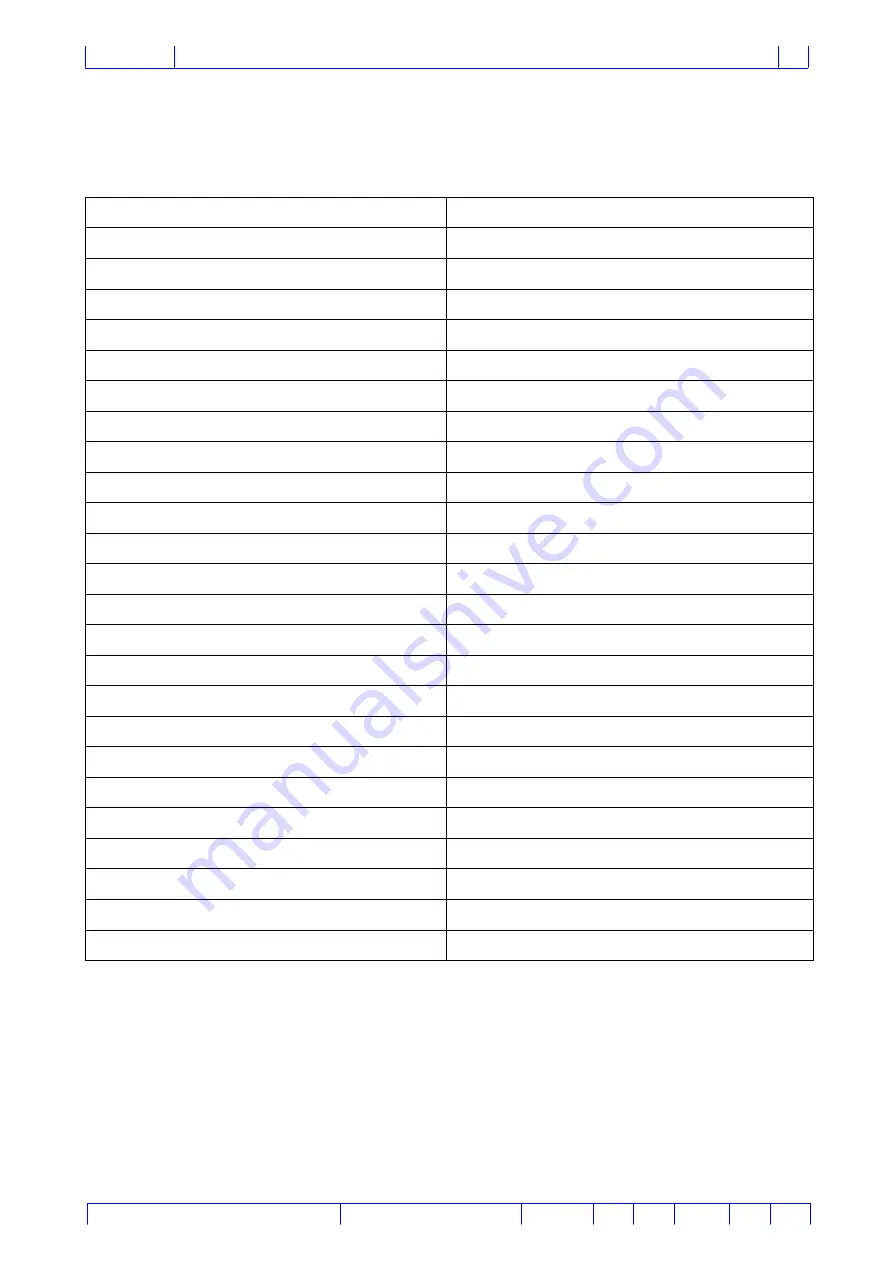
UT
Handbook for Use and Maitenance – 50000 WB-80-87-95
Edition
01/11
Revisione
00
6
50000WB_e111_E.doc
IDENTIFICATION OF THE MAIN CRANE COMPONENTS
The major crane components are listed below in order to make, the reading and
understanding of the operator’s manual easier.
LIST OF MAIN COMPONENTS
:
1 Right outrigger beam
26
2 Stabilising cylinder
27
3 Crane control valve
28
4 3 point linkage
29 Fitting bolts
5 Basement (chassis)
30 Top fitting plate
6 Control station
31 Bottom fitting plate
7 Left outrigger beam
32 Fitting nut
8 Screws of bearing inner ring
33 Power take off
9 Screws of bearing outer ring
34 Shaft
10 Bearing
35 Pump
11 Main lifting cylinder
36
12 Column
37 Hydraulic load limiting device
13 Main boom
38 Hydraulic load limiting device
14 Hydraulic oil tank
39
15 Second (knukle) boom cylinder
40
16 Second boom
41 Sub frame
17 JIB boom extension cylinder
42 Vehicle chassis
18 Acces stairs
43 Grab suspension
19 Joystick
20 Foot pedals
21 Hydraulic extensions
22 Lifting capacities sticker
23 Outriggers looks
24 Links
25 Main boom extension cylinder