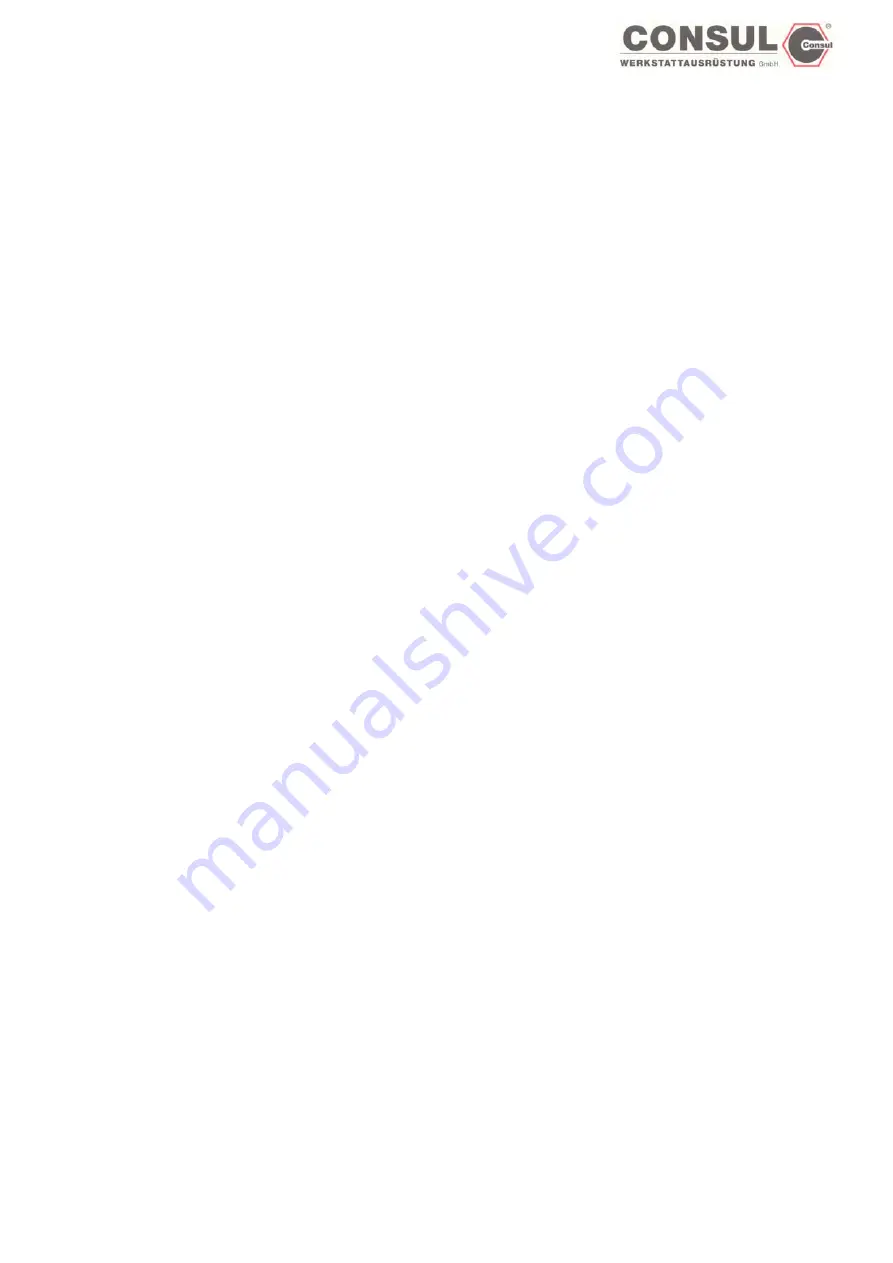
OPERATING & INSTALLATION INSTRUCTION 2-POST-LIFT
Maintenance general care
Before any maintenance the lift should be isolated from the electricity supply and protected from any
unauthorised use!
Thorough maintenance is essential if your lift is to have a long working lift and be constantly ready to give
good service.
In this respect special attention must be given to lubrication. The lifting spindles must be greased weekly
with Consul Spindle Oil. When the spindle is in the „down” position, brush the lifting spindle with oil. Where
lifts have spindle oilers (identification number: 34631.2) then the oil container on the carriage must be kept
full. At least once a month you should check that the oil provision is sufficient.
After installation and commissioning there may be some stretching of the power transmission elements,
depending on the type of lift. For example, stretching of the drive belt, chainds or calbes, consequential
adjustments, adjustments to the safety systems, etc. These changes do not constitue wear and tear of the
parts. They are routine aspects of running in and must form part of the customer’s maintenace and care.
With lack of care break downs can occur which are not occur which are not covered by the guarantee. In this
case, any costs airsing may have to be borne by the customer.
The swivel arm joints must be greased when necessary and at least quarter yearly (oil underneath the safety
screws). Where lifts are exposed to the weather, the lubrication programm should be doubled (see the
lubrication instructions on the main column).
The load bearing apparatus must always be kept in working condition. The buffer points must be kept clean
and greased-free. The spindles of the turntables must must be greased. They must not be able to unscrew
themselves completely.
Chain lifts:
One further point is the correct tensioning of the chains. Because of the initial stretching of the chain it is
necessary to retension these as required. Thi is not a sign of early wear. After a short running in time the
chain generally requires retensioning.
The retensioning of the chain (only with tension lifts! ) is an item of maintenance which must be carried out
by the customer as and when necessary.
Damages which occurs when the lift is operated with an overslack chain will invalidate the guarantee. The
tensioning of the chain is to be carried out according to the instructions for assembly. The chain glide units
should be stored clean and in well-greased conditions (to be checked quarter yearly).
Page 53
Summary of Contents for 2.25 EMC
Page 67: ...OPERATING INSTALLATION INSTRUCTION 2 POST LIFT Electric diagram H342 Page 67 ...
Page 68: ...OPERATING INSTALLATION INSTRUCTION 2 POST LIFT Electric diagram H325 Page 68 ...
Page 70: ...OPERATING INSTALLATION INSTRUCTION 2 POST LIFT Electric diagram with push button Page 70 ...
Page 71: ...OPERATING INSTALLATION INSTRUCTION 2 POST LIFT Page 71 ...
Page 72: ...OPERATING INSTALLATION INSTRUCTION 2 POST LIFT Page 72 ...
Page 73: ...OPERATING INSTALLATION INSTRUCTION 2 POST LIFT Page 73 ...
Page 74: ...OPERATING INSTALLATION INSTRUCTION 2 POST LIFT Page 74 ...
Page 75: ...OPERATING INSTALLATION INSTRUCTION 2 POST LIFT Page 75 ...
Page 76: ...OPERATING INSTALLATION INSTRUCTION 2 POST LIFT Page 76 ...
Page 77: ...OPERATING INSTALLATION INSTRUCTION 2 POST LIFT Page 77 ...
Page 78: ...OPERATING INSTALLATION INSTRUCTION 2 POST LIFT Page 78 ...
Page 79: ...OPERATING INSTALLATION INSTRUCTION 2 POST LIFT Page 79 ...
Page 80: ...OPERATING INSTALLATION INSTRUCTION 2 POST LIFT Page 80 ...