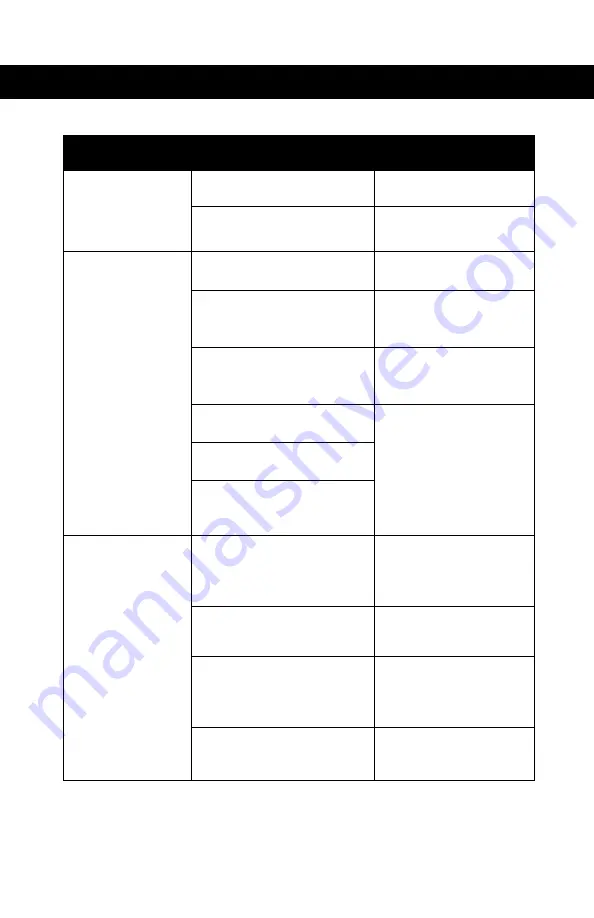
21
IF THE SOLUTIONS LISTED HERE DO NOT SOLVE YOUR PROBLEM
CONTACT OUR CUSTOMER SUPPORT HOTLINE:
+1-800-777-9101 (+1-513-576-8981)
TROUBLESHOOTING
PROBLEM
CHECK THIS
SOLUTION
MACHINE WILL
NOT POWER UP
GREEN LIGHT IS
NOT ON
Is the unit plugged in?
NO: Plug Unit in.
Is the power switch in the
ON (I) position?
NO: Push power switch
to ON (I).
MACHINE WILL
NOT BLAST
Is the BLUE DISABLE BLAST
LIGHT on?
YES: Pull the disable
blast button out.
Is the applicator safety
switch in the center
position?
YES: Flip the switch right
to deactivate safety.
The Air Filter may be
clogged.
Remove the back cover
and replace the filter
element.
Is the air supply connected
and the air supply on?
YES: The nozzle may be
clogged.
To unclog the nozzle,
blast with air only.
Is the blast pressure gauge
showing pressure?
Is the applicator cable
connected to the machine
and the applicator?
MACHINE BLASTS
AIR BUT NOT
SHAVED DRY ICE
Is the dry ice block behind
the Pusher Plate?
YES: Push the plate to
the back of the trough
and reinsert the dry ice
block.
Do the rotary knives look
damaged?
YES: Call Cold Jet for
support.
Is too much ice clogging the
feeder?
YES: Open the Chute
Access Port and blast
with compressed air to
break the clog.
Is a foreign object lodged in
the feeder.
YES: Call Cold Jet for
support.
Summary of Contents for i3 MICROCLEAN
Page 2: ...2...
Page 4: ...4...
Page 5: ...5 SAFETY...
Page 8: ...8...
Page 9: ...9 COMPONENT GUIDE...
Page 13: ...13 STANDARD CART...
Page 14: ...14...
Page 15: ...15 OPERATION...
Page 18: ...18...
Page 19: ...19 MAINTENANCE...
Page 22: ...22...
Page 23: ...23 APPENDIX...
Page 28: ...28...
Page 30: ...30...
Page 31: ...TRAINING VIDEO...