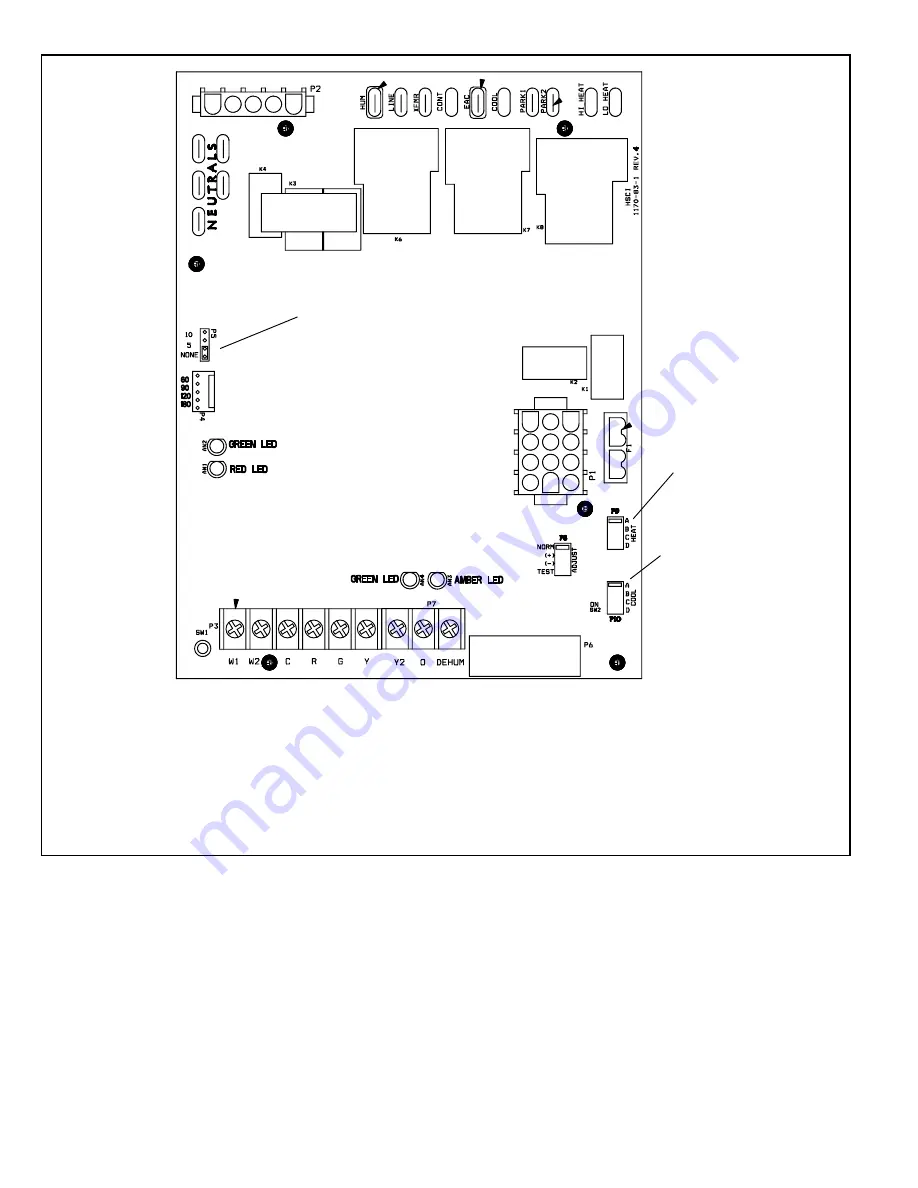
508183-01
Issue 2114
Page 8 of 52
Figure 3. Integrated Control
TERMINAL DESIGNATIONS
HUM -Humidifier (120VAC)
Line - Input (120VAC)
XFMR - Transformer (120VAC)
EAC - Indoor Air Accessory (120VAC)
Cool - Cool Speed (120VAC)
Park 1 - Dead terminal for alternate speed tap
Park 2
- Dead terminal for alternate speed tap
Heat Stage Jumper
(single stage shown)
Heat
Taps
Cool
Taps
Air Flow
Jumper