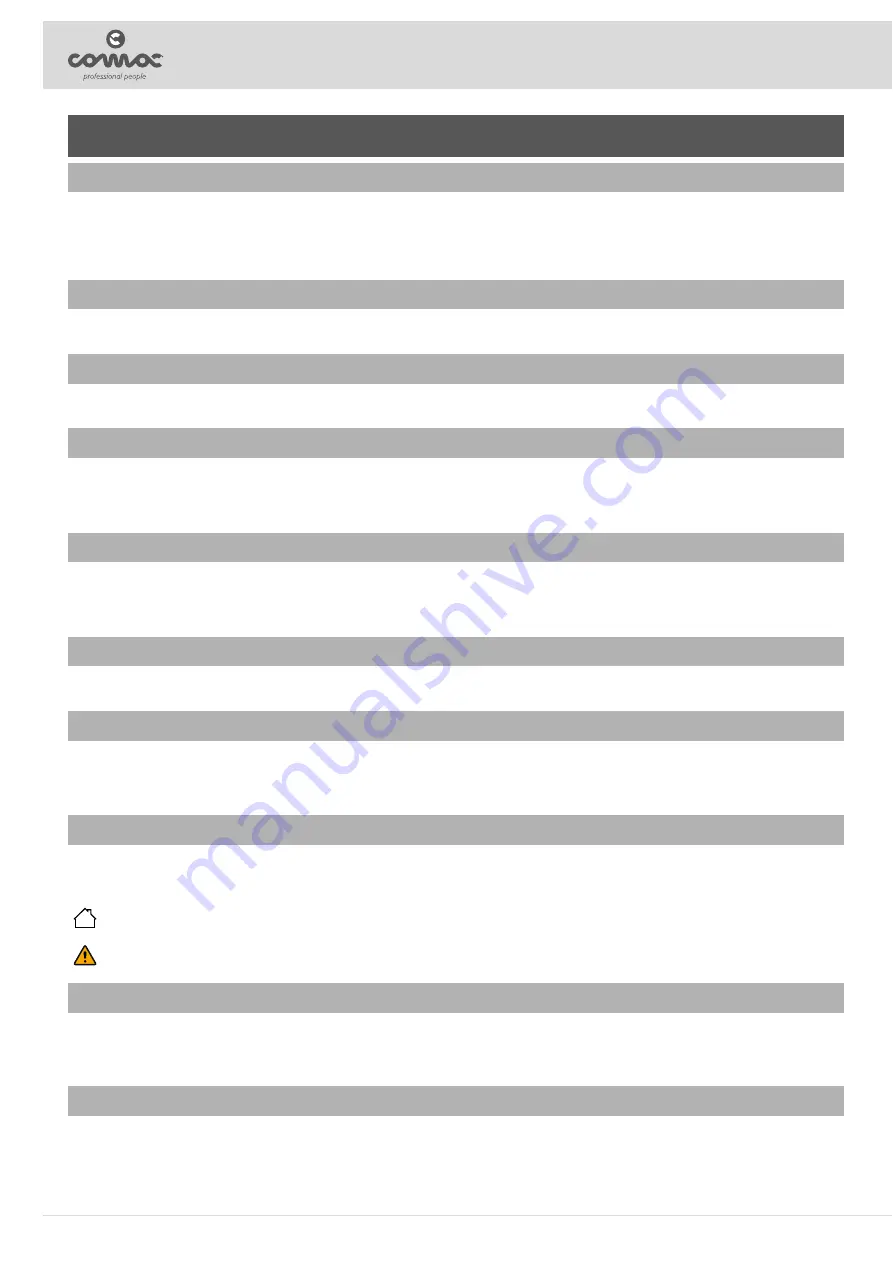
GENERAL DESCRIPTION
PURPOSE AND CONTENT OF THE MANUAL
The aim of this manual is to provide customers with all the information needed to use the machine in the safest, most appropriate and most
autonomous way. This includes information concerning technical aspects, safety, operation, downtime, maintenance, spare parts and scrapping.
The operators and qualified technicians must carefully read the instructions in this manual before carrying out any operations on the machine. If in
doubt about the correct interpretation of instructions, contact your nearest Customer Service Centre to obtain the necessary clarifications.
TARGET GROUP
This manual is written both for operators and for qualified machine maintenance technicians. Operators must not perform operations that should
be carried out by qualified technicians. The manufacturer is not liable for damages resulting from failure to comply with this veto.
STORING THE USE AND MAINTENANCE MANUAL
The Use and Maintenance Manual must be stored in its special pouch close to the machine, protected from liquids and anything else that could
compromise its legibility.
ON CONSIGNMENT OF THE MACHINE
When the machine is consigned to the customer, an immediate check must be performed to ensure all the material mentioned in the shipping
documents has been received, and also to check the machine has not suffered damage during transportation. If this is the case, the carrier must
ascertain the extent of the damage at once, informing our customer service office. It is only by prompt action of this type that the missing material
can be obtained, and compensation for damage successfully claimed.
INTRODUCTORY COMMENT
Any floor scrubbing machine can only work properly and effectively if used correctly and kept in full working order by performing the maintenance
operations described in the attached documentation. We therefore suggest you read this instruction booklet carefully and read it again whenever
difficulties arise while using the machine. If necessary, remember that our assistance service (organised in collaboration with our dealers) is
always available for advice or direct intervention.
IDENTIFICATION DATA
For technical assistance or to request replacement parts, always give the model, the version and the serial number (written on the relevant plate).
TECHNICAL DESCRIPTION
The
Innova Comfort
is a floor scrubbing machine that can handle a wide variety of floors and types of dirt thanks to the mechanical action of
two disc brushes and the chemical action of a water-detergent solution. As it advances, it collects the dirt removed and the detergent solution not
absorbed by the floor.
The machine must only be used for this purpose
.
INTENDED USE
This scrubbing machine was designed and built for the cleaning (scrubbing and drying) of smooth, compact flooring in the commercial, residential
and industrial sectors by a qualified operator in proven safety conditions. The scrubbing machine is not suitable for cleaning rugs or carpet floors.
It is only suitable for use in closed (or at least covered) places.
ATTENTION:
the machine is not suitable for use in the rain, or under water jets.
IT IS FORBIDDEN:
to use the machine to clean up dangerous powders or flammable liquids in environments with an explosive atmosphere.
In addition, it is not suitable as a means of transport for people or objects.
SAFETY
Operator cooperation is paramount for accident prevention. No accident prevention programme can be effective without the full cooperation of the
person directly responsible for machine operation. The majority of occupational accidents that happen either in the workplace or whilst moving
are caused by failure to respect the most basic safety rules. An attentive, careful operator is most effective guarantee against accidents and is
fundamental in order to implement any prevention programme.
REGULATIONS
All references to forwards and backwards, front and rear, right and left indicated in this manual should be understood as referring to the operator
in a driving position with his hands on the steering wheel.
8
Summary of Contents for 109160
Page 1: ...SCRUBBING MACHINES ORIGINAL INSTRUCTION DOC 10084230 Ver AA 05 2020 USE AND MAINTENANCE MANUAL...
Page 2: ......
Page 42: ...42...
Page 43: ......