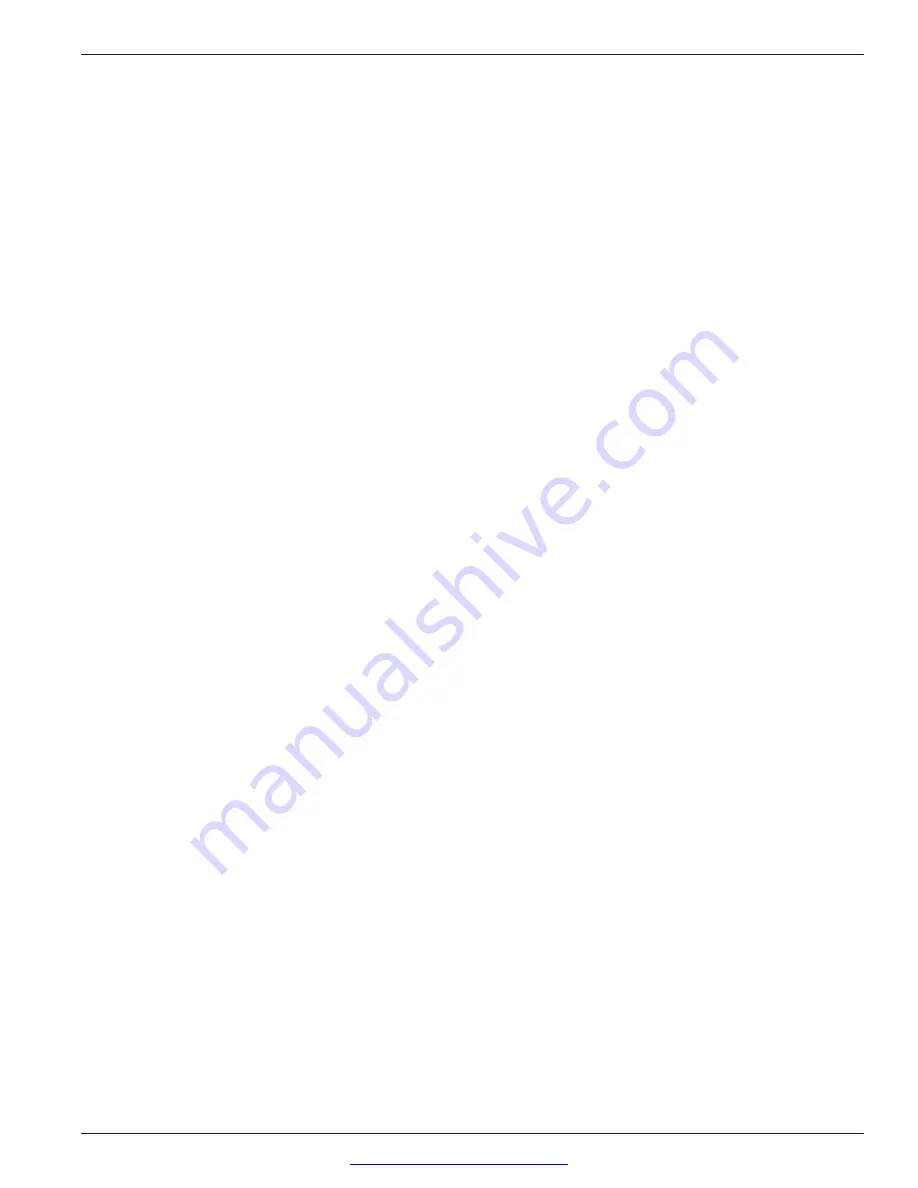
2.3 Installation Design Criteria For
Underground Tank Applications
Minimize frictional losses:
• Pump should be as close as possible to the tank’s liquid
outlet connection
• Use a minimal number of fittings and elbows
• No strainer is necessary since the tank itself acts as a
gravity collector
• Use full-port ball valves, or low restriction valves
• Use at least the minimum piping sizes shown in
Appendix I
• Minimize the net static suction lift to approximately 14
feet (4.3 M)
• Use vapor eliminator valves (Corken B166 by-pass
valves have this feature)
• Use back-pressure check valves downstream of the pump
• Vent the vapor eliminator on the liquid meter back to the
tank, not to the by-pass line
• Limit the capacity of the pump to a maximum of 1.5%
of the tank’s capacity or a 1000 Gal (3,785 L) tank, limit
the capacity of the pump to 15 gpm (56.8 L/min)
See Appendix I for piping diagram.
Chapter 3—Preventative Maintenance
for Your Coro-Flo
®
Pump
The only maintenance necessary on this pump is to
lubricate the bearings about once every six months.
The bearings have been lubricated at the factory for the
initial operation.
Lubrication for models C10, C12, C13 and C14:
These models are equipped with lifetime lubricated bearings.
Lubrication for models DL, DLF, DS, DSF, F, and FF in
pump sizes 9, 10, 12, 13, 14, and 15:
There are two bearings on the pump frame of these models
that require lubrication. In addition, if the pump is driven by a
motor there may be two bearings on the motor to lubricate at
the same time you lubricate the pump bearings. If the driver
is an engine, follow the engine manufacturer's instructions.
Lubricating the ball bearing is simple. Use ball bearing
grease only to lubricate the pump shaft bearing – nothing
else will do.
Older models without a grease zerk: Remove the plug
over the bearings, add a small amount of grease. With
the plug removed, run the pump and driver for several
minutes. The bearings will pump out the excess grease.
Replace the plug.
Newer pump models with a grease zerk: Remove the
lubricap covering the grease zerk and attach a grease
gun to the grease zerk. Add a small amount of grease and
cover the grease zerk with the lubricap.
Chapter 4—Repair Service on Your
Coro-Flo
®
Pump
After a long service life, repairs are limited to replacing the
impeller or mechanical seal.
The only wearing part influencing the pumping action
is the impeller, so we suggest the pump be given an
“efficiency” test before any attempt is made to repair
it. The trouble may lie in the piping system rather than
in the pump. If the pump will still produce as much
differential pressure when circulating through the bypass
system as it did when new, you may be sure your
problem is elsewhere. If the pump does not produce
as much pressure as it did originally, remove the cover
and inspect the impeller. If visual inspection indicates
the impeller is in good condition, remove one thin shim
gasket and replace the cover. Many times this procedure
will adjust for slight impeller wear. If the impeller is badly
damaged, it must be replaced (see step 32 in the seal
replacement instructions).
This is a matter of removing the cover and removing the
old impeller from the shaft. If the old impeller is tight on
the shaft, threaded bolt holes are provided in the impeller
to use for pulling. The new impeller must be a good slip
fit on the shaft; it should “float” on the shaft, so it may be
necessary to sand the shaft lightly to get the proper fit.
9
www.northridgepumps.com