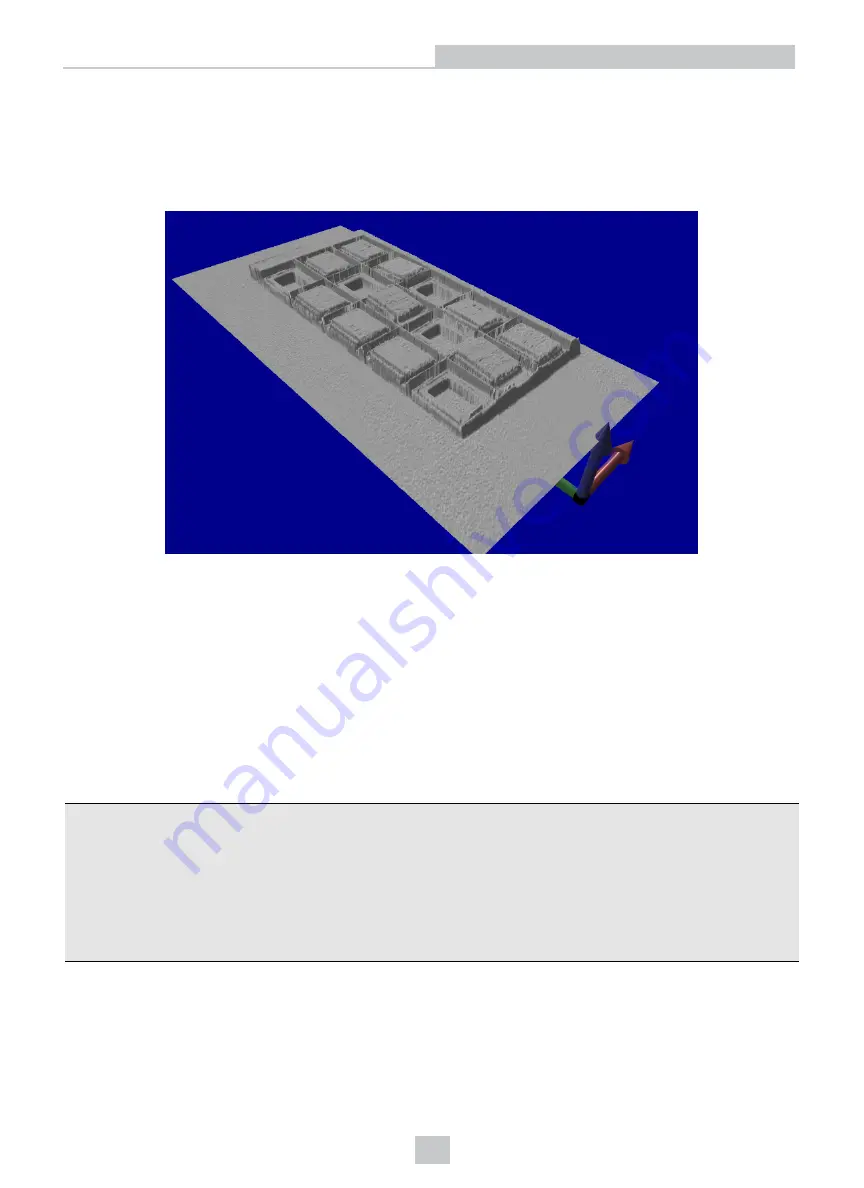
Image Acquisition
Your Cognex vision software captures image information and generates a synthetic image containing height profile
information of each object that passes within view of the laser and camera contained within the DS1000 series sensor,
as shown in the following example using a 3D display utility:
Image acquisition combines the use of the following:
l
Encoders - electrical devices that convert movement of the conveyor system into electrical pulses
l
Acquisition triggers - hardware devices that signal the start of an image acquisition
l
Acquisition parameters - settings in your Cognex vision software that determine the size and resolution of each
acquired image
Encoders
The DS1000 series sensor typically relies on electrical signals from an encoder to generate images, allowing the sensor
to capture image information based on the speed of the moving object rather than predetermined exposure settings.
Many vision applications use a rotary encoder attached to the conveyor system.
Note
:
l
The frequency of encoder pulses must not exceed 50 kHz.
l
Using an encoder allows you to specify input and output delay values in pulse counts instead of real time
units.
l
The sensor supports a test encoder that generates encoder pulses internally. The test encoder can be used
to acquire images without connecting a physical encoder, which can be useful as you develop your
application or if you need to verify the operation of the sensor while debugging encoder connection issues.
A rotary encoder typically uses two output channels (A and B) to provide cyclical outputs as the encoder rotates. The
signals are
quadrature
outputs - 90 degrees out of phase with each other. Each complete quadrature cycle consists of
four rising or falling
pulse
edges. The number of cycles per encoder rotation depends on the specific encoder you use.
29
Image Acquisition