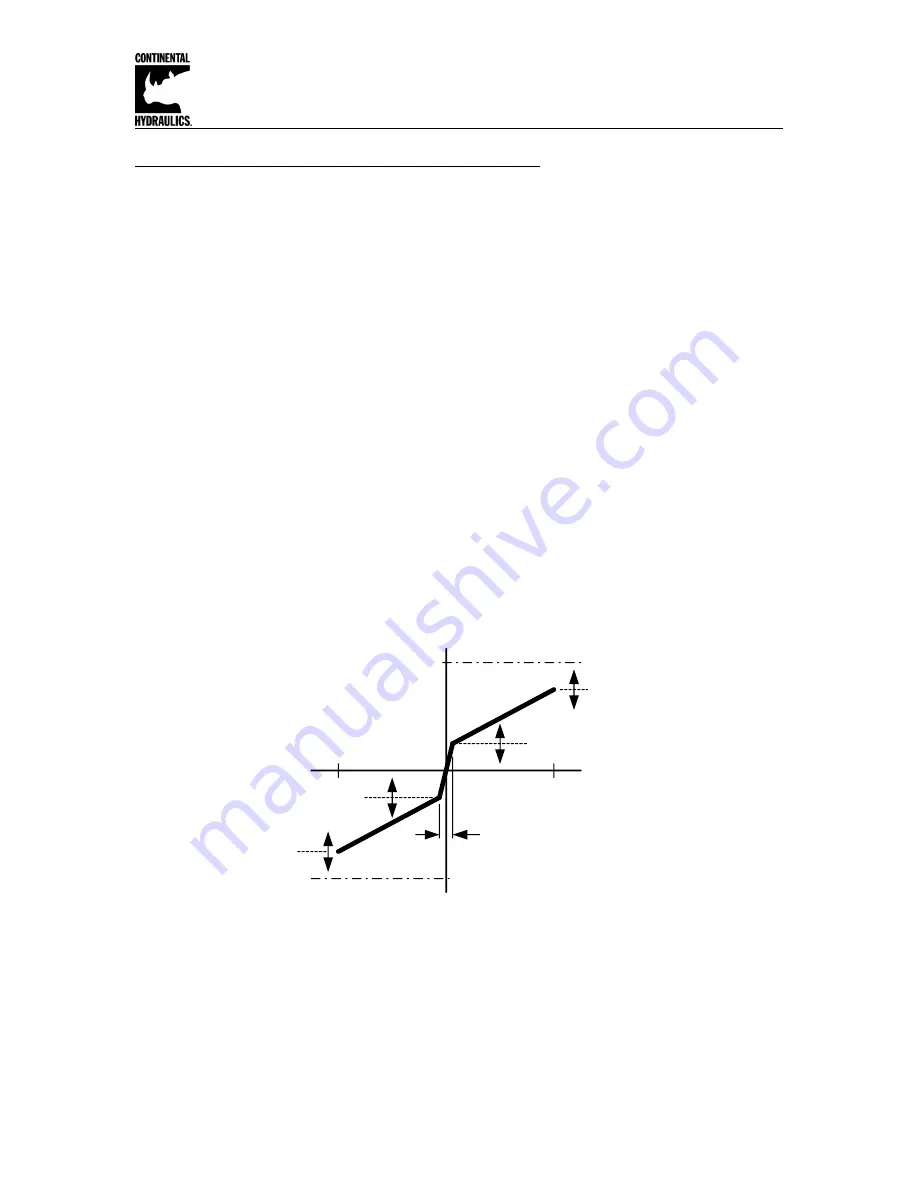
Continental Hydraulics Installation Manual
Page 8 of 15
CEM-MS-A
CHI 1013478 Jan 2013
Adjust module output to match valve requirements:
The CEM-MS module has a 0 to +/-10v differential output. This output is designed to directly
interface to proportional valves with on board electronics.
This output signal may be configured to more closely match the valve characteristics. The
parameters used to adjust the output signal include:
MAX:A and MAX:B
MIN:A and MIN:B
TRIGGER
MAX:A and MAX:B are set with software as a percentage of the 10v output. MAX:A and
MAX:B are set at 100% (10000) for a valve that has a 10v input rating. To reduce the maximum
flow from a valve with a spool that is too large, set MAX to a number less than 100%. Valid range
is from 5000 to 10000. Default is 10000. Units are 0.01%
MIN:A and MIN:B are adjusted via software for the purpose of deadband elimination. A valve
with a minimum control point (cracking point) will give best performance if this deadband is
eliminated. Valid range is 0 to 5000. Default is 0. Units are 0.01%.
Example: A directional control valve has an input range of 0 to +/-10v. The valve is
factory calibrated to begin flow at 1v, and max flow is at 10v. Adjust the CEM-SA parameters:
MAX:A = 10000 (100% of +10v)
MIN:A = 900 (9% of 10v = +0.9v)
MAX:B = 10000 (100% of -10v)
MIN:B = 900 (9% of -10v = -0.9v)
Min A =
% of Range
Max A =
% of Range
Voltage Output
+
10v
Trigger = % of Output
Module output +100%
Module output
-
100%
Min B =
% of Range
Max B =
% of Range
Voltage Output
-
10v
TRIGGER and MIN can be used together to optimize valve performance near zero.
When using a proportional valve with an overlap spool, adjust TRIGGER to 200 (2%), and MIN:A
and MIN:B to slightly less than the “crack point” of the valve.