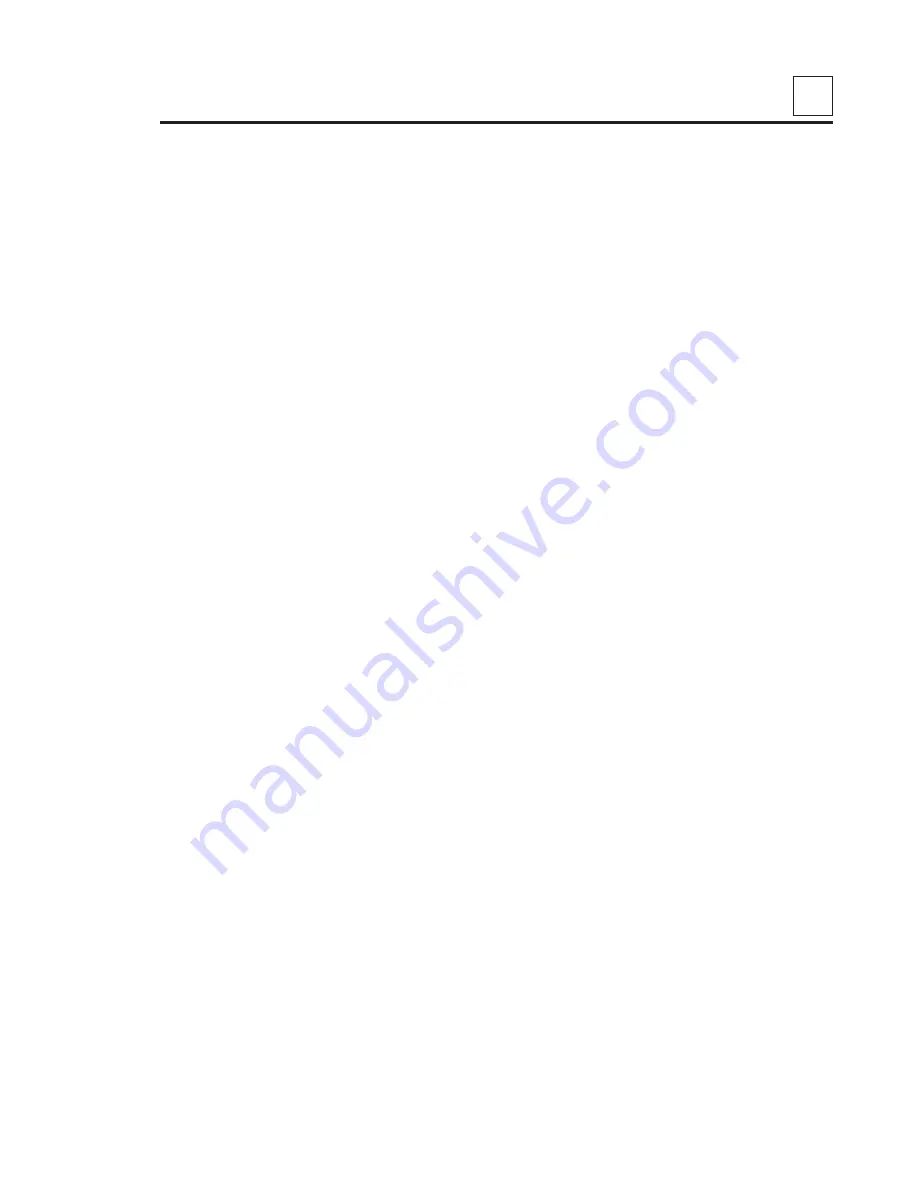
487 0329 21
11.7
11. Periodic maintenance
11
Service
manual
The area surrounding the dryer
Fresh-air intake to the room
Check that the fresh-air intake to the room and the exhaust ducts/pipes from the room
are not clogged by lint/dust or blocked in any other way.
Dryer area
Check that the dryer area is clear and free from combustible materials, gasoline and
other flammable vapours and liquids.
Safety and warnings signs (USA only)
Product safety signs or labels should be replaced when they no longer meet the
legibility requirements for safe viewing.
Check that all the safety and warning signs are located on the dryer as shown in the
installation manual supplied with the dryer. A copy of this manual is available from
your dealer.
Replacement of safety signs or labels should be in accordance with the installation
manual.
Summary of Contents for T3300S
Page 2: ......
Page 4: ......
Page 6: ......
Page 10: ...2 Technical data 2 Service manual 487 0329 21 2 4 ...
Page 20: ...11 Periodic maintenance 11 Service manual 487 0329 21 11 8 ...
Page 40: ...12 Error codes 12 Service manual 487 0329 21 12 20 Intentionally blank ...
Page 50: ...12 Error codes 12 Service manual 487 0329 21 12 30 ...
Page 66: ...29 Door and lint drawer 29 Service manual 487 0329 21 29 4 ...
Page 80: ...40 Heating 40 Service manual 487 0329 21 40 4 I III II 6 7 Dismounting of the heating unit ...
Page 99: ...487 0329 21 47 7 47 Gas system 47 Service manual ...