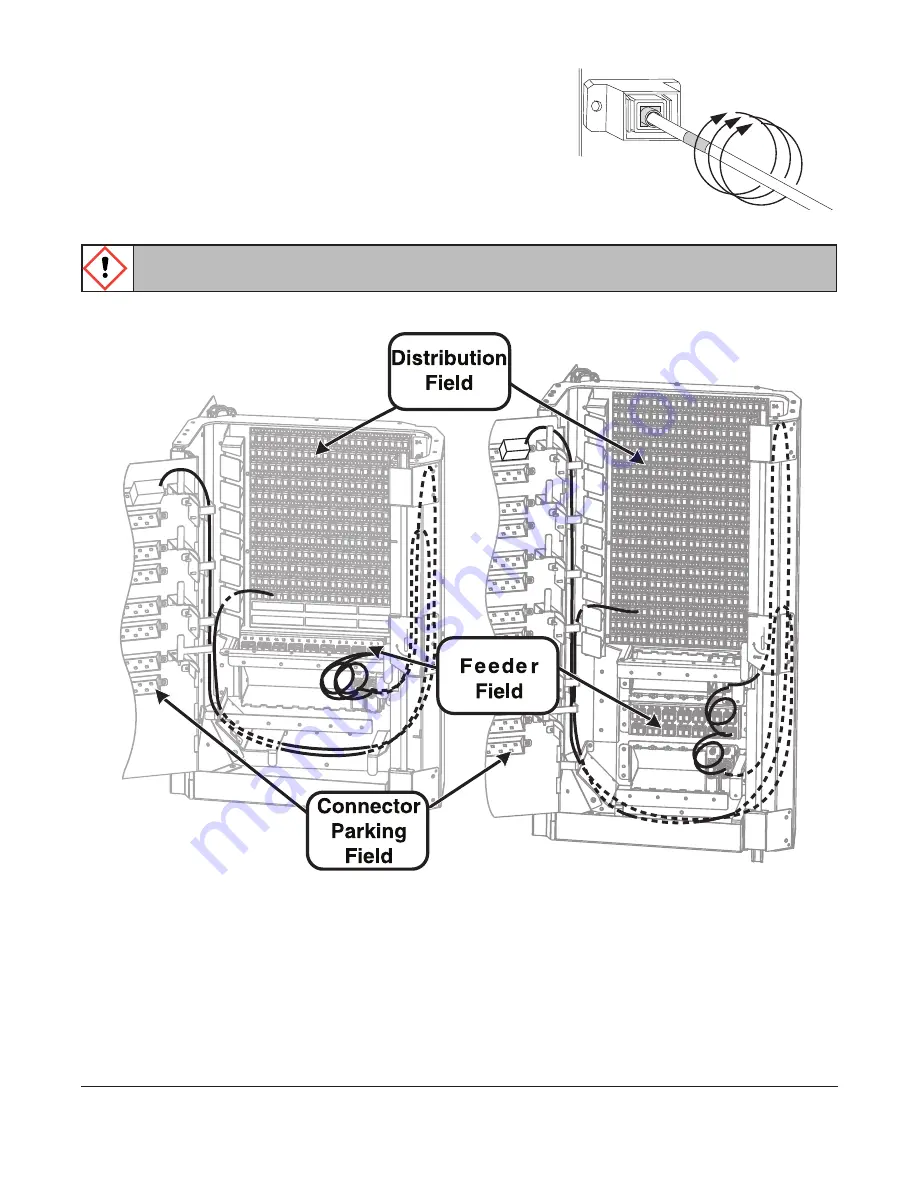
STANDARD RECOMMENDED PROCEDURE 003-737 | ISSUE 4 | MAy 2015 | PAGE 22 OF 25
Step 1:
Locate the feeder fiber port to be connected.
Lower the laser safety shutter and clean the
adapter using a dry process (Figure 32).
Step 2:
Verify with a power meter that the power is off to
the feeder fiber port to be connected. If power
to that port is on, turn it off at the central office
before proceeding.
Figure 32
In this application, making connections with the feeder power on may destroy the connector.
Step 3:
Route the connectorized splitter input fiber to the appropriate feeder port (Figure 33).
Figure 33
Step 4:
Remove the connector dust cap. Clean the connector end-face using a dry process,
such as with a cleaning cassette per your company’s cleaning procedures. Mate the
connector into the port.
Step 5:
Record the connector information on the label provided on the front door in the
feeder section of the label.
Step 6:
Power may now be turned on to the newly connected feeder port.
Cleaning stick
KPA-0705
KPA-0684