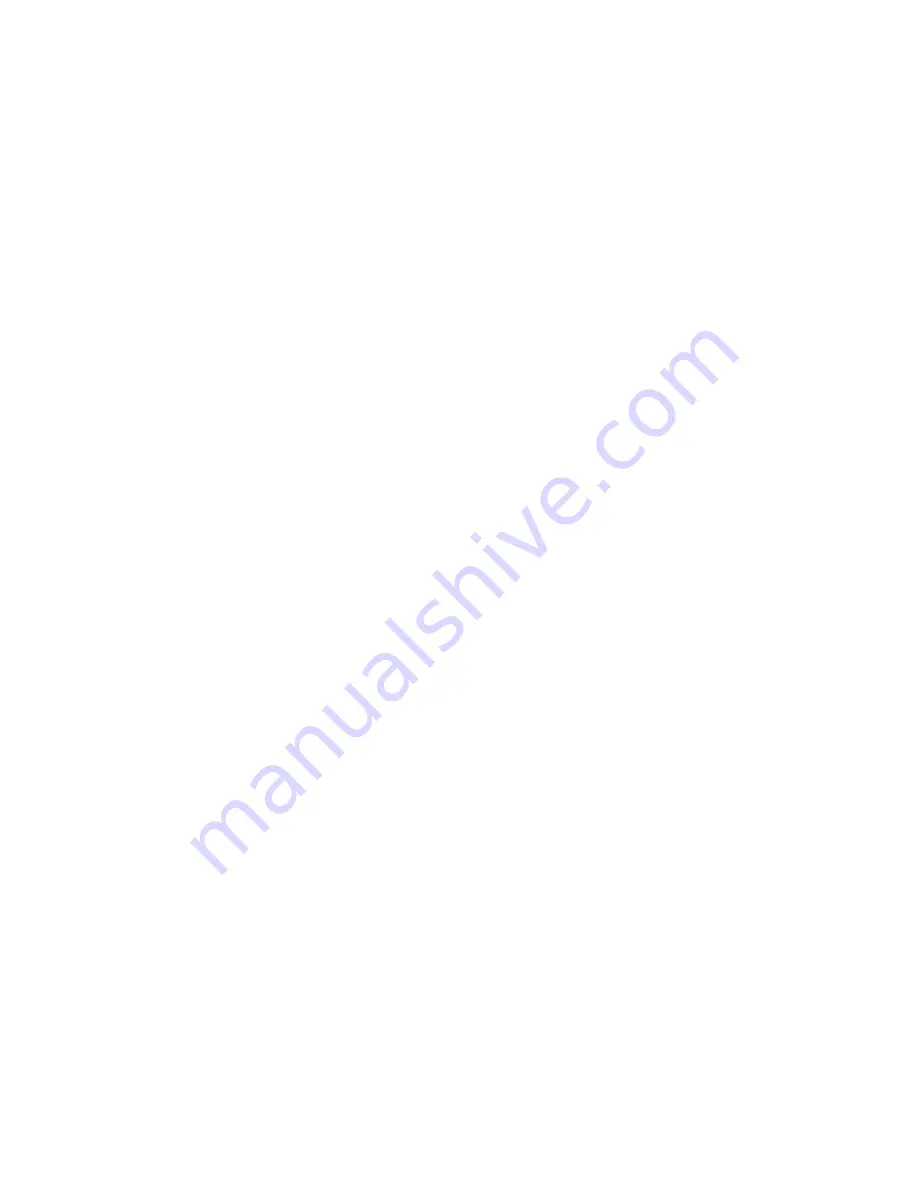
36
312026000
UNIT WITH WATER-COOLED REFRIGERATION SYSTEM
The high-pressure cutout switch, located inside the lower control box (see Figure 16), will shut the Unit
refrigeration system down when overheated (high head pressure) caused by lack of cooling water. After problem
has been corrected and the head pressure has decreased, the reset button on the high-pressure cutout switch
must be pressed to restart the refrigeration system.
ADJUSTMENTS
ADJUSTING PLAIN WATER PRESSURE REGULATOR
(see Figure 2 and 13)
The carbonator water pump plain water inlet adjustable water pressure regulator is factory adjusted to 45-psi
and should not be readjusted.
ADJUSTING CARBONATED WATER FLOW RATE
The carbonated water flow regulators (see Figure 2 and 5), which control carbonated water flow rate into the
product blender tanks, are factory adjusted for a flow rate of 1.3
±
0.05 ounces per second and normally do not
require adjustment. However, if adjustment is necessary, proceed as follows:
1. Press applicable ‘‘OFF 1’’ or ‘‘OFF 2’’ switch to prevent more product from entering the applicable product
blender tank.
2. Disconnect Unit syrup inlet line from the applicable soft drink tank.
3. Remove applicable side panel from the Unit as instructed for access to the applicable carbonated water
flow regulator, product shutoff valve, and product sample valve.
4. Close applicable product shutoff valve to prevent more product from entering the freeze cylinder.
5. Place container under applicable product sample valve. Open the valve and allow all product to be purged
from the product blender tank, then close the valve.
6. Remove the lower front access panel as instructed for access to the secondary CO
2
regulators.
7. Note pressure setting on the applicable secondary CO
2
regulator with 60-psi gage for the applicable
product blender tank. Turn regulator adjusting screw out (counterclockwise) until gage reads 0-psi. Pull up
on the applicable product blender tank relief valve to release CO
2
pressure from the tank.
8. Disconnect carbonated water line from the outlet side of the applicable carbonated water flow regulator.
9. Connect line, long enough to reach to the outside of the Unit, to the water flow regulator outlet, then route
the line to the outside of the Unit.
10. Place end of the carbonated water line, routed to the outside of the Unit, in the container.
11. Press applicable ‘‘AUTO BLEND 1’’ or ‘‘AUTO BLEND 2’’ switch to activate the electrically operated
carbonated water solenoid.
12. When steady stream of water is flowing from the added length of line, catch carbonated water in a
container graduated in ounces for exactly 10-seconds. Press applicable ‘‘FILL 1’’ or ‘‘FILL 2’’ switch to
deactivate the carbonated water solenoid. In 10-seconds, 12 to 14-ounces of water should have been
dispensed.
13. If adjustment is necessary, turn the carbonated water flow regulator adjusting screw to the left
(counterclockwise) to reduce carbonated water flow rate or turn the screw to the right (clockwise) to
increase the flow rate.
Summary of Contents for FCB 3 H.P. POST-MIX DISPENSER
Page 23: ...16 312026000 THIS PAGE LEFT BLANK INTENTIONALLY...
Page 69: ......
Page 70: ...62 312026000 FIGURE 17 WIRING DIAGRAM 3584 Rev C...