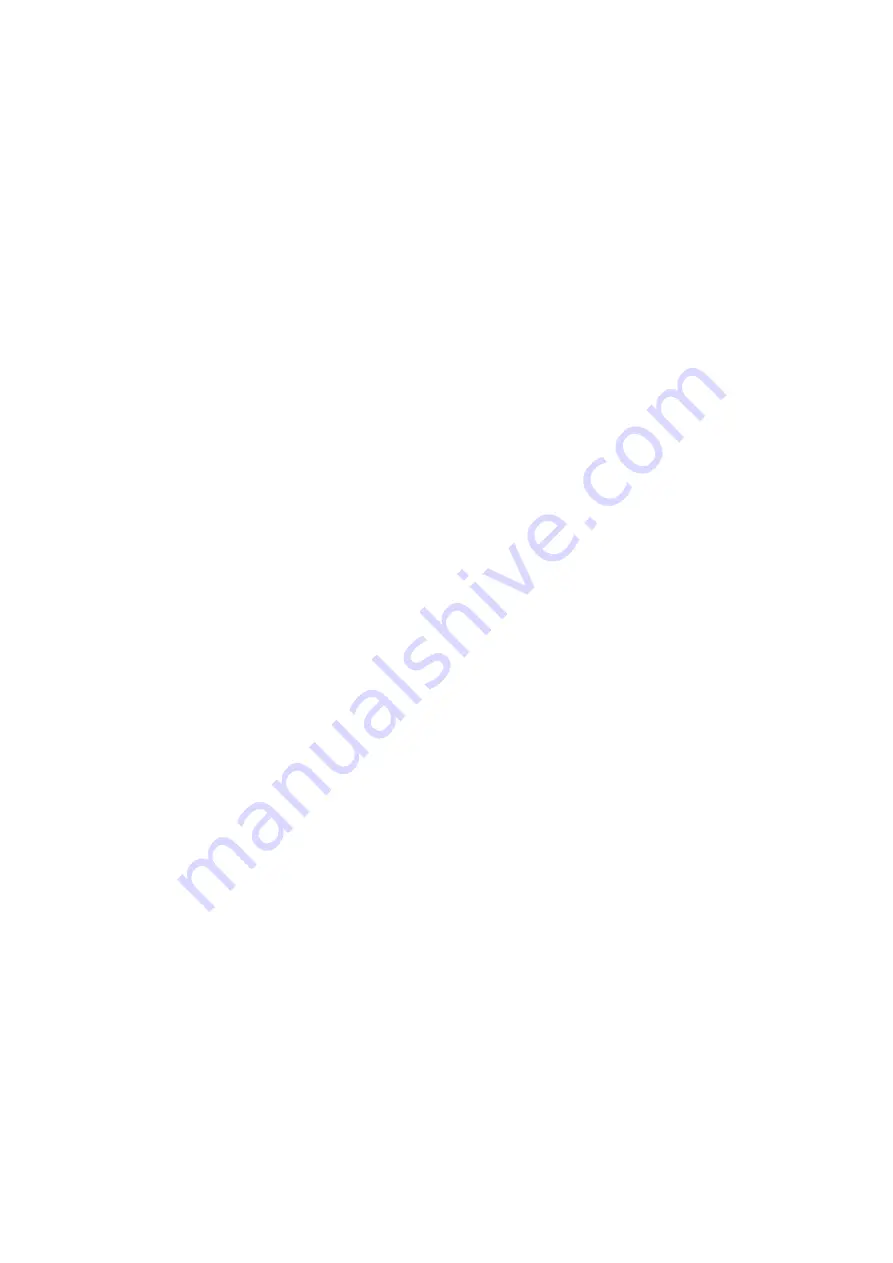
3.2.1 Control Relay Outputs
The two output relays can be set up to control a single valve or a dual valve with
slow stop and/or slow start. Alternatively, the second relay can be used to control
a pump.
The relay operation is shown on the previous two pages.
A time delay between the Start and the time when relay 2 energises can be
programmed to provide a soft startup. The delay can range from 0 (no delay) to
79 minutes and 59 seconds.
A Prestop quantity (ie. the quantity to the end of the batch) can also be
programmed to provide a slowdown of flow at the end of the batch, thereby
enabling precise quantities to be batched.
The process can be stopped at any time by pressing the STOP key, whereby both
relays will immediately de-energise. The process can then be aborted and the
batcher reset by pressing the STOP key again, or the process continued by
pressing the RUN key.
If the process is continued and the instrument was previously in the slow start or
main control phases (ie. not the prestop phase), the timer will be reset and a slow
start will occur with a full time delay to ensure a correct start up. The totals will
not be reset and the batch quantity will remain unchanged.
Operation 13
Summary of Contents for 414Q
Page 1: ...BATCH CONTROLLER MODEL 414Q July 2001 ...
Page 2: ......