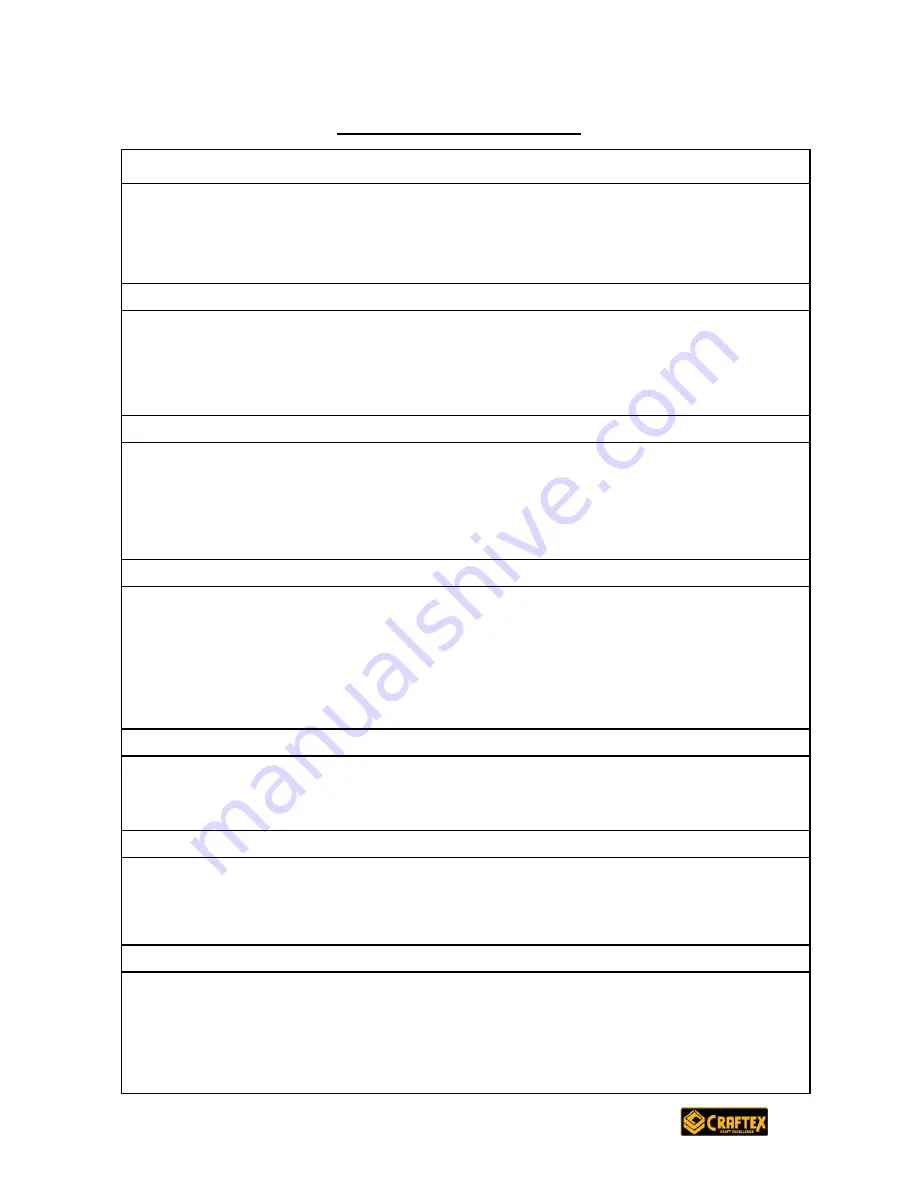
34
TROUBLESHOOTING
PROBLEM
CAUSE
SOLUTION
Saw does not start
Cord is not plugged in
Plug Power Cord in
Circuit breaker is tripped
Reset Breaker
Motor/switch/cord is damaged
See Qualified Technician
Circuit fuse is blown
Replace circuit fuse
Excess Vibration
Blade is damaged
Replace Blade
Uneven Work Surface
Change to a flat surface
Not Mounted properly
Retighten all hardware
Blade is not balanced
Replace Blade
Rip Fence does not
Rails are not clean
Clean/Wipe away debris
Move Smoothly
Fence not mounted properly
Remount fence
Clamp Screw is out of adjustment
Adjust clamp screw
Cuts burn or bind work
Work is being fed too fast
Slow down the feed rate
Blade is dull
Replace blade/re-sharpen
Rip Fence misaligned
Align rip fence properly
Wood is warped
Change work piece
Separator not aligned
Align separator
Saw not making 90°/45° cuts
Miter gauge misaligned
Align/Adjust miter gauge
Bevel stops not adjusted
Adjust/check bevel stop
Motor overheats
Work piece fed too fast
Slow down feed rate
Blade cuts poorly
Blade is mounted backwards
Re mount the blade
Blade is dirty
Clean blade of debris
Incorrect blade for cut
Chose correct blade
PROBLEM
CAUSE
SOLUTION
PROBLEM
CAUSE
SOLUTION
PROBLEM
CAUSE
SOLUTION
PROBLEM
CAUSE
SOLUTION
PROBLEM
CAUSE
SOLUTION
PROBLEM
CAUSE
SOLUTION
Summary of Contents for CT146
Page 1: ...CT146 10 TABLE SAW ...
Page 4: ...4 ...
Page 5: ...5 ...
Page 6: ...6 ...
Page 10: ...10 LOOSE PARTS OF MACHINE ...
Page 11: ...11 LOOSE PARTS OF MACHINE ...
Page 36: ...36 SCHEMATIC DIAGRAM MITER GAUGE ASSEMBLY ...
Page 38: ...38 SCHEMATIC DIAGRAM STAND ASSEMBLY ...
Page 40: ...40 SCHEMATIC DIAGRAM RIP FENCE ...
Page 42: ...42 SCHEMATIC DIAGRAM BLADE GUARD ...
Page 44: ...44 SCHEMATIC DIAGRAM MOTOR ASSEMBLY ...
Page 46: ...46 SCHEMATIC DIAGRAM MAIN HOUSING ...
Page 48: ...48 SCHEMATIC DIAGRAM TABLE ASSEMBLY ...
Page 50: ...50 SCHEMATIC DIAGRAM INTERNAL BODY ...
Page 54: ...54 ...
Page 55: ...55 ...
Page 56: ...56 ...