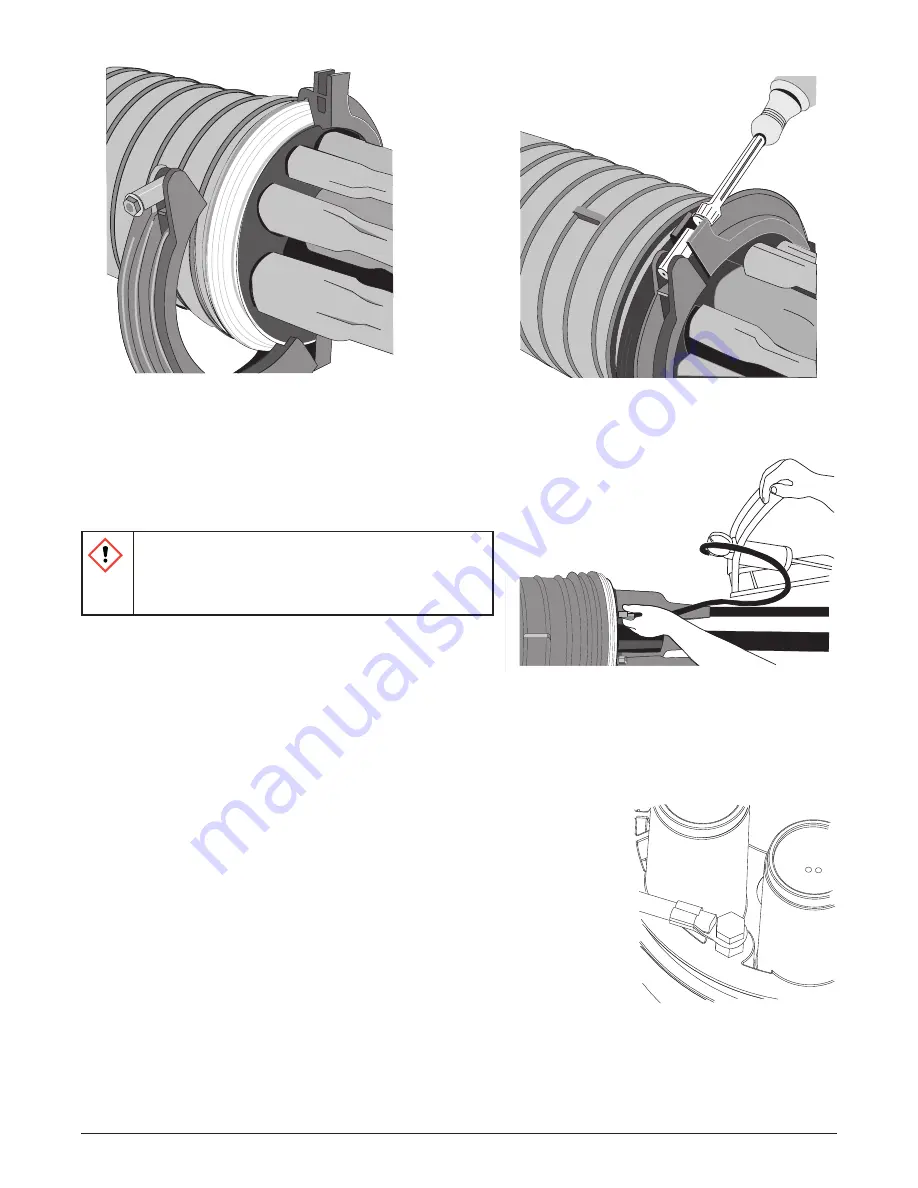
Standard Recommended Procedure 206-455-AEN | Issue 1 | November 2018 | Page 12 of 14
13. Perform Flash Test
Step 1:
Inject 12 to 14 psi (maximum) of air into the closure
. Check pressure after
each 25 pumps.
WARNING:
To avoid a potentially hazardous
situation that could result in death or serious
injury, do not exceed 14 psi (100 kpa) gauge
pressure. The closure could burst.
Step 2:
Apply soapy water to the edges of the heat-shrink
tubing and watch closure for signs of leakage
(bubbling of soap).
NOTE:
A correctly sealed closure maintains pressure with no leaks.
Step 3:
After the flash test has been performed and the closure sealed correctly, carefully remove the air valve
and allow air to escape.
14. Ground the Closure (Optional)
Step 1:
Apply a thin coat of lubricant retained previously to the threads of a
solid, two-piece, nonvented grounding plug
Step 2:
Install the larger plug into the end cap from the outside of the end cap
finger- tight, then another half turn (approximately 40 to 60 in-lb)
Step 3:
Connect a grounding cable (not supplied) to the plug.
Step 4:
Screw the smaller insert into the plug.
Step 5:
Tighten the insert using a small adjustable wrench.
Step 6:
Terminate the other end of the ground per local practices.
KPA-1723
KPA-1724
Figure 26
KPA-1726
Figure 27
TPA-5999
Figure 28