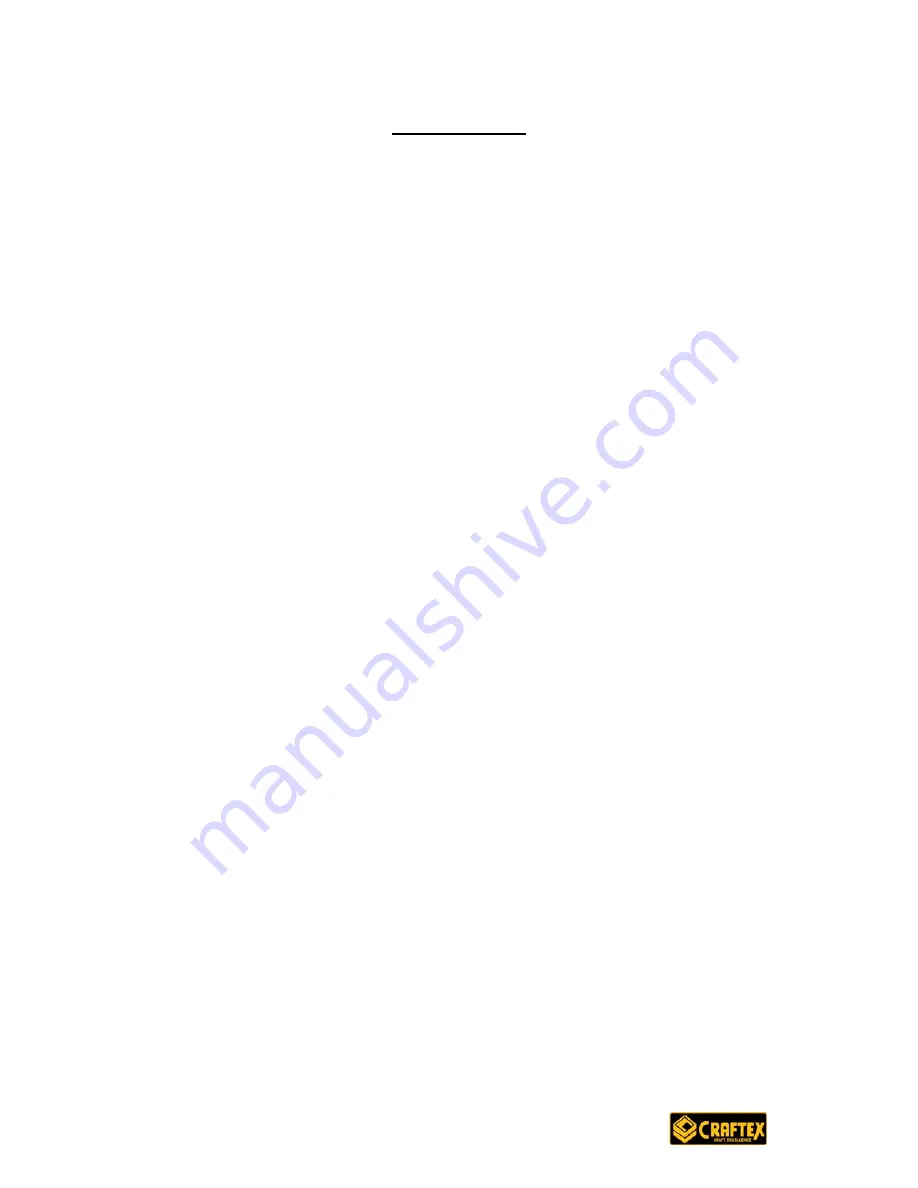
9
ASSEMBLY
DRILL PRESS HEAD TO COLUMN.
Lift the drill press head carefully and position it over the column.
The column fits into the drill press mounting hole. Make certain the mounting hole
is properly seated on the column. Line the drill press head up with the table and
base and then tighten the two set-screws using the supplied hex wrench.
FEED HANDLE.
Fit the feed handle onto the shaft.
Summary of Contents for CT024N
Page 1: ...OWNER S MANUAL CT024N 8 DRILL PRESS ...
Page 15: ...15 CT024N 8 Drill Press SCHEMATIC DIAGRAM ...
Page 16: ...16 CT024N 8 Drill Press ...
Page 18: ...18 ...
Page 19: ...19 ...
Page 20: ...20 ...
Page 21: ...21 ...