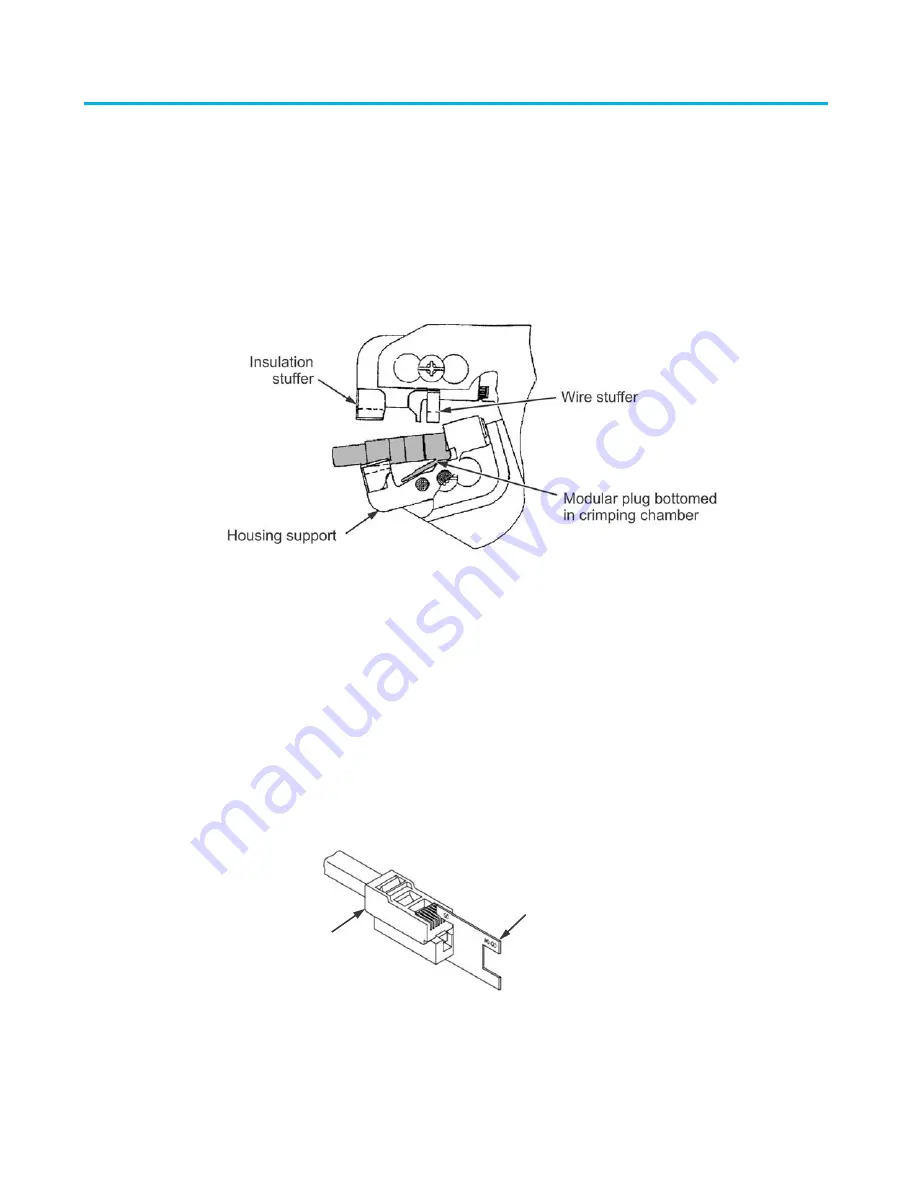
408-8738
Instruction Sheet
www.commscope.com
Page 4 of 6
5. Crimping Procedure
Before proceeding, refer to the applicable Application Specification: 114-22008 (Category 5E EMT) or
114-13035 and 114-93006 (Category 6 shielded), and ensure the following:
Modular plug and cable are compatible
Cable polarity is properly maintained
Modular plug is properly crimped and assembled
CAUTION:
Make sure that the modular plug shield is fully bottomed onto the body. With some cables
containing shielded twisted pairs, this is especially IMPORTANT to check.
Figure 3. Position of Modular Plug Before Crimping
1. Close the tool handles until the ratchet releases, then allow the handles to open FULLY.
2. Hold the tool so that the back is facing you. Insert the modular plug (including shield and cable) in the crimping
chamber until it bottoms. Refer to Figure 3.
3. While holding the assembly, carefully close the tool handles until the ratchet releases, then allow the handles
to open FULLY.
Note:
This tool terminates three areas of the modular plug. For proper alignment, make sure to apply forward
pressure on the cable while closing the tool handles.
4. Remove the modular plug from the tool, and make sure that the crimp requirements are met according to the
applicable application specification (refer to first paragraph of Section 5).
If necessary, adjust the tool ratchet according to Paragraph 6.1 to obtain the proper crimp height.
Figure 4. Crimp Height Gauge
Note:
Crimp Height Gauge 904170-1 can be used as a quick verification of acceptable crimp height as shown in
Figure 4. Refer to Instruction Sheet 408-4389 for instructions on using the gauge.
Crimp height
gauge (ref)
Modular plug
(ref)