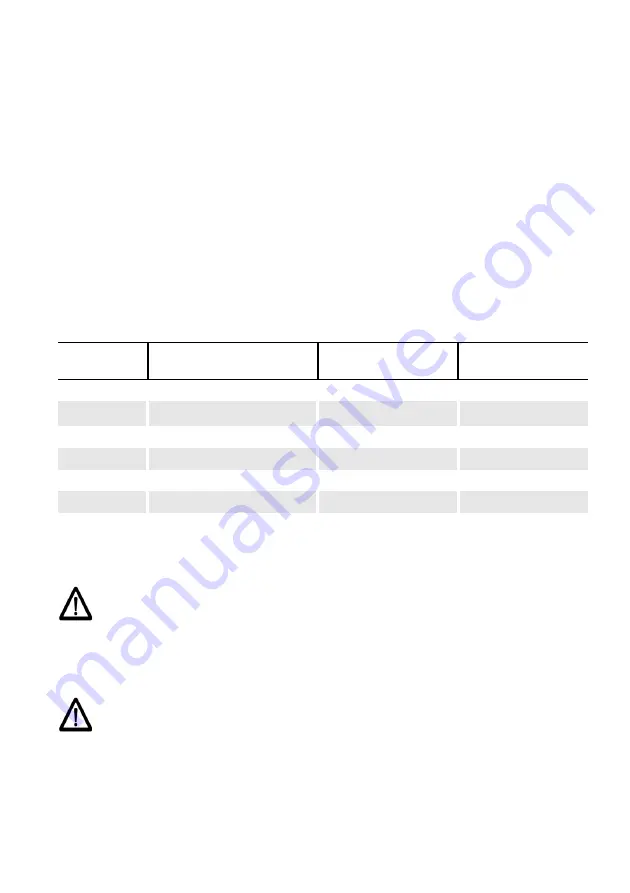
39
6.3
SETTING OF THE LIMIT VALUES
The cover must be removed before the limit values can be set.
(Pull the cover up.)
The limits:
/
max. flow
/
max. water volume
/
max. drawing time
can be set with three 6-way DIP switches S1, S2 and S3 (see fig. 6). Each contact of a DIP switch is assigned
a limit value.
The power supply unit must be pulled out before changing the setting of the DIP switches. Then the power
supply unit is plugged back in. After the automatic LED test, the new setting is displayed by the assigned
LED of the assigned LED series (see chapter 6.4 “DISPLAY OF THE SET LIMIT VALUES”).
To set the limit values, in each case only one contact of a DIP switch can be pushed to the left in the “ON”
position.
The limit value can be switched off, in that all contacts of a DIP switch (S1, S2 or S3) are pushed to the right
position. The last LED of the “Off” LED row illuminates.
The limit values must be set according to the respective consumption habits. If under the normal consump-
tion habits a limit value is regularly exceeded, without a leak being present, the assigned DIP switch can be
reset to a larger limit value.
DIP switches
S1
max. water flow [m³/h]
S2
max. water volume [m³]
S3
max. drawing time [h]
Contact 6 “ON”
5
3
2
Contact 5 “ON”
4
1)
1) The factory setting of the DIP switches is identified in the table by the values shown in bold.
2
1
Contact 4 “ON”
3
1
0.5
Contact 3 “ON”
2
0.5
0.3
Contact 2 “ON”
1
0.2
0.2
Contact 1 “ON”
0.5
0.1
0.1
If more than one contact of the DIP switches S1-S3 is pushed to the left, the corre-
sponding LED row signals that a setting error exists by simultaneous flashing of all
LEDs. Additionally the red “Fault” LED illuminates. The DIP switch setting must
then be corrected.
If one of the limit values is switched off, this value is no longer monitored. If for
example for DIP switch S3 (max. drawing time) all contacts are in the right posi-
tion, a small leak can only be detected by the control sensor, when the max. water
volume set using DIP switch S2 is reached.
Summary of Contents for CLEAR 2.0 SAFE
Page 12: ...12 6 BETRIEB Abb 5 CLEAR 2 0 SAFE mit abgenommener Abdeckhaube Abb 6 CLEAR 2 0 SAFE Schaltung...
Page 36: ...36 6 OPERATION Fig 5 CLEAR 2 0 SAFE with removed cover Fig 6 CLEAR 2 0 SAFE switch...
Page 60: ...60 6 EKSPLOATACJA Rys 5 CLEAR 2 0 SAFE ze zdj t os on Rys 6 CLEAR 2 0 SAFE uk ad elektryczny...
Page 74: ...74 Notizen Notes Notatki...
Page 75: ...75 Notizen Notes Notatki...