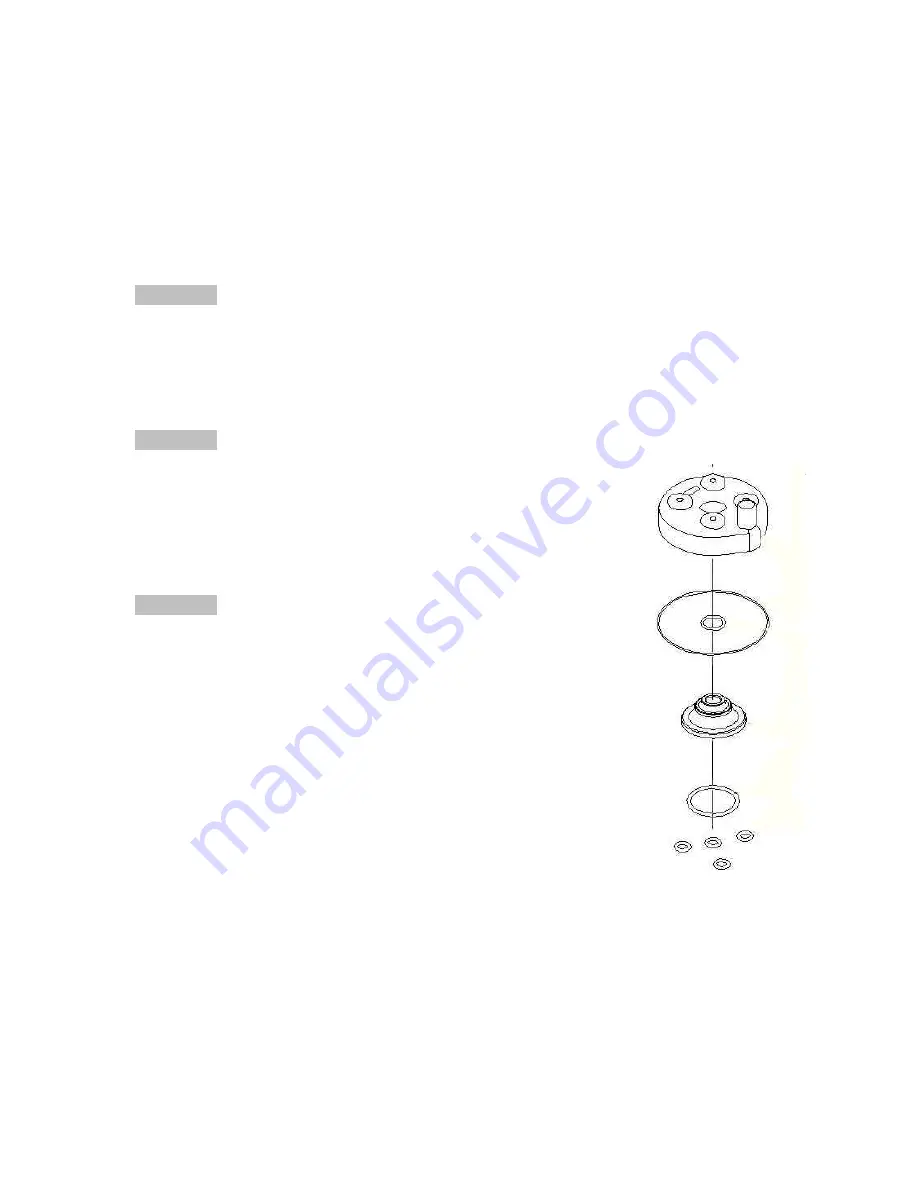
45
9. Torque to 12 Nm (105 in-lb) in the pattern shown in figure 28.
10. Trim away any excess gasket material if necessary.
NOTE:
Check engine mount holes for excess material that may cause problems
in engine installation.
11. Install the piston with new wrist pin bearing and, pin and clips.
CAUTION:
Be sure to align the piston such that the arrow on the top piston surface points to
the exhaust (front of bike/engine) and put assembly lube on the connecting rod
bearing.
12. Install the piston rings.
CAUTION:
Ring end gap should be no less than 0.25 mm (0.010”) and no
more than 0.64mm (0.025”)
13. Install the base gasket.
14. Install the cylinder being sure that the piston rings are
properly aligned with the indexing pins.
CAUTION:
Never force the cylinder. If resistance is felt, determine the
problem and solve it. Once installed slightly rotate the cylinder
back and forth insuring that the rings are properly seated.
15. Install cylinder head insert.
NOTE:
A light application of silicone grease can help hold the
O-RINGs into position during assembly.
16. Pressure test the engine insuring an acceptable leakdown
rate.
17. Install O-RINGs as shown in figure 29.
Figure 29
18. Install the cylinder head.
19. Install the washers (with flat side down) and nuts. Torque to 105 in-lb (12
Nm)
20. Install reed and inlet manifold with new gaskets (105 in-lb, 12 Nm) applying
1104 gasket sealer to both sides of all gaskets.
21. Leak check the engine to 20 psi to ensure proper seal.
22. Install stator reinstalling the grommet and wires (snug the bolts).
23. Install the rotor per
Rotor Installation
section, under the
S3: Ignition
portion of
this manual.