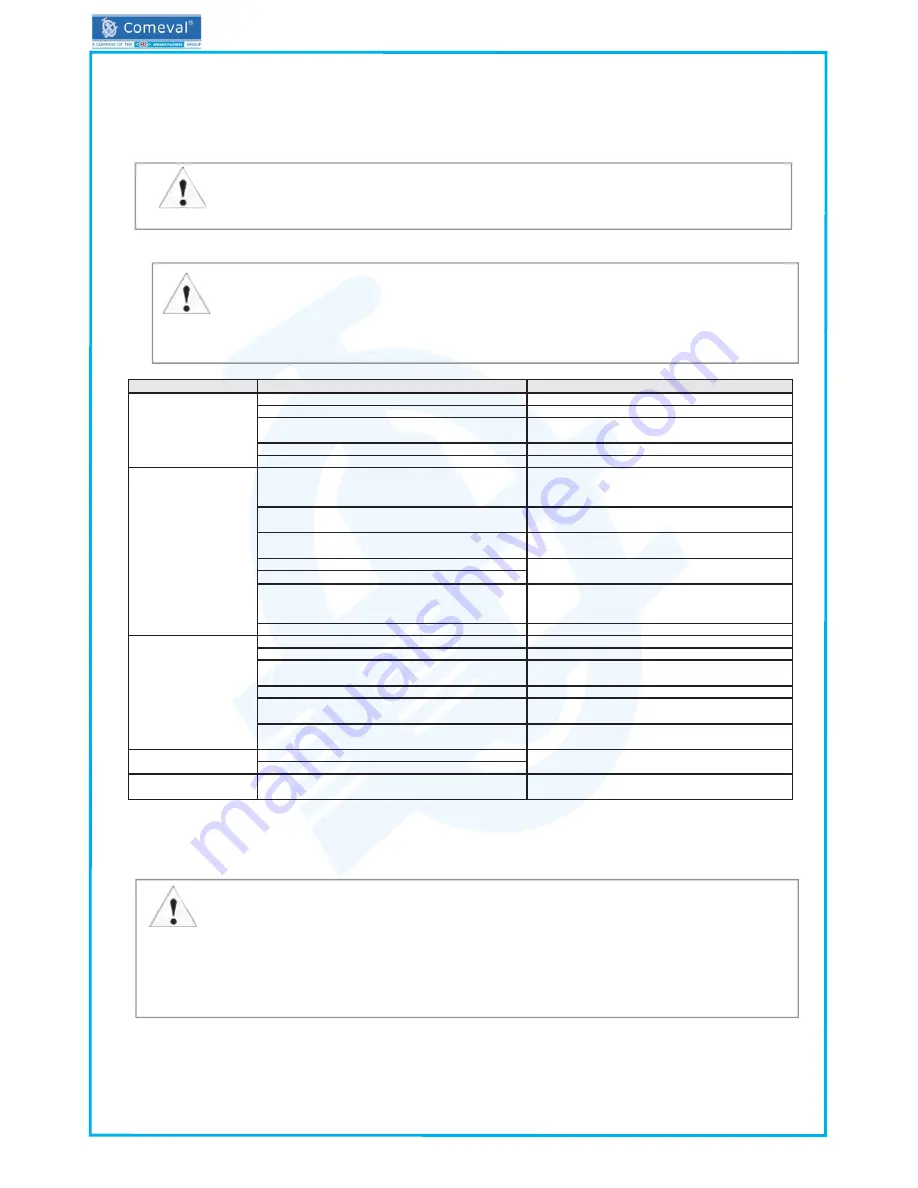
IOM -
SELF-ACTING DIAPHRAGM VALVES
MAXOMATIC VMXBERL24C
©COMEV
AL
V
A
L
VE SYSTEMS
T
echnical Dept. Ref. IOM-SELF-ACTING DIAPHRAGM V
A
L
VES, MAXOMA
TIC VMXBXERL24C-Ed.15/05
Comeval V
alve Systems reserves the right to alter any technical data contained in this Manual without prior notice. Regularly u
pdated data on www
.comeval.es
8. – TROUBLESHOOTING
In the event of malfunction or faulty operating performance, check that the installation and adjustment work has been
carried out and completed in accordance with this Manual.
9. – TROUBLESHOOTING TABLE
FAULT
POSSIBLE CAUSE
CORRECTING MEASURES
No fl ow
Not enough fl ow
-Flange covers or protection not removed.
-Clear valve entrances.
-Isolating valves of Pilot circuit or of pipeline closed.
-Open the valves.
-Normal pipeline pressure is not enough to overcome
diaphragm rigidity.
-Check pipeline pressure in relation to selected dia-
phragm and the condition of the diaphragm itself.
-Piping clogged.
-Check piping system.
-Solenoids calcifi ed or with impurities.
-Check the Solenoid clean or replace if needed.
Valve is not closing or is
not tight at closing
-The Pilot is not operating correctly or is not well ad-
justed. The Pilot does not stop the drainage of the
activation chamber (observe the exhaust of the Pilot).
-Check the closing with the manual valve or with the
Solenoid valve if any.
-Check adjustment and condition of the Pilot. Chan-
ge if needed.
-Dirt/deposits trapped between the diaphragm and
body seat.
-Open and close again trying to eliminate dirt trap-
ped.
-Diaphragm damaged.
-Disassemble and inspect the body and diaphragm,
clean or replace parts.
-Body seat wear.
-Strainer or Pilot circuit clogged.
-Check if the fl uid reaches the activation chamber,
by unplugging the corresponding connection. Revise
fi ltering and Pilot circuit.
-Solenoids calcifi ed or with impurities.
-Check the Solenoid core, clean or replace if needed.
Valve is not regulating
properly
-Pilot is not well adjusted.
-Check tightening of Pilot adjusting screw.
-Valve is oversized.
-Check valve sizing.
-The adjusting point is out of the Pilot adjusting range
or out of the diaphragm working range.
-Check operation conditions in relation to Pilot and
diaphragm.
-Strainer or Pilot circuit clogged.
-Check fi ltering and Pilot circuit.
-Pilot working failure.
-Tighten/loosen the Pilot adjusting screw to observe
if there is any reaction. Inspect/replace it if needed.
-Opening/closing speed not suitable (large size val-
ves with accelarator Pilot).
-Check adjustment of adjusting screw of accelerator
Pilot.
Broken fl ange
-Bolts not properly tightened.
-Realign piping and fi t new valve.
-Mating fl anges not properly aligned.
Leakage between body
and cover
-Cover bolts loose or diaphragm damaged.
-Retighten bonnet bolts or change diaphragm.
Technical support always available through our website www.comeval.es or your local distributor.
10. – DISMANTLING THE VALVE OR THE COVER
Page 7
ATTENTION!
- Read chapters 10 & 11 before carrying out installation and repair work!
- Read chapter 6 before recommissioning!
ATTENTION!
The following points must be observed:
- Pressureless pipe system
- Medium must be cool
- Plant must be drained
- Purge pipe systems in case of toxic, corrosive, fl ammable or caustic media
ATTENTION!
- It is essential that the safety regulations are observed when identifying faults.