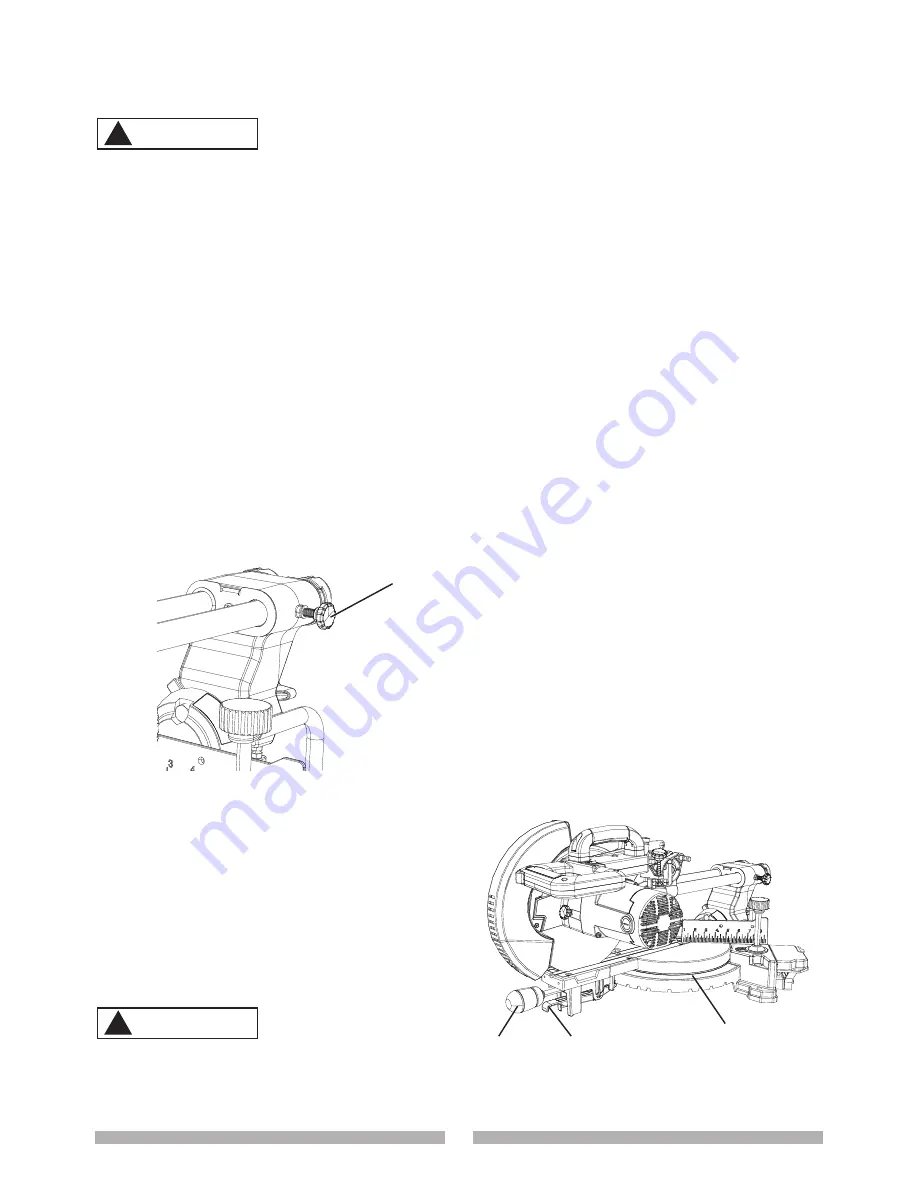
36
37
SLIDING CARRIAGE SYSTEM
(FIG. CC)
To reduce the risk of injury, return
carriage to the full rear position after
each crosscut operation.
1. For chop cutting operations on small
workpieces, slide the cutting head
assembly completely toward the
rear of the unit and tighten the slide
carriage lock knob (1).
2. To cut wide boards up to 12 in., the
slide carriage lock knob (1) must be
loosened to allow the cutting head
to slide freely.
Fig. CC
BEFORE LEAVING THE SAW
●
Never leave tool running
unattended. Turn power OFF. Wait
for all moving parts to stop.
●
Make workshop childproof. Lock the
shop. Disconnect master switches.
Store tool away from children and
other unqualified users.
To avoid injury from materials being
thrown, always unplug the saw to
avoid accidental starting, and
WARNING
!
WARNING
!
remove small pieces of material
from the table cavity.
MITER CUT (FIG. DD)
1. When a miter cut is required, unlock
the miter table by turning the miter
handle (1) counterclockwise.
2. While holding the miter handle, lift
up on the positive stop locking
lever (2).
3. Rotate the miter table to the right or
left with the miter handle.
4. When the table is in the desired
position, as shown on the miter
scale (3), release the positive stop
locking lever and tighten the miter
handle. The table is now locked at
the desired angle. Positive stops are
provided at 0°, 15°, 22.5°, 31.6°
and 45°.
IMPORTANT:
Always tighten the
miter table lock handle before
performing every cutting operation.
5. Turn the Laser Trac
®
on and
position the workpiece on the table
for prealignment of your cut.
Fig. DD
3
1
2
1