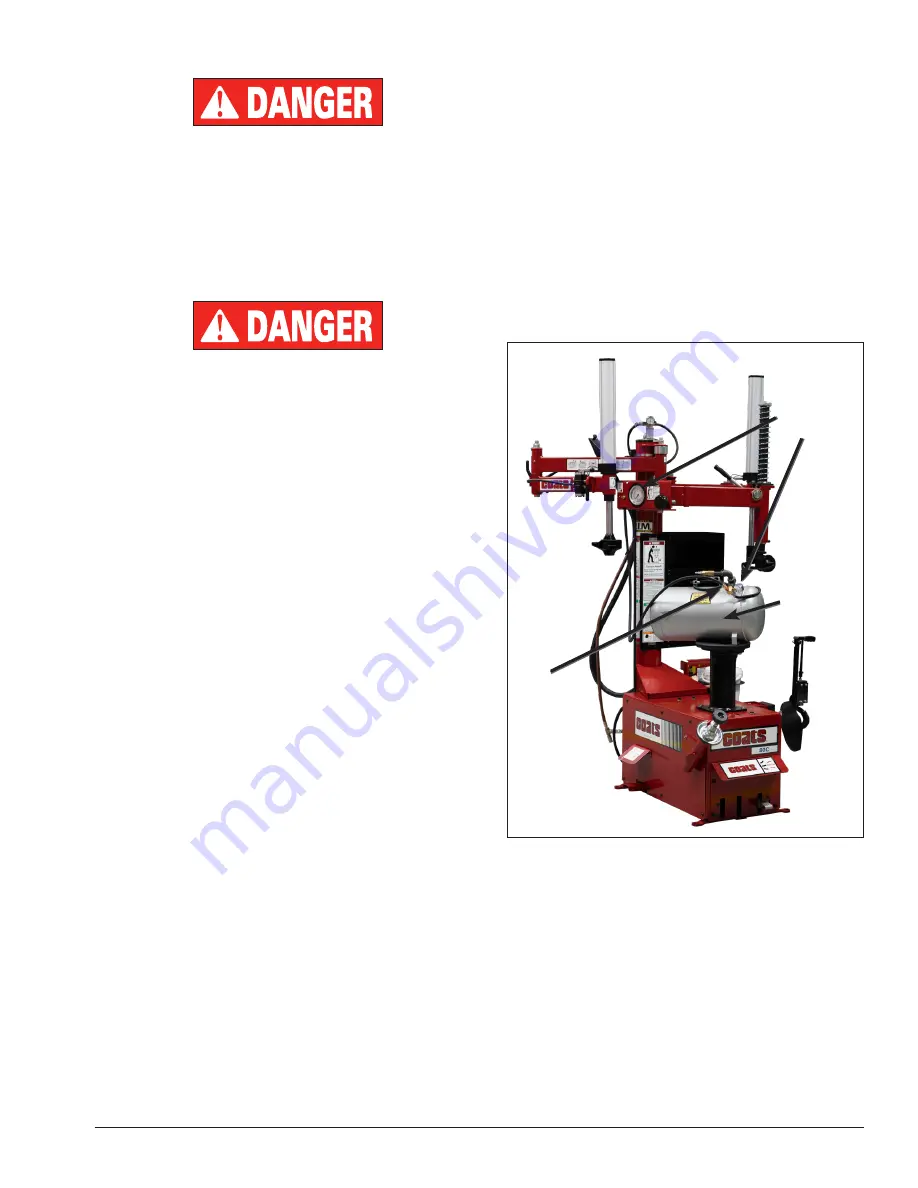
Important: Always read and follow operating instructions.
• 19
Pressure Limiter Maintenance
Operating a tire changer with a defective,
improperly adjusted, or by-passed pres-
sure limiter could cause an operator to
accidentally over pressurize a tire, result-
ing in a tire explosion with severe injury or
death to the operator or bystanders.
Always be sure that the pressure limiter is
present and is operating properly.
Never inflate tire above manufacturer’s rec-
ommended pressure after bead is seated.
Pressure limiter is set at 60 PSI. Any
required inflation above 60 PSI should be
performed in an inflation chamber/safety
cage or securely mounted on the vehicle
if an inflation chamber is not available. A
tire explosion may cause personal injury or
death to operator or bystanders.
The pressure limiter helps prevent inflation of stan-
dard size or larger tires or tubes beyond 60 PSI to
minimize risk of explosion. This device is for the safety
of the operator and bystanders. Proper operation of
the pressure limiter is essential to safe operation of
the machine.
Check operation of the pressure limiter as shown
and described below at least monthly:
1.
Remove tires and/or wheels from the machine.
2.
Connect the inflation hose to an empty service
tank with a pressure gauge (should read 0). Use a tank
with at least 200 PSI pressure rating.
3.
Depress inflation pedal to position 1 to start
airflow through the hose and into the tank. Maintain a
steady pressure for constant flow.
4.
Watch the rising pressure on the tank gauge and
the gauge on the machine. Machine gauge should
cycle between check and inflation pressures while
tank gauge climbs steadily. As tank pressure reaches
60 PSI, the pressure limiter should stop the airflow
automatically. Both gauges should read 60 PSI ± 5
PSI.
5.
Release inflation pedal. Check manual release
valve function by pressing the button and releasing
pressure from the tank until it reaches 50 PSI. Discon-
nect inflation hose, and release air inside tank.
6.
Replace pressure limiter if it fails to cycle properly
during inflation, if it fails to shut air supply off at 60
PSI, or if it malfunctions in any other way. Do not oper-
ate machine with a faulty pressure limiter.
Watch
Pressure on
Both Gauges
Air Service
Tank
Tire Changer
Inflation Hose
Connected to
Tank