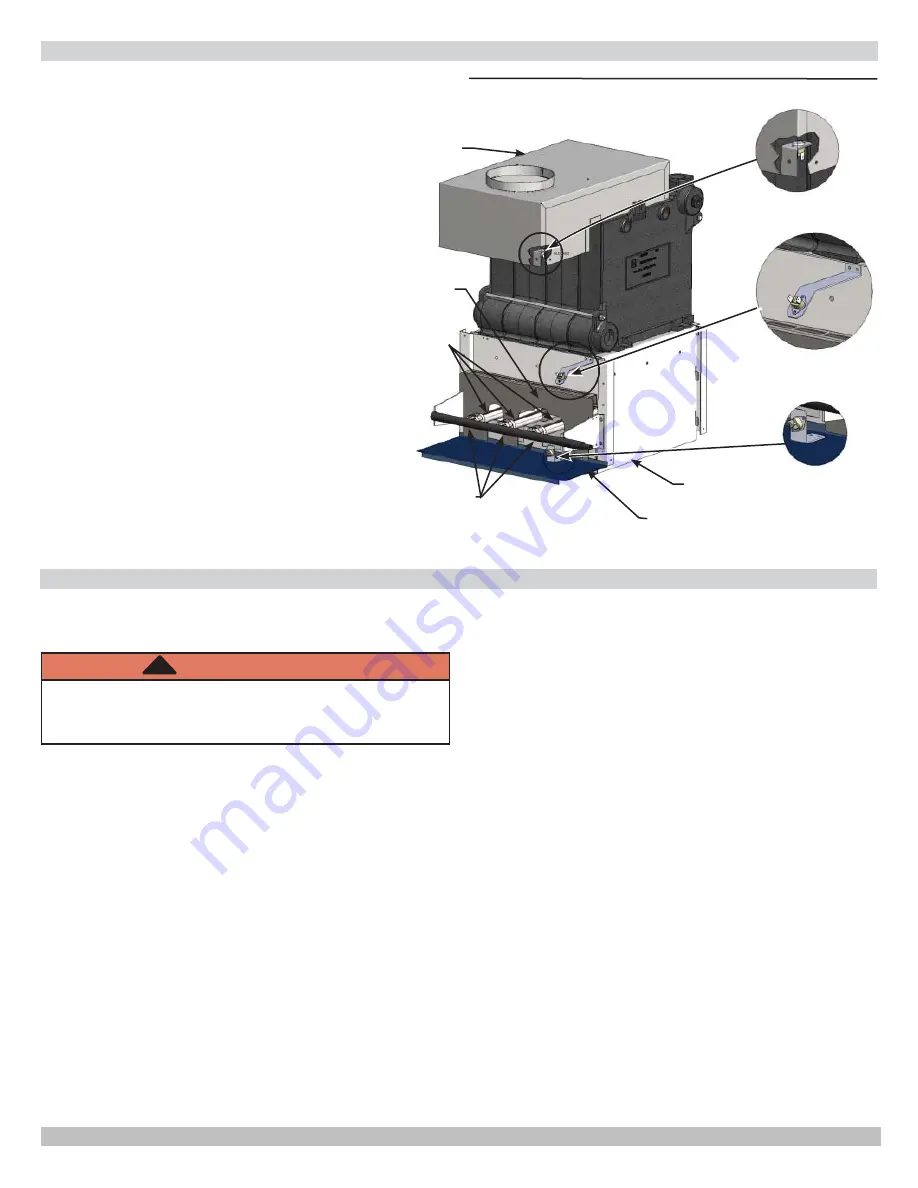
18
12 - NORMAL SEQUENCE OF OPERATION
13 - GENERAL INSTRUCTIONS
Thermostat actuates on call for heat,
completing circuit to control. Completed
circuit to control will
fi
rst activate circulator
and damper which will close end switch inside
damper. Completes circuit to ignition system,
ignition takes place.
In event boiler water temperature exceeds
high limit setting on boiler mounted high limit
control, power is interrupted between control
system and ignition system. Power remains
off until boiler water temperature drops below
high limit setting. Circulator continues to
operate under this condition until thermostat is
satis
fi
ed.
In event
fl
ow of combustion products through
boiler venting system becomes blocked, blocked
vent safety switch shuts main burner gas off.
Similarly, if boiler
fl
ue-way becomes blocked,
fl
ame rollout safety switch shuts main burner
gas off. Figure 16.
If either of these conditions
occur,
DO NOT ATTEMPT TO PLACE BOILER
BACK INTO OPERATION. CONTACT
CERTIFIED SERVICE AGENCY.
Blocked Vent
Safety Switch
Rollout Switch
4 Section Boiler
Rollout Switch
2,3,5
Section Boiler
Intergral Draft
Hood
Base
Burner
Door
Burners
Ori
fi
ces
Jacket Base
Panel
Before seasonal start-up, have a certi
fi
ed service agency
check boiler for soot and scale in
fl
ues, clean burners and
check gas input rate to maintain high operating ef
fi
ciency.
WARNING
Label all wires prior to disconnection when servicing
controls. Wiring errors could cause improper and
dangerous operation.
!
Verify proper operation after servicing
Service agency will verify system is
fi
lled with water to
minimum pressure and open air vents, if used, to expel any
air accumulated in the system. Check entire piping system
and, if any leaks appear, have them repaired.
Circulators need to be checked and maintained.
Refer to circulator manufacturer's instructions.
Inspect venting system at the start of each heating
season. Check vent pipe from boiler to chimney for signs of
deterioration by rust or sagging joints. Repair if necessary.
Remove vent pipe at base of chimney or
fl
ue and using a
mirror, check vent for obstruction and verify vent is in good
working order.
Boiler
fl
ue gas passageways may be inspected by a light
and mirror. Remove burner door. Figure 17. Place trouble
lamp in
fl
ue collector through draft relief opening. With
mirror positioned above burners,
fl
ue gas passageways can
be checked for soot or scale.
This procedure should be followed to clean
fl
ue gas
passageways:
1.
Remove burners from combustion chamber by raising
burners up from manifold ori
fi
ces and pulling toward
front of boiler. Figure 19.
2.
Disconnect vent pipe from draft hood.
3.
Remove top jacket panel.
4.
Remove combination
fl
ue collector and draft hood from
boiler castings by loosening nuts on hold down bolts
located on each side of collector. Figure 17.
5.
Place sheet of heavy paper or similar material over
bottom of base and brush down
fl
ue passageways. Soot
and scale will collect on paper and is easily removed
with the paper.
6.
With paper still in place in base, clean top of boiler
castings of boiler putty or silicone used to seal between
castings and
fl
ue collector. Verify chips are not lodged
in
fl
ue passageways.
When cleaning process is complete, restore boiler
components to their original position. Use IS-808 GE
silicone (available from distributor) to seal around
fl
ue
collector and boiler castings.
Figure 17 - Blocked Vent Safety Switch, Roll-out
Safety Switch