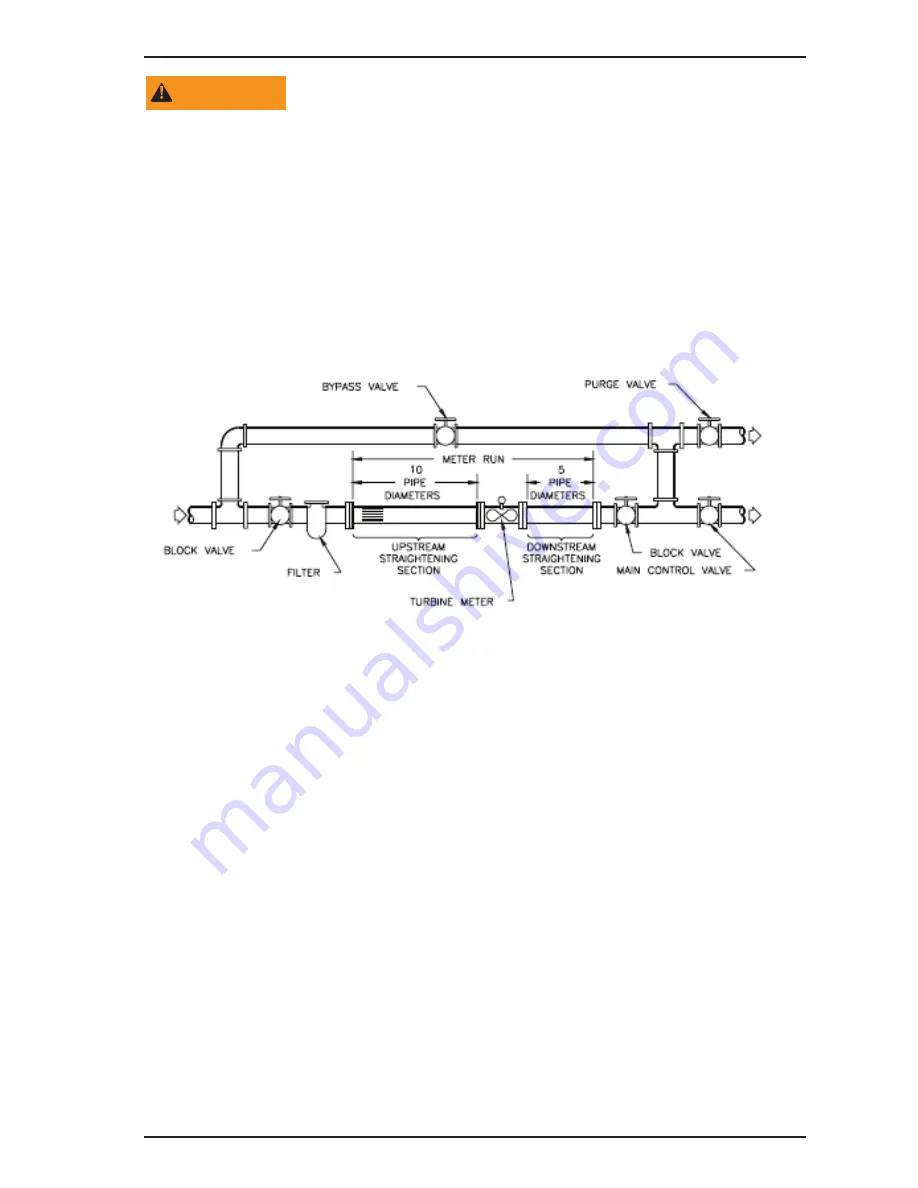
Installation
Page 7
TRB-UM-00478-EN-01
September 2018
WARNING
MAKE SURE TO PURGE ALL FLOW LINES OF FOREIGN OBJECTS AND DEBRIS
PRIOR TO INSTALLING A FLOW METER TO AVOID BEARING CONTAMINATION
OR ROTOR DAMAGE. DO NOT PURGE LINES WITH THE FLOW METER
INSTALLED OR IRREPARABLE DAMAGE IS HIGHLY LIKELY TO OCCUR.
It is critical to avoid over-spinning the meter (operating at greater than the maximum flow
rate) Always select a meter sized appropriately for your application Entrained vapor or
gaseous state product in the metered fluid piping can also cause the rotor to over-spin
resulting in bearing damage Necessary precautions must be made by the end user to
address these two situations
Figure 2: Recommended flow meter installation for bearing diagnostics
Flow meters with threaded end connection (NPT or AN) should not be over tightened
when installed into the flow line This can deform the end connection of the flow meter
resulting in sealing issues and problems in performing routine maintenance Stainless steel
is relatively soft and can be damaged if not handled with care Liquid pipe thread sealant
is recommended for pipe thread applications as Teflon® tape often is pulled into the flow
stream, thereby contaminating the rotor bearings Copper conical seals (crush washers) are
recommended for use in AN style connections to protect the sealing surface, but are not
mandatory to attain a seal
Flow straighteners can be manufactured with stainless steel B-nuts The flow meter housing
is manufactured from stainless steel Use anti-seize to prevent galling and permanent,
irreparable damage to both items
To obtain accurate flow measurement, sufficient downstream pressure is required to
prevent flashing and/or cavitation The minimum downstream pressure is calculated using
the following equation:
Pressure
Minimum
= (Fluid Vapor Pressure × 1 25) + (Pressure Drop × 2)
Adjust downstream pressure using a control valve located downstream of the
metering assembly