded or
improperly used. RELEASE TRIGGER
SWITCH IMMEDIATELY, remove drill bit
from workpiece, and determine cause of
stalling. DO NOT START AND STOP A
STALLED DRILL BY QUICKLY APPLYING
AND RELEASING PRESSURE ON THE
TRIGGER SWITCH. THIS CAN
DAMAGE THE DRILL.
10. To minimize stalling or breaking through
the workpiece, reduce pressure on the
hammer drill and ease the bit through the last part of the hole.
11. Keep the motor running when pulling the bit out of a drilled hole. This will help prevent
the bit from jamming.
12. With variable speed there is no need to use a center punch at the point to be drilled.
Just use a slow speed to start the hole and accelerate by applying pressure to the
trigger switch when the hole is deep enough to drill without the drill bit skipping out
of the hole.
13.
When drilling in metal
start drilling with slow speed and increase to full power while
applying pressure on the hammer drill. A smooth even flow of metal chips indicates
proper drilling rate. Use a cutting lubricant when drilling metals. The exceptions are
cast iron and brass, which should be drilled dry. The cutting lubricants that work best
are sulfurized cutting oil or lard oil; bacon grease will also serve the purpose.
14. When driving screws and various types of fasteners, always use the proper driving bit
matched to the screw or fastener. Start the driving action using a constant force on the
fastener at a lower speed and torque, slowly increasing the speed and torque to
effectively drive and set the fastener in its finished position.
Fig. 14