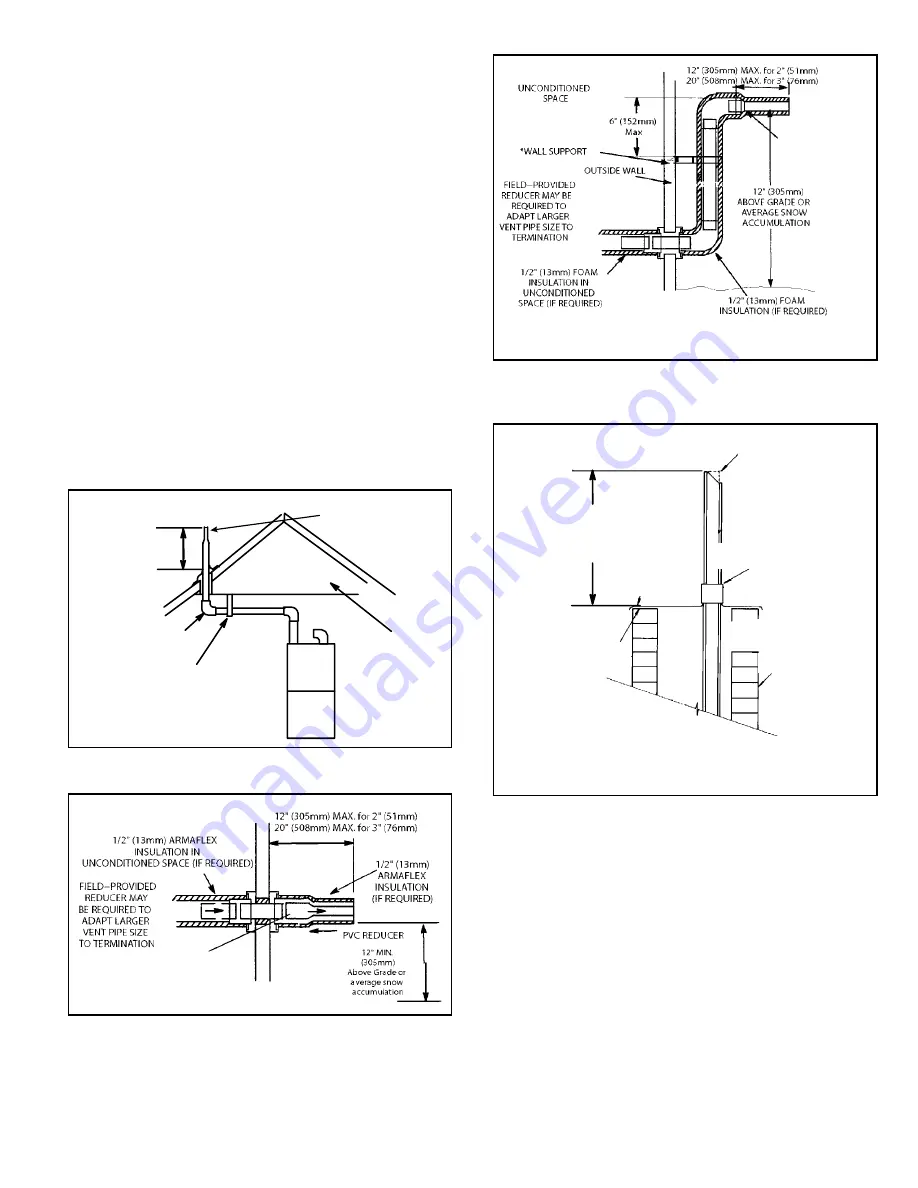
507714-01
Page 27 of 52
Issue 1716
Details of Exhaust Piping Terminations for Non-
Direct Vent Applications
Exhaust pipe may be routed either horizontally through
an outside wall or vertically through the roof. In attic or
closet installations, vertical termination through the roof
is preferred. Figure 40 through Figure 43 show typical
terminations.
1. Exhaust piping must terminate straight out or up as
shown. The termination pipe must be sized as listed
in Table 9. The specified pipe size ensures proper
velocity required to move the exhaust gases away
from the building.
2. On field supplied terminations for side wall exit,
exhaust piping may extend a maximum of 12 inches
(305 mm) for 2” PVC and 20” (508 mm) for 3” (76 mm)
PVC beyond the outside wall. See Figure 41.
3. If exhaust piping must be run up a sidewall to position
above snow accumulation or other obstructions, piping
must be supported every 24” (610 mm) as shown in
Figure 42. When exhaust piping must be run up an
outside wall, any reduction in exhaust pipe size must
be done after the final elbow.
Figure 40. Non-Direct Vent Roof Termination Kit
UNCONDITIONED
ATTIC SPACE
3” (76MM) OR
2” (51MM) PVC
PROVIDE SUPPORT
FOR EXHAUST LINES
12” (305MM)
ABOVE AVE.
SNOW
ACCUMULATION
SIZE PER EXHAUST PIPE
TERMINATION SIZE
REDUCTION TABLE
Figure 41. Non-Direct Vent Field Supplied Wall
Termination
SIZE TERMINATION
PER EXHAUST PIPE
TERMINATION SIZE
REDUCTION TABLE
Figure 42. Non-Direct Vent Field Supplied Wall
Termination Extended
SIZE TERMINATION
PER EXHAUST PIPE
TERMINATION SIZE
REDUCTION TABLE
* Use wall support every 24” (610 mm). Use two supports of extension is greater than 24”
(610 mm) but less than 48” (1219 mm).
Figure 43. Non-Direct Vent Application Using Existing
Chimney
STRAIGHT-CUT OR
ANGLE-CUT IN DIRECTION
OF ROOF SLOPE
SHOULDER OF FITTINGS
PROVIDE SUPPORT
OF PIPE ON TOP PLATE
EXTERIOR
PORTION OF
CHIMNEY
INSULATE
TO FORM
SEAL
SHEET
METAL TOP
PLATE
Minimum 12” (305MM)
above chimney top
plate or average snow
accumulation
* SIZE TERMINATION PIPE
PER EXHAUST PIPE TERMINATION
SIZE REDUCTION TABLE