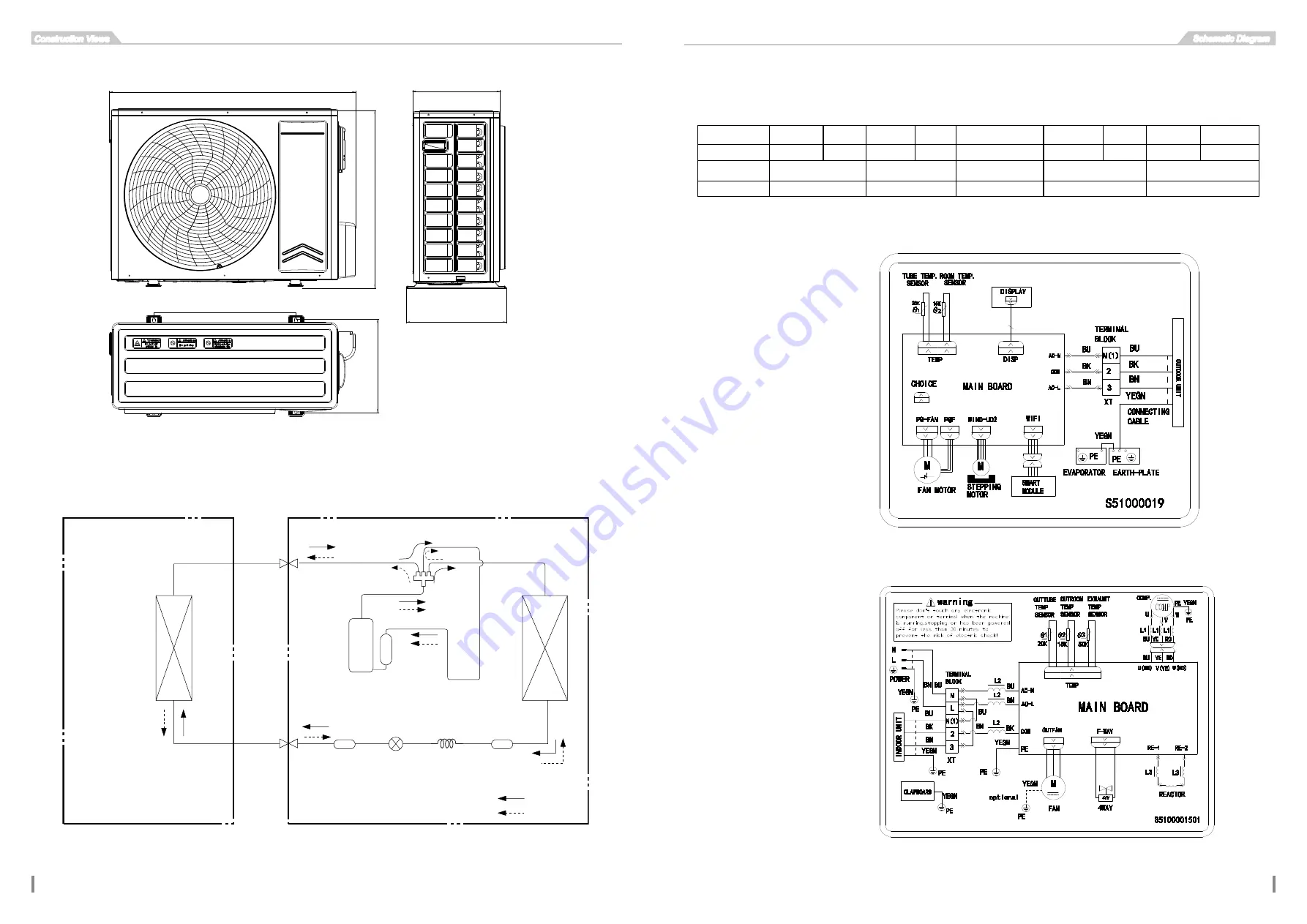
11
Schematic Diagram
10
Construction Views
4. Refrigerant System Diagram
Indoor unit
Outdoor unit
COOLING
HEATING
4-Way valve
Discharge
Suction
Heat
exchanger
(evaporator)
Heat
exchanger
(condenser)
Valve
Valve
Liquid pipe
side
Gas pipe
side
Strainer Electron
expansion
valve
Strainer
Capillary
Accumlator
Compressor
Refrigerant pipe diameter
Liquid :1/4" (6 mm) Gas : 3
/8" (9.52mm)(9
、
12K); 1/2"(12mm)(18K); 5/8"(16mm)(24K)
5. Schematic Diagram
5.1 Electrical Wiring
Symbol
OG
WH
YE
RD
YEGN
BN
BU
BK
VT
Color symbol ORANGE WHITE YELLOW
RED
YELLOW GREEN
BROWN
BLUE
BLACK
VIOLET
Symbol
COMP
CT1,2
4V
XT
Parts name
COMPRESSOR
OVERLOAD
4-WAY VALVE
TERMINAL BLOCK
PROTECTIVE EARTH
Meaning of marks
Model
(
outdoor
)
:CH-S09FTXC
CH-S12FTXC
CH-S18FTXC
CH-S24FTXC
These circuit diagrams are subject to change without notice, please refer to the one supplied with the unit.
Model
(
indoor
)
:CH-S09FTXC
CH-S12FTXC
CH-S18FTXC
CH-S24FTXC
960
340
700
368
560
396
Model:CH-S24FTXC