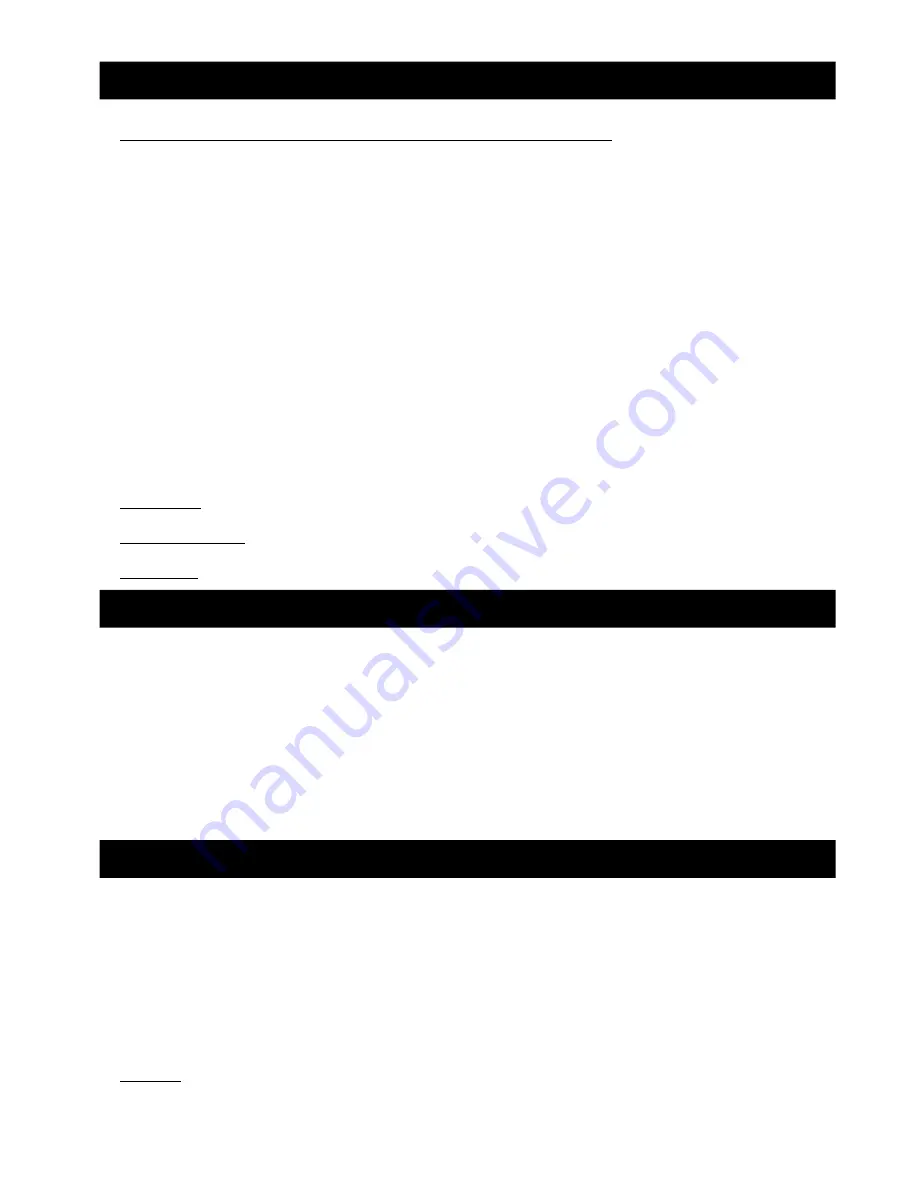
6.
5.3 Operation for espresso machine model Crema Compact och Digital
Water system diagram
The water used for production of coffee does not come from the boiler. It is supplied directly from the water
net, through the heat exchangers inside the boiler. The hot water and steam surrounding the heat
exchangers, give the water inside the right temperature. This is shown in the water system diagram
Wiring diagram
The machine is connected to the power supply network by means of the electric cord supplied. See p. 35.
The main switch
The machine is fitted with a two-position power switch:
- Position 0: no power supply to the internal components.
- Position 1: power supply to the operational electric components and to the heating element.
5.
Technical description Crema Compact och Digital
Do not tamper with the machine´s components or pull on the electric power cord to unplug it.
Never
clean the inside of the machine with the power ON or with the plug connected and do not use
detergents or jets of water in any case.
The operator must not touch the machine with damp or wet hands or feet, or use it with bare feet.
Allthough the machine is earthed, we recommend the use of a wooden foot-board and a centralized life-
saving system to prevent the risk of electric schocks as much as possible.
Grinder shall only be used for coffee beans.
All other usage could be dangerous and must seems like a
wrong and defective way to handle the machine.
The manufacturer is not responsible for damage which is caused by improper, unreasonable and/or incorrect
usage of machine.
Warning: Do not try to put in spoons, knife´s or other kitchen / housekeeping tools in the grinder
when machine is operating or in use.
6.
Safety precautions
5.
Technical description Crema Compact och Digital
5.2 Operating Principles
An espresso coffee machine is basically made up of the following elements:
Boiler
Is used to contain the hot water and steam.. Made of copper to get a equal temperature over the year.
Brewing group and heat exchanger
The brewing group is the component which, when attached to the filterholder, brews and delivers the
beverages when supplied with hot water. (Containing the filter and the ground coffee or coffee pod).
The heat exchangers, one for each group, are immersed in the water and are used for fast heating of the
fresh water from the network to the optimal temperature and to prevent thermal imbalances within the sys-
tem.
Heat source
This is normally provided by an electric heating element immersed in the boiler and/or by an external gas
burner , which heat the water and provide the steam.
Electric pump
This device is used to raise the pressure of the network, which is normally inadequate for the purpose, to a
pressure of 9 bars which is ideal for making the best coffee.
Steam taps
This allow steam to be delivered to give the indispensable ”froth” to the milk used for preparing cappuccino,
for heating water and punches and for preparing chocolate drinks.
Water tap
It allows water to be delivered for preparing hot drinks, tea and tisanes.
Control instruments
Manometers:
show the current pressure in the boiler and in Dig. models the pump´s operating
pressure.
Pressure switchest:
control the pressure and switching ON/OFF the heat sources to keep the boiler water
temperature constant.
Level gauge:
shows the water level in the boiler.