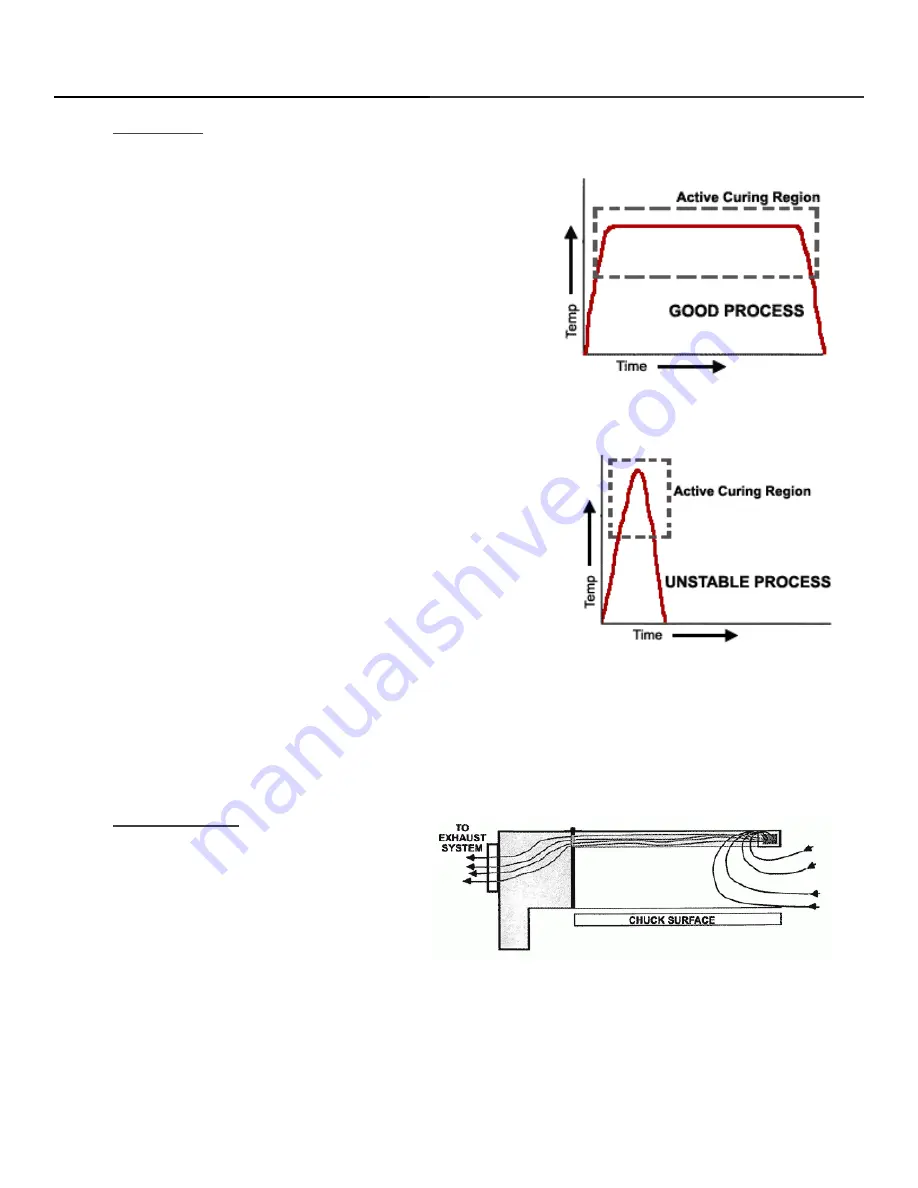
Cee® Apogee™ 300 Bake Plate Manual
Page
19
of
23
4.6. Bake Time
The selection of the bake time parameter plays an
important role in the reproducibility of the bake process.
Substrate thermal properties and the choice of bake
method greatly affect the amount of time necessary for the
substrate and therefore film temperature to stabilize during
the bake. Thicker substrates and the use of proximity bake
methods will increase the time necessary for the film to
reach its final temperature. It is important that most of the
baking action in the film takes place after this temperature
is reached. A silicon wafer will reach a stable temperature
within a few seconds and so it is traditional to adjust a
photoresist bake processes to be completed in 60-90
seconds with an appropriate bake temperature.
For thicker substrates such as photomasks and ceramic
modules the increased time necessary to heat the larger
mass of the substrate results in bakes times approaching
five minutes. It should be noted that these substrates can be
processed with higher temperature and much shorter bake
times but reproducibility may suffer. If the bake time is too
short then a significant amount of the actual bake process
will take place during the loading and unloading steps as
well as while the substrate is cooling after removal from the
bake plate. This is an unstable condition since it is very
difficult to exactly reproduce conditions during these steps.
In general the temperature-time relationship in a bake process can be taken as a "dose" of the
(temperature) x (time) product. Increasing the bake temperature results in a need for decreasing
bake time. The limits for
both
parameters can be reached when the process is no longer
reproducible or when the physical temperature limitations of the resin or substrate have been
reached.
4.7. Exhaust Cover
The design of the Cee® exhaust cover
promotes the dissipation of vapors
removed from a substrate placed on the
chuck, without drawing air across the
chuck surface.