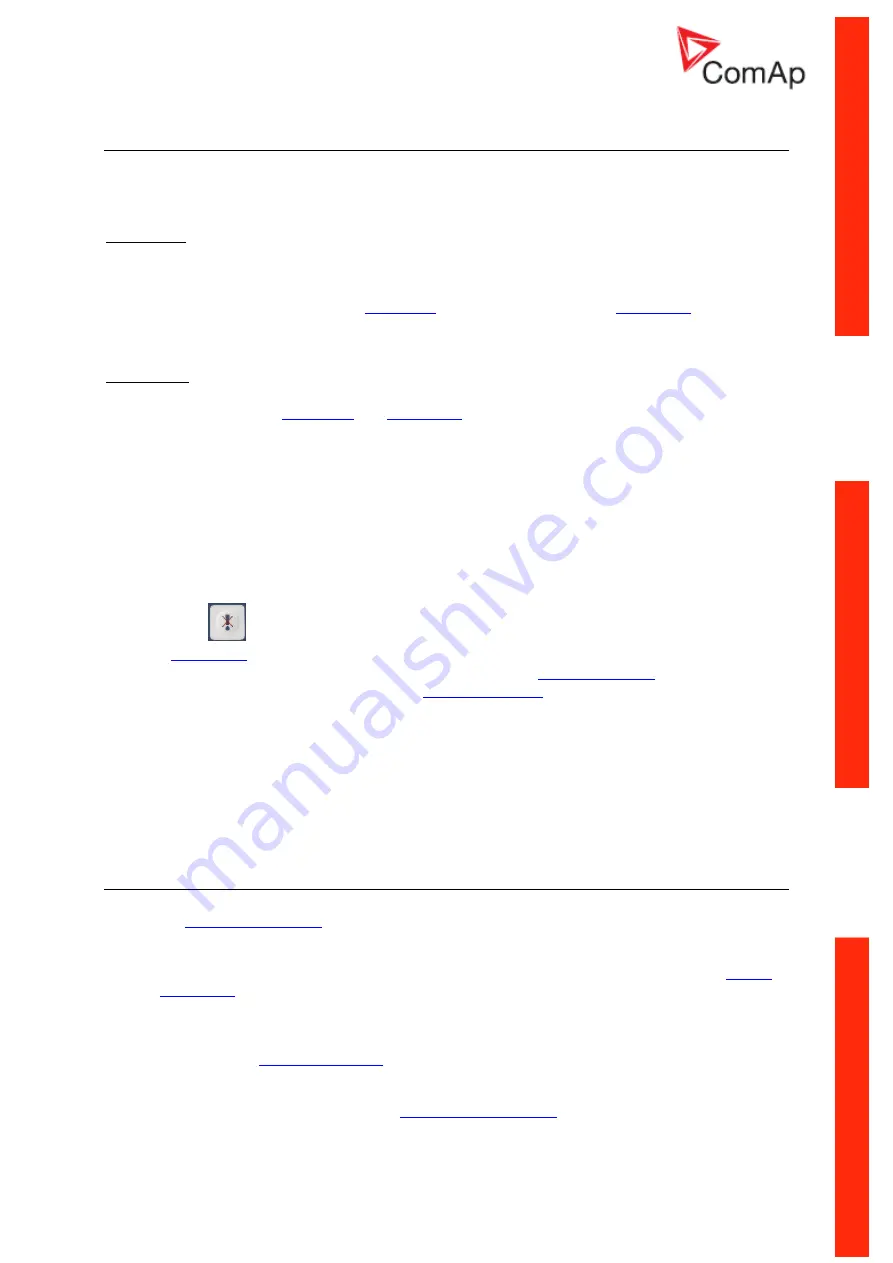
InteliPro, SW version 1.4,
©
ComAp
–
April 2014
InteliPro 1.4 Comprehensive Guide - rev. 1
2-5
TRIP and Fault Reset description
TRIP
TRIP may be considered as event or status of the unit:
TRIP event:
Starts in the moment of terminating the count-down of any protective function with delay, or in the
moment of activation of any immediate protective function.
As a result of the trip event, are e.g. the following consequences:
o
Immediate activation of output
and deactivation of output
o
LED TRIP goes to red
o
History record is created
TRIP status:
Starts at the moment of TRIP event
outputs keep in the fault position
During this status, it is not possible to perform Fault reset
TRIP status is active until a successful Fault reset. This may not be done before all measured and
evaluated values are within preset limits.
If during the TRIP status, caused by some value, another value overreached its limits for TRIP
evaluation, this second overreach is not considered as TRIP. It does not cause a second TRIP
event. However, as a consequence of this, the TRIP duration may be prolonged until the moment
when both (all) values are within limits.
Fault reset
Fault reset is an event, caused by either of the following reasons:
Fault reset
button is pressed
Automatic fault reset is performed according to the setting of
By activation or deactivation of binary input
The abovementioned reasons are a trigger to provide Fault reset, however, it is successfully done only
in case that the TRIP status is activated and all evaluated values have returned back into limits. If the
TRIP status is not activated, or it is activated, but any of the values is still out of limits, Fault reset is
not done and any of the mentioned triggers is forgotten. I.e., the unit may not be „provisionally“ fault
-
reset.
By a successful Fault reset, the TRIP status is terminated.
Interconnection to IG/IS-NT controllers
It is possible to interconnect InteliPro unit with IG-NT and IS-NT controllers on the CAN2 bus. Refer to
the chapter
for the details on wiring the CAN2 bus. The most frequent
applications of this function are as follows:
-
Transmitting analog values like active and reactive power, measured voltage or current from
the point of connection to the mains via IntleiPro to the NT controllers. Technology of
is used to transmit up to 4 analog values. The transmitted values can then be
processed by the controllers to allow the requested operation of the gen-sets (e.g. load and
PF control).
-
Transmitting binary signal from the point of connection to the grid to the controllers.
Technology of
is used to transmit up to 8 binary signals. Typically, the
state of breaker feedbacks or other InteliPro binary inputs can be used to provide inputs to the
gen-set control processes. Another application is to use InteliPro as a communication
interface that allows e.g. setting the
state of the switches can then be transferred to the controllers to reduce power to the value
requested by the external system or provide other signals relevant to the site operation.