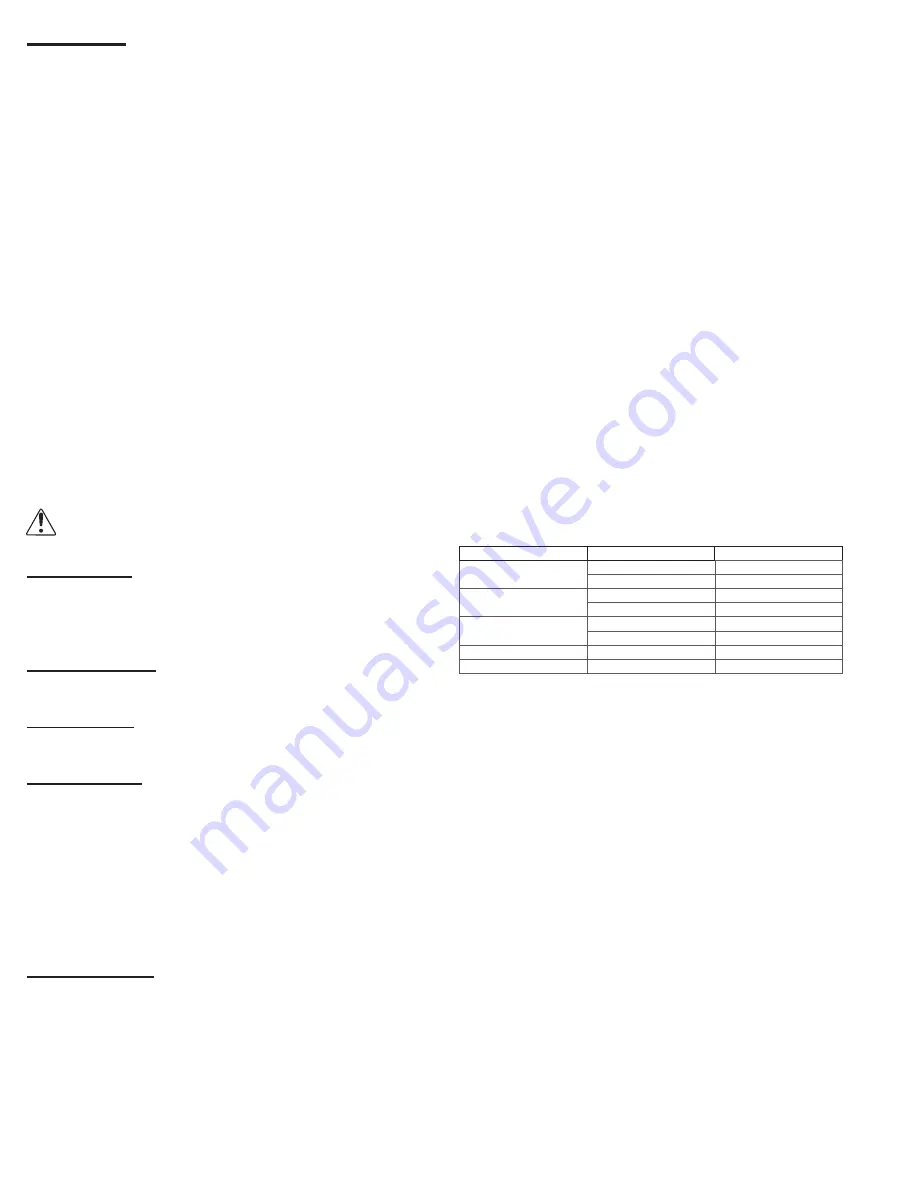
4
DB IO&M
B51131-002
Operation
Pre-Start Checks
1. Lock out all the primary and secondary power sources.
2. Inspect fasteners and setscrews, particularly those
used for mounting the fan, and tighten if necessary.
3. Inspect belt tension and pulley alignment. (Remember,
if belt tension is correct, a loud squeal occurs as the
fan increases to full power.)
4. Inspect motor wiring.
5. Ensure the belt touches only the pulleys.
6. Ensure fan and ductwork are clean and free of debris.
7. Test the fan to ensure the rotation of the wheel is the
same as indicated by the rotation label.
8. Close and secure all access doors.
9. Restore power to unit.
Start Up
Turn on the fan. In variable speed units, set the fan to its
lowest speed. Inspect for the following:
• Direction of rotation
• Excessive vibration
• Unusual noise
• Bearing noise
• Improper belt alignment or tension (listen for a continuous
squealing noise)
• Improper motor amperage or voltage
NOTICE! If a problem is discovered, immediately shut
off the fan. Lock out all electrical power and check
for the cause of the trouble. Refer to Troubleshooting.
Inspection
Inspection of the fan should be conducted at the first
30
minute
,
8 hour
and
24 hour
intervals of satisfactory op-
eration. During the inspections, stop the fan and inspect
as per directions below.
30 Minute Interval
Inspect bolts, setscrews and motor mounting bolts. Ad-
just and tighten as necessary.
8 Hour Interval
Inspect belt alignment and tension. Adjust and tighten
as necessary.
24 Hour Interval
Inspect belt tension. Adjust and tighten as necessary.
Filters (if included)
Filters should be inspected within the first two weeks of
operation. If there is no excessive build-up, monthly ser-
vicing should be adequate.
To clean reusable aluminum filters, back flush with soap
and water. When clean, shake off excess water and allow
the filter to air-dry before reinstalling it.
Maintenance
Establish a schedule for inspecting all parts of the fan.
The frequency of inspection depends on the operating
conditions and location of the fan.
Inspect fans exhausting corrosive or contaminated air
within the first month of operation. Fans exhausting con
-
taminated air (airborne abrasives) should be inspected ev-
ery three months.
Regular inspections are recommended for fans exhaust-
ing non-contaminated air.
It is recommended the following inspections be con-
ducted twice per year.
• Inspect bolts and setscrews for tightness. Tighten as
necessary
• Inspect belt wear and alignment. Replace worn belts with
new belts and adjust alignment as needed. See
Belt and
Pulley Installation
, page 3
• Bearings should be inspected as recommended in the
Conditions Chart
• Inspect for cleanliness. Clean exterior surfaces only. Re-
moving dust and grease on motor housing assures prop-
er motor cooling
Fan Bearings
The fan bearings are provided prelubricated. Any spe-
cialized lubrication instructions on fan labels supersedes
information provided herein. Bearing grease is a petro-
leum lubricant in a lithium base conforming to an NLGI #2
consistency. If user desires to utilize another type of lu-
bricant, they take responsibility for flushing bearings and
lines and maintaining a lubricant that is compatible with
the installation.
An NLGI #2 grease is a light viscosity, low-torque, rust-
inhibiting lubricant that is water resistant. Its temperature
range is from -30°F to 200°F and capable of intermittent
highs of 250°F.
Bearings should be relubricated in accordance with the
Conditions Chart
below.
Conditions Chart
RPM
Temp °F
Greasing Interval
Up to 1000
-30 to 120
6 months
120 to 200
2 months
1000 to 3000
-30 to 120
3 months
120 to 200
1 month
Over 3000
-30 to 120
1 month
120 to 200
2 weeks
Any Speed
< -30
Consult Factory
Any Speed
> 200
1 week
For moist or otherwise contaminated installations; divide the inter-
val by a factor of three. For vertical shaft installations divide the in-
terval by a factor of two.
For best results, lubricate the bearing while the fan is in
operation. Pump grease in slowly until a slight bead forms
around the bearing seals. Excessive grease can damage
seal and reduce life through excess contamination and/or
loss of lubricant.
In the event that the bearing cannot be seen, use no more
than three injections with a hand operated grease gun.
Motor Bearings
Motors are provided with prelubricated bearings. Any lu-
brication instructions shown on the motor nameplate su-
persede instructions below.
Direct Drive 1050/1075, 1200, 1300 and 1500 RPM units
use a prelubricated sleeve bearing that has an oil-saturat-
ed wicking material surrounding it. The initial factory lubri-
cation is adequate for up to 10 years of operation under
normal conditions. However, it is advisable to add lubri-
cant after three years. Use only LIGHT grade mineral oil
or SAE 10W oil up to 30 drops. If the unit has been stored
for a year or more, it is advisable to lubricate as directed
above. For VCR direct drive units and other units in severe
conditions, lubrication intervals should be reduced to half.