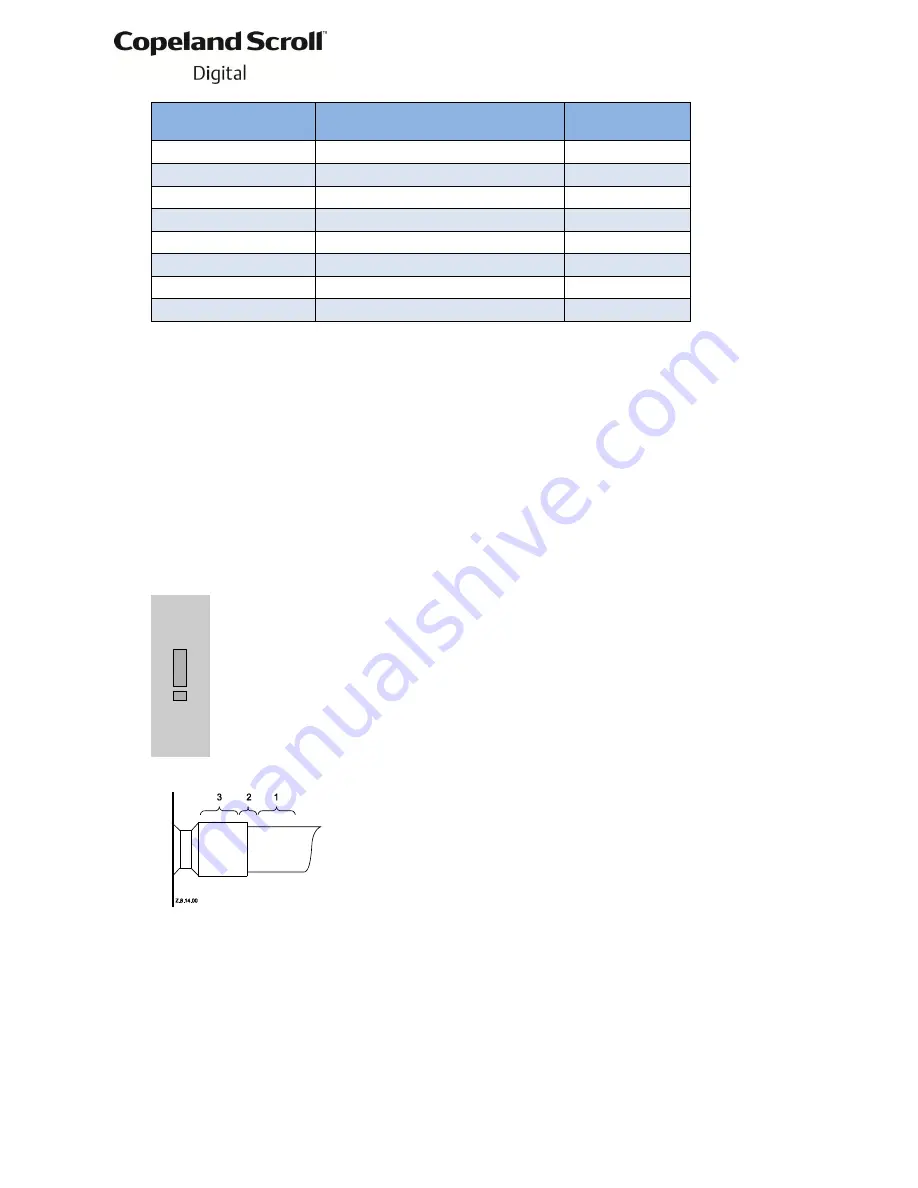
14
C6.2.15/0815/E
Figure 23: Suction tube brazing areas
Compressor model
Base compressors
Available
voltages
ZPDT21MCE
ZP ZPD103KCE
TFD
ZPDT22MCE
ZP ZPD104KCE
TFD
ZPDT24MCE
ZP ZPD120KCE
TFD
ZPDT25MCE
ZP ZPD122KCE
TFD
ZPDT27MCE
ZP ZPD137KCE
TFD
ZPDT31MCE
ZP ZPD154KCE
TFD
ZPDT36MCE
ZP ZPD182KCE
TFD
ZRDT25MCE
ZR ZRD125KCE
TFD
Table 2: Tandem configurations with standard models and Digital Scroll compressors
3.5 Discharge check valve
There is
no
discharge check valve at the discharge port of Copeland Scroll Digital compressors
ZRD42K* to ZRD81K* and ZPD34K* to ZPD91K* since the high-side pressure is needed to
support the operation of the un-loader mechanism.
To avoid bypassing during the unloading process back to suction, a dynamic discharge valve is
fitted internally on the discharge port of the fixed scroll. This discharge valve cannot be used with
recycling pump-down because it is not leak-proof during the off period.
Models ZRD94K*, ZRD125K* and ZPD103K* to ZPD182K* work with an internal un-loader
mechanism (see
Figures 5 & 11
) and are equipped with a check valve in the discharge fitting
that will prevent backward flow of gas through the scroll when the compressor shuts off.
3.6 Brazing procedure
IMPORTANT
Blockage! Compressor breakdown!
Maintain a flow of oxygen-free
nitrogen through the system at very low pressure during brazing. Nitrogen
displaces the air and prevents the formation of copper oxides in the system.
If allowed to form, the copper oxide material can later be swept through the
system and block screens such as those protecting capillary tubes, thermal
expansion valves, and accumulator oil return holes.
Contamination or moisture!
Bearing failure!
Do not remove the plugs until
the compressor is set into the unit. This minimises any entry of contaminants
and moisture.
Copeland Scroll Digital compressors have copper-
plated steel suction and discharge tubes. These
tubes are far more robust and less prone to leaks
than copper tubes. Due to the different thermal
properties of steel and copper, brazing procedures
may have to be changed from those commonly used.
Refer to
Figure 25
and the procedure below for the
brazing of the suction and discharge lines to a scroll
compressor.
The copper-coated steel tubes on scroll compressors can be brazed in approximately the
same manner as any copper tube.
Recommended brazing materials: any Silfos material is recommended, preferably with a
minimum of 5% silver. However, 0% silver is acceptable.
Be sure tube fitting inner diameter and tube outer diameter are clean prior to assembly.
Using a double-tipped torch, apply heat in area 1.
As the tube approaches brazing temperature, move the torch flame to area 2.