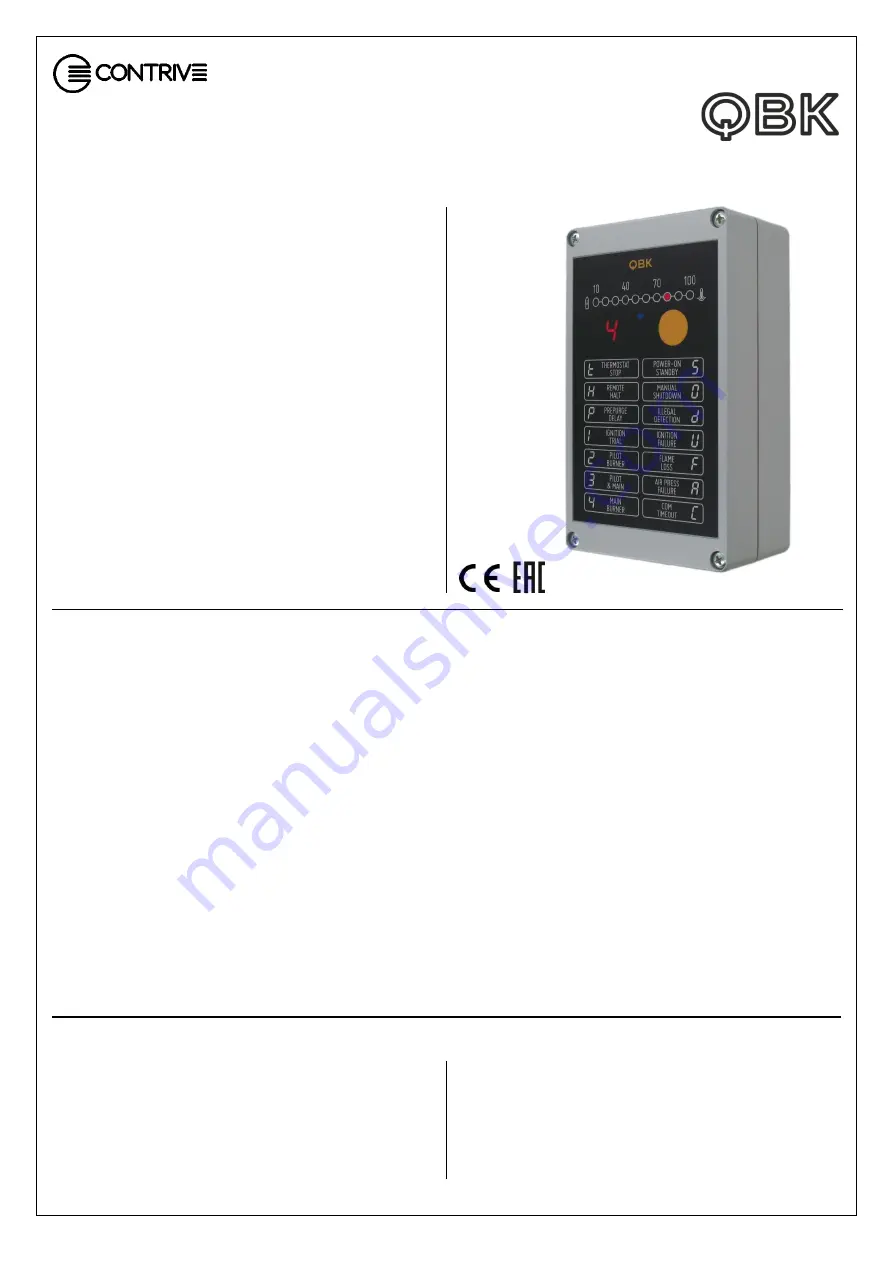
© 2016
CONTRIVE • B14
88|
QBK
.EN
0219
1
www.contrive.it
AUTOMATIC BURNER CONTROL SYSTEM
The burner control unit Q
BK [
cubic
] is suitable for the
control of pilot burners up to 350 kW and main
burners
of unlimited capacity, pursuant to EN 746
-2,
for intermittent or continuous operation.
Flame control by means of UV scanner or ionization
rod (even shared with ignition) and high-temperature
option for flame surveillance bypass.
Specific output for air valve or fan, following cycle or
independently controllable.
Times and cycle are configurable: the same device can
be used to control different types of gas and oil
burners, meeting all relevant requirements.
A led-bar flame signal indicator and an advanced self-
diagnostic system provides the display of either the
cycle status, lockouts and failures.
Remote control and supervision of the burner can be
implemented by means of traditional electrical wiring,
or through built-in communication line.
SAFETY INFORMATION
Read and understand this manual before installing, operating, or servicing this unit. This unit must be installed
according to this manual and local regulations. The drawings may show units without covers or safety shields to
illustrate details. Disconnect power supply and follow all usual safety precautions before carrying out any operation
on the device.
Be sure to reinstall covers or shields
before operating any devices.
The device is not user serviceable, a faulty device must be put out of order and sent back for servicing.
CONTRIVE manufactures products used as components in a wide variety of industrial systems and equipment. The
selection and application of products remain the responsibility of the equipment manufacturer or end user.
CONTRIVE accepts no responsibility for the way its products are incorporated into the final system design. All
systems or equipment designed to incorporate a product manufactured by CONTRIVE must be supplied to the end
user with appropriate warnings and instructions as to the safe use and operation of that part.
Any warnings provided by CONTRIVE must be promptly provided to the end user.
CONTRIVE guarantees for two years from the date of manufacture of its product to replace, or, at its option, to
repair any product or part thereof (except fuses and with some limitations for tubes and photocells) which is found
defective in material or workmanship or which otherwise fails to conform to the description of its sales order.
CONTRIVE makes no warranty of merchantability or any other warranty express or implied. CONTRIVE assumes no
liability for any personal injury, property damage, losses, or claims arising from misapplication of its products.
CERTIFICATION
Gas Equipment Directive (2009/
142
/EC)
Low Voltage Equipment Directive (
2014
/35/EC)
EMC Directive (
2014
/30/EC)
IN CONJUNCTION WITH:
EN298 –
EN746
-2 – EN60730-1 – EN13611
EU type certification
CE 0063CS1560
Eurasian Customs Union
MEETS TECHNICAL SPECIFICATIONS OF
RUSSIAN FEDERATION, BELARUS AND KAZAKHSTAN