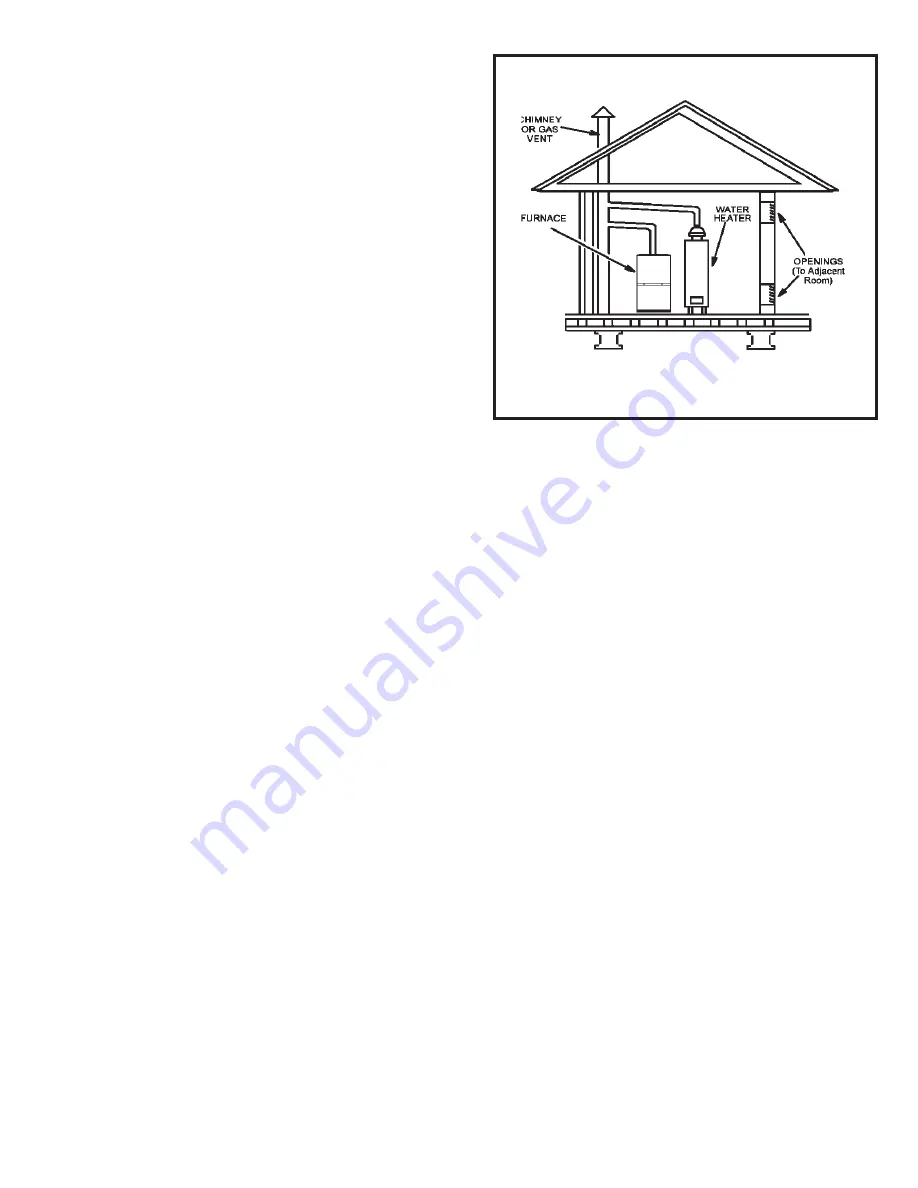
506842-01
Page 7 of 42
Issue 1132
All gas fired appliances require air for the combustion
process. If sufficient combustion air is not available, the
furnace or other appliances will operate inefficiently and
unsafely. Enough air must be provided to meet the needs
of all fuel burning appliances and appliances such as exhaust
fans which force air out of the house. When fireplaces,
exhaust fans, or clothes dryers are used at the same time
as the furnace, much more air is necessary to ensure proper
combustion and to prevent a downdraft. Insufficient air
causes incomplete combustion which can result in carbon
monoxide.
In addition to providing combustion air, fresh outdoor air
dilutes contaminants in the indoor air. These contaminants
may include bleaches, adhesives, detergents, solvents and
other contaminants which can corrode furnace components.
The requirements for providing air for combustion and
ventilation depend largely on whether the furnace is installed
in an unconfined or a confined space.
Unconfined Space
An unconfined space is an area such as a basement or
large equipment room with a volume greater than 50 cubic
feet (1.42 m
3
) per 1,000 Btu (.29 kW) per hour of the
combined input rating of all appliances installed in that space.
This space also includes adjacent rooms which are not
separated by a door. Though an area may appear to be
unconfined, it might be necessary to bring in outdoor air for
combustion if the structure does not provide enough air by
infiltration. If the furnace is located in a building of tight
construction with weather stripping and caulking around the
windows and doors, follow the procedures in the air from
outside section.
Confined Space
A confined space is an area with a volume less than 50
cubic feet (1.42 m
3
) per 1,000 Btu (.29 kW) per hour of the
combined input rating of all appliances installed in that space.
This definition includes furnace closets or small equipment
rooms.
When the furnace is installed so that supply ducts carry air
circulated by the furnace to areas outside the space
containing the furnace, the return air must be handled by
ducts which are sealed to the furnace casing and which
terminate outside the space containing the furnace. This is
especially important when the furnace is mounted on a
platform in a confined space such as a closet or small
equipment room. Even a small leak around the base of the
unit at the platform or at the return air duct connection can
cause a potentially dangerous negative pressure condition.
Air for combustion and ventilation can be brought into the
confined space either from inside the building or from outside.
Air from Inside
If the confined space that houses the furnace adjoins a
space categorized as unconfined, air can be brought in by
providing two permanent openings between the two spaces.
Each opening must have a minimum free area of 1 square
inch (645 mm
2
) per 1,000 Btu (.29 kW) per hour of total
input rating of all gas fired equipment in the confined space.
Each opening must be at least 100 square inches (64516
mm
2
). One opening shall be within 12 inches (305 mm) of
the top of the enclosure and one opening within 12 inches
(305 mm) of the bottom. See Figure 3.
Air from Outside
If air from outside is brought in for combustion and ventilation,
the confined space must have two permanent openings. One
opening shall be within 12 inches (305 mm) of the top of the
enclosure and one opening within 12 inches (305 mm) of
the bottom. These openings must communicate directly or
by ducts with the outdoors or spaces (crawl or attic) that
freely communicate with the outdoors or indirectly through
vertical ducts. Each opening shall have a minimum free
area of 1 square inch (645 mm
2
) per 4,000 Btu (1.17 kW)
per hour of total input rating of all equipment in the enclosure.
See Figures 4 and 5. When communicating with the
outdoors through horizontal ducts, each opening shall have
a minimum free area of 1 square inch (645 mm
2
) per 2,000
Btu (.56 kW) per total input rating of all equipment in the
enclosure. See Figure 6.
Figure 3
Equipment in Confined Space - All Air From Inside
NOTE:
Each opening shall have a free area of at least one square
inch per 1,000 Btu (645 mm² per .29 kW) per hour of the total input
rating of all equipment in the enclosure, but not less than 100 square
inches (64546 mm²).