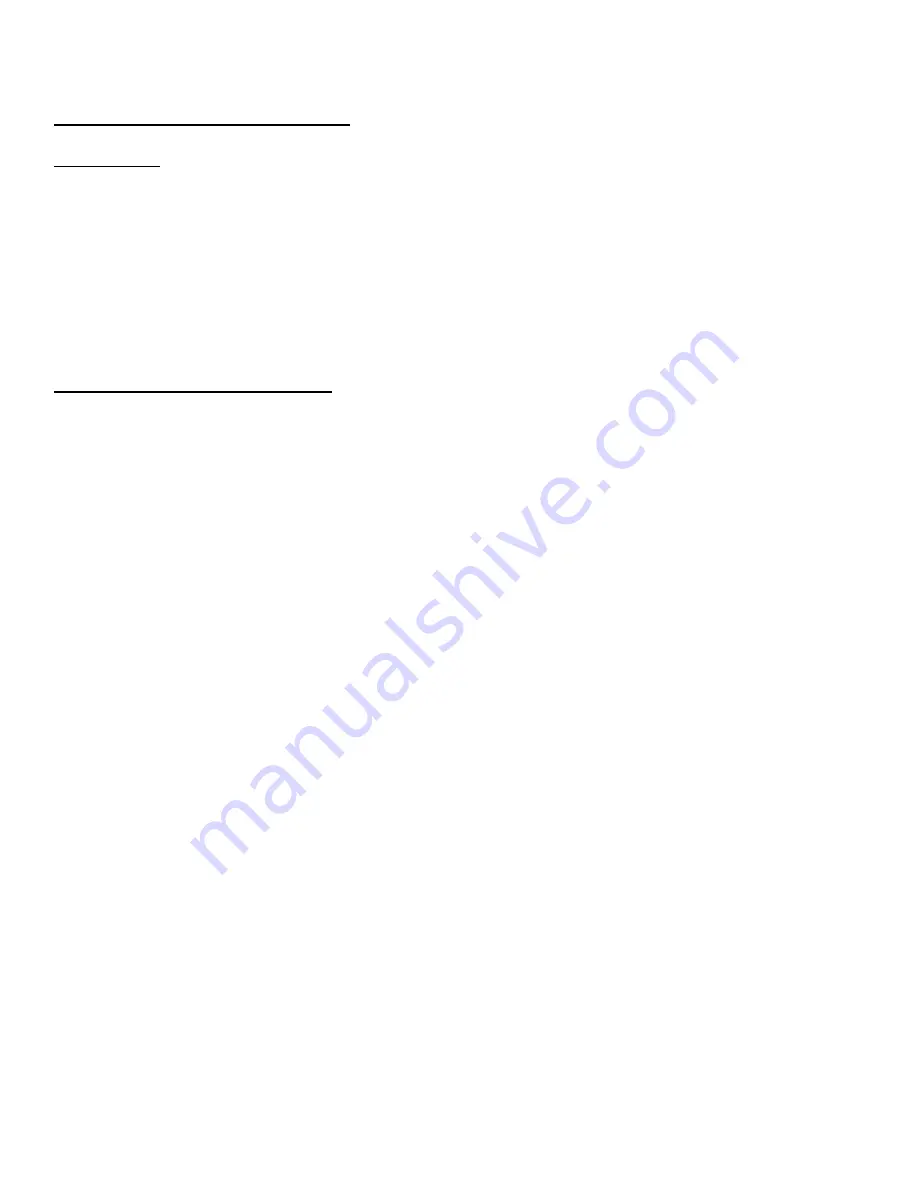
© 2014 CPT Autopilot Inc.
www.cptautopilot.com
Page 12 of 17
PART III – Maintenance & Troubleshooting
1. Maintenance and Adjustments
A. Belt Tension
Sliding the motor unit down on its mounting bracket slots with your hands tensions the belt. Pull the belt
snug by hand by putting downward pressure on the drive box and tightening the wing nuts. Do not over-
tension the belt; it causes clutch wear & makes the clutch difficult to operate and the shaft can be bent. Over-
tensioning also removes any beneficial “give” in the drive system. If it doesn't slip it is tight enough. An optional
belt tensioner is available which keeps the belt tensioned and will act as a shock-absorber to dampen shock loads
from the rudder.
An over-tightened belt does not allow any give;
a less tensioned belt will jump with a thump
to warn of heavy loads or if striking the rudder-stops. The hose-clamps on the pedestal bracket will need to be
tightened after the rubber scratch pads compress. Reversed pedestal installations will typically need the bracket
directly fastened to the pedestal with screws, hose-clamp slippage under loads will cause a slack belt.
B. Drive Pulley and Clutch Maintenance
The drive pulley is held in one of two positions (engaged or disengaged) on its shaft by a spring-loaded ball,
which fits into one of two grooves on the shaft. All parts are either Delrin, Nylon or stainless steel.
Most clutch wear is caused when hand-steering under high belt tension without lubrication. Lubricate the
drive pulley and shaft often. High tension also makes the clutch difficult to operate. Salt water may
eventually cause salt crystal build-up in the locating spring and ball. The drive pulley should be removed,
cleaned and oiled or greased periodically - more often in severe or heavy use conditions..
If the autopilot will not be steering for awhile, remove the belt from the small pulley & hang it over the
binnacle or wheel shaft. This will lessen wear and prolong the life of the clutch when hand steering.
To service & lubricate the clutch/drive pulley:
1.
Loosen tension on the drive belt and remove belt from the small pulley.
Remove the two screws from the back of pulley cap; these are the shear-pins. (The black, grooved grip
used to engage and disengage the clutch is the pulley cap. The screws are the machined shear pins.)
Do
not
attempt to remove the shear-pins if the pin ends are bent. Reach and straighten them with long-nosed
pliers or a small vise grip first.
2.
Remove pulley cap.
3.
Remove stainless steel retaining clip from its groove at the end of the shaft.
4.
Remove pulley gear.
5.
Rinse pulley in fresh water. Work the ball inside the shaft-hole in and out.
6.
Clean , dry and lubricate shaft & work lubrication into the ball inside the shaft-hole..
7.
Replace pulley, retaining clip, and pulley cap.
8. Replace the two shear screws. Do not over-tighten screws, they can strip or the pulley may distort. Rotate
the pulley on the shaft and observe the ends of the shear screw pins:
Adjustment:
There should be an even gap (1/16” appx.) between the end of the shear pins and stainless
steel shaft-plate. If one of the pins is too close to shaft-plate, it may tend to catch in the plate holes when
the wheel is turned. If the pulley does not turn freely, if the pins are not even, or too close to the shaft-
plate, back off one or both of the screws slightly; there us a set-screw in the gear teeth to adjust the
spring & ball detente.
8.
To remove the clutch drive-plate: Loosen the stainless Allen-head set-screw in the side of the driveplate,
and remove clutch assembly from motor shaft. Grease motor shaft, replace clutch, and be sure to tighten
driveplate setscrew securely. Replace belt and adjust the belt tension.