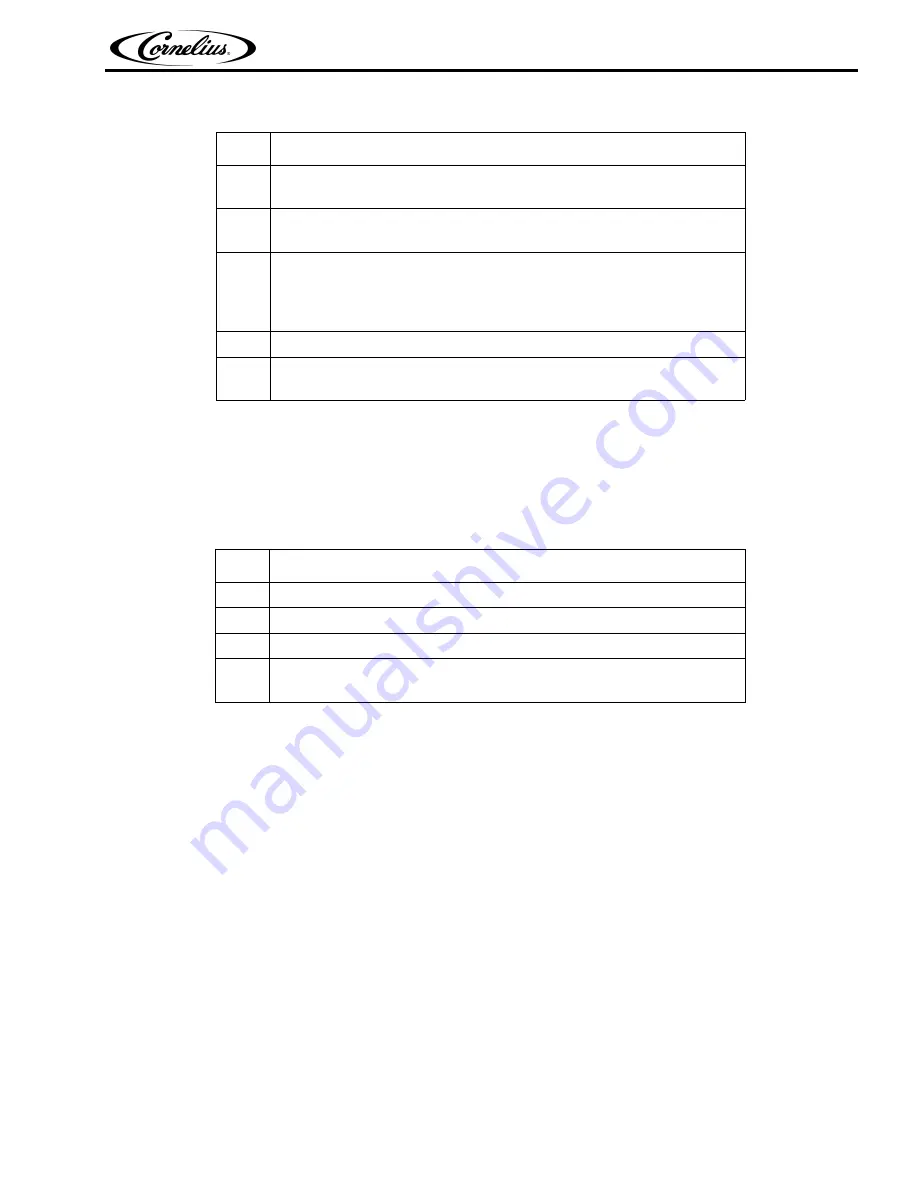
Viper Service Manual
© 2008-2015, Cornelius Inc.
- 45 -
Publication Number: 621260373SER
Cleaning the Syrup Connections
Syrup connections should be cleaned at least every six months, or when syrup types are changed. Perform the
procedure in Table 36. to clean the BIB connectors.
Servicing Motorman Dispensing Valves
NOTE:
Dispensing valves with caged o-rings should be serviced (lubricated) every 6 months or more frequently if the
valve lever gets tight to operate. Caged O-rings should be replaced every 12 months.
Refer to Figure 38 and perform the procedure in Table 37. to lubricate or change the caged o-rings in each dis-
pensing valve on the unit.
6.
If there is significant wear on the blades, Reverse or replace them, depending
on the wear pattern.
7.
Replace the blade assembly and bushings (PN 2392) onto the motor shaft in
the barrel.
8.
Re-install the faceplate and replace the four (4) mounting nuts. Hand tighten
the nuts until the faceplate makes contact with the gasket, then use a wrench
to tighten the nuts an additional 1/4 turn. Be careful not to over tighten the nuts
or cracking of the faceplate may result.
9.
Refill the barrel with product. See “Filling a Barrel” on page 32.
10.
When barrel fill is complete, perform a motor calibration. See “Calibrating a
Motor” on page 38.
Table 36.
Step
Action
1.
Open the merchandiser and select OFF for the barrel to be cleaned.
2.
Remove the quick disconnect from the BIB container.
3.
Fill a suitable pail or bucket with soap solution.
4.
Submerge the disconnect in the soap solution and then clean it using a nylon
bristle brush. (Do not use a wire brush). Rinse with clean water and dry.
Table 35.
Step
Action