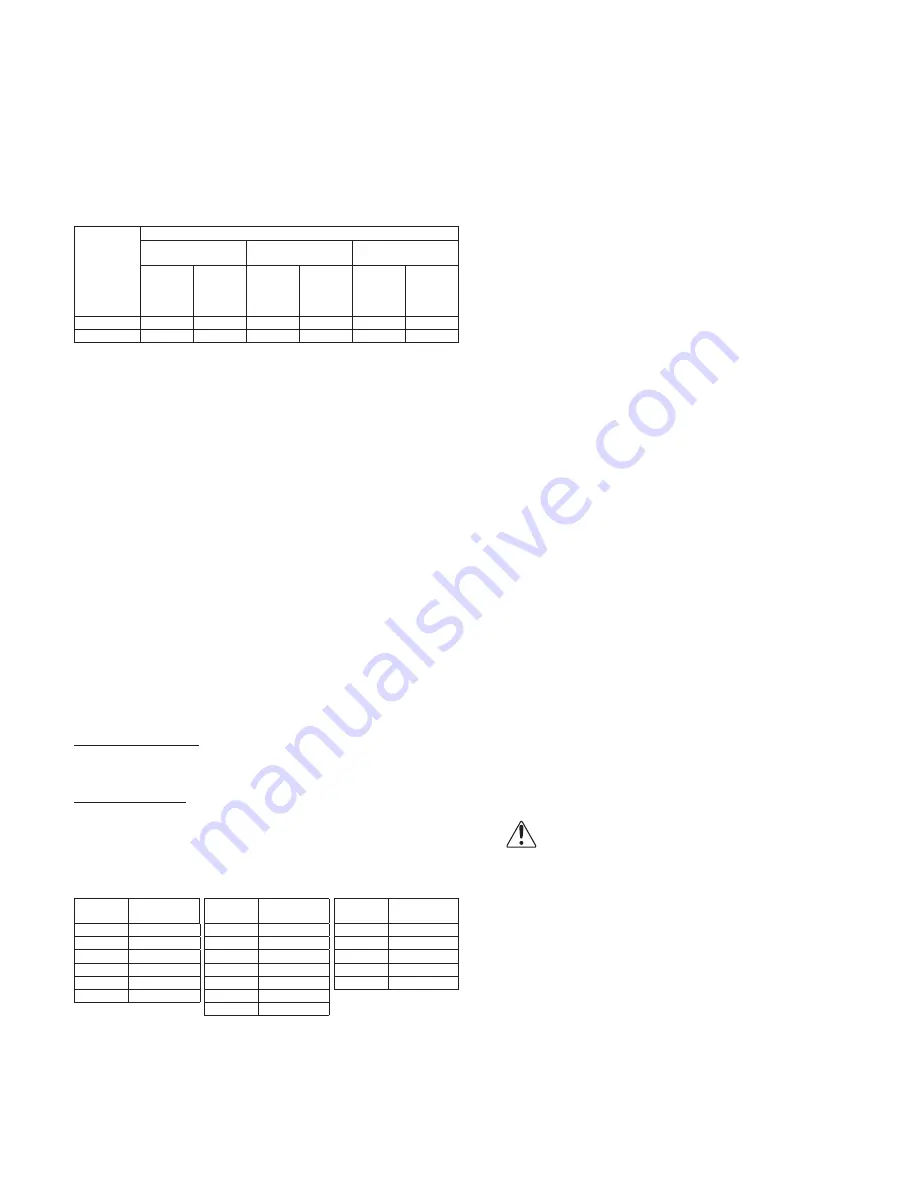
5
DB IO&M
B51131-002
Motors without sleeve bearings (as described previous-
ly) will have grease lubricated ball or roller bearings. Motor
bearings without provisions for relubrication will operate
up to 10 years under normal conditions with no mainte-
nance. In severe applications, high temperatures or exces-
sive contaminates, it is advisable to have the maintenance
department disassemble and lubricate the bearings after
three years of operation to prevent interruption of service.
For motors with provisions for relubrication, follow inter-
vals of the table below.
Relubrication Intervals
Service
Conditions
NEMA Frame Size
Up to and
Including 184T
213T–365T
404T and Larger
1800
RPM and
Less
Over
1800
RPM
1800
RPM and
Less
Over
1800
RPM
1800
RPM and
Less
Over
1800
RPM
Standard
3 years 6 months 2 years 6 months
1 year
3 months
Severe
1 year
3 months
1 year
3 months 6 months 1 month
Motors are provided with a polyurea mineral oil NGLI #2
grease. All additions to the motor bearings are to be with
a compatible grease such as Exxon Mobil Polyrex EM and
Chevron SRI.
The above intervals should be reduced to half for verti-
cal shaft installations.
Motor Services
Should the motor prove defective within a one-year pe-
riod, contact your local Loren Cook representative or your
nearest authorized electric motor service representative.
Changing Shaft Speed
All belt driven Propeller Wall fans with motors up to and
including 5HP are equipped with variable pitch pulleys. To
change the fan speed, perform the following:
1. Loosen setscrew on driver (motor) pulley and remove
key, if equipped.
2. Turn the pulley rim to open or close the groove facing.
If the pulley has multiple grooves, all must be adjusted
to the same width.
3. After adjustment, inspect for proper belt tension.
Speed Reduction
Open the pulley in order that the belt rides deeper in the
groove (smaller pitch diameter).
Speed Increase
Close the pulley in order that the belt rides higher in the
groove (larger pitch diameter). Ensure that the RPM lim-
its of the fan and the horsepower limits of the motor are
maintained.
Maximum RPM
SDB
Size
Maximum
RPM
100
2795
120
2486
135
2281
150
2088
180
1727
210
1399
245
1284
TDB
Size
Maximum
RPM
9
1469
10
1382
13
1094
15
1030
18
907
DB/DBX
Size
Maximum
RPM
8
1494
9
1594
10
1382
13
1094
15
973
18
906
Pulley and Belt Replacement
1. Clean the motor and fan shafts.
2. Loosen the motor plate mounting bolts to relieve the
belt tension. Remove the belt.
3. Loosen the pulley setscrews and remove the pulleys
from the shaft.
• If excessive force is required to remove the pulleys, a
three-jaw puller can be used. This tool, however, can eas-
ily warp a pulley. If the puller is used, inspect the trueness
of the pulley after it is removed from the shaft. The pulley
will need replacement if it is more than 0.020” out of true.
4. Clean the bores of the pulleys and place a light coat of
oil on the bores.
5. Remove grease, rust and burrs from the shaft.
6. Place fan pulley on the fan shaft and the motor pulley
on the motor shaft. Damage to the pulleys can occur
when excessive force is used in placing the pulleys on
their respective shafts.
7. After the pulleys have been correctly placed back onto
their shafts, tighten the pulley setscrews.
8. Install the belts on the pulleys. Align and adjust the
belts to the proper tension as described in
Belt and
Pulley Installation
, page 3.
Bearing Replacement
If you have a model DB or TDB, the fan bearings are
permanently sealed and will not require replacement.
If you have a model SDB or DBX, the fan bearings are
pillow block ball bearings. Follow the instructions below for
replacement.
1. Loosen screws on bearing cover.
2. Push bearing cover toward the wheel. As the bearing
cover moves toward the wheel, it will slide down to re-
veal the bearings and shaft.
3. Remove the old bearing.
4. Remove any burrs from the shaft by sanding.
5. Slide new bearings onto the shaft to the desired lo-
cation and loosely mount bearings onto the bearing
support. Bearing bolts and setscrews should be loose
enough to allow shaft positioning.
6. Correctly position the wheel and tighten the bearing
bolts securely to the bearing support.
7. Align setscrews bearing to bearing and secure tightly
to the shaft.
NOTICE! Never tighten both pairs of setscrews be
-
fore securing bearing mounting bolts. This may
damage the shaft.
8. Inspect the wheel position again. If necessary, re-
adjust by loosening the bearing bolts and setscrews
and repeat from step 5.