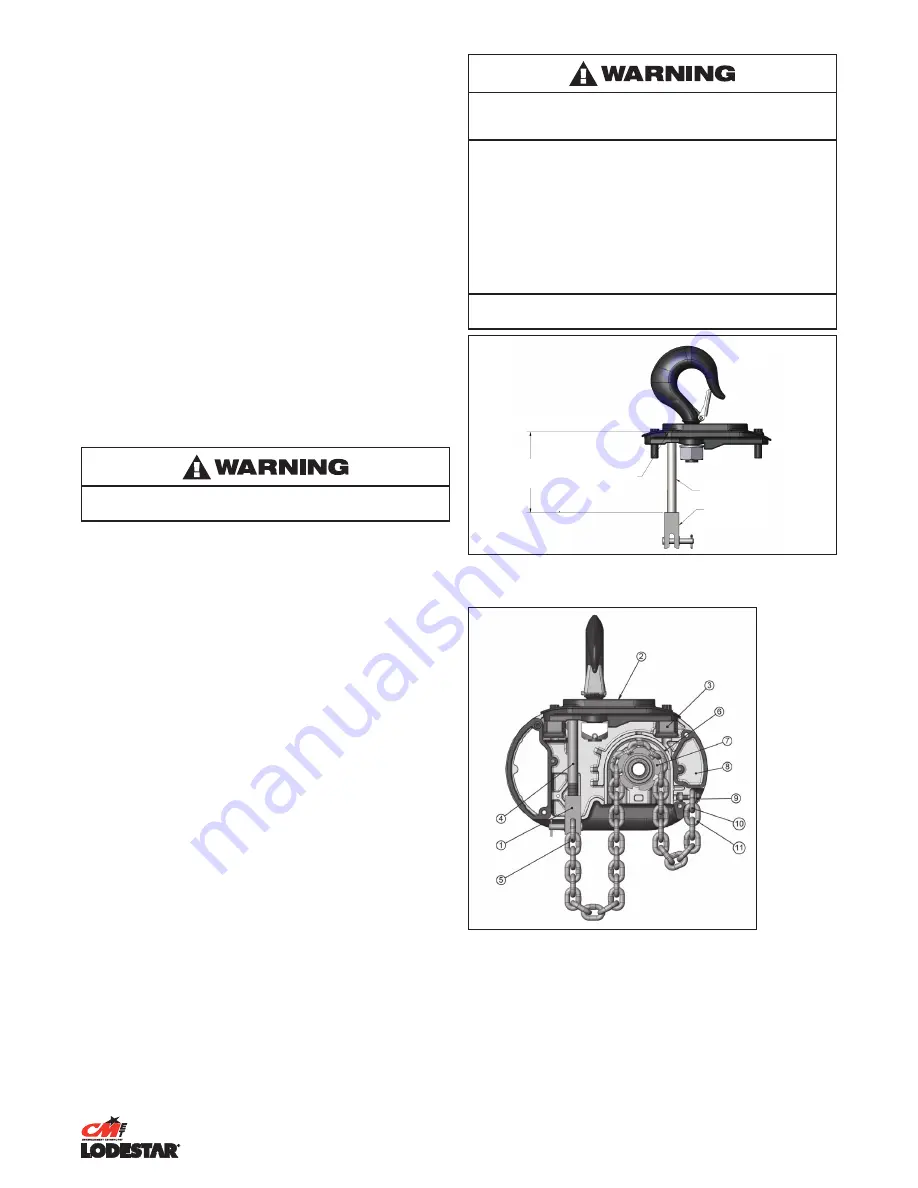
6
10001921 REV AC
July 2019
INSTALLATION
UNPACKING INFORMATION
When received, the hoist should be carefully inspected for damage
which may have occurred during shipment or handling. Check
the hoist frame for dents or cracks, the external cords for damaged
or cut insulation, the control station for cut or damaged enclosure,
and the load chain for nicks and gouges. If shipping damage has
occurred, refer to the packing list envelope on the carton for
claim procedure.
Before using the hoist, make sure the voltage change board is
connected for the intended power supply the hoist is to be operated.
NOTE: See Electrical Installation instructions.
INSTALLING THE SUSPENSION
(If Applicable)
A. SINGLE REEVED UNITS:
Remove the hook suspension and (2) suspension screws from the
packaging. Place the suspension assembly into the recess on top
of the hoist so that the adapter body follows the contour of the hoist.
Insert the suspension screws through the holes in the adapter and
hand thread these into the self-locking nuts enclosed in the hoist.
The screws will turn freely into the nuts until the last 1/4" (6.35 mm)
of travel, during which the resistance of the nut locking collar will
be encountered.
DO NOT apply any type of lubricant to the
threads of these screws.
USE OF IMPACT TOOLS (ELECTRIC OR PNEUMATIC) MAY
CAUSE PREMATURE FAILURE OF ATTACHING HARDWARE.
Securely tighten the screws to the recommended seating torque
using a 12 point socket 3/8" for Models B, C, and F and 1/2" for
Models J, L, LL, R and RR and 3/16" hex bit socket
for Model RRS."
For Model RRS:
Remove the hook suspension, screw and locknut
from the packaging. Slide the suspension assembly into the channel
in the top of the hoist. Insert the locknut into the hex recess on
the side of the suspension riser, insert the screw through opposite
side and hand thread the screw into the self-locking nut. Tighten to
recommended torque.
B. DOUBLE REEVED UNITS:
Remove the hook suspension, (2) suspension screws, (1) dead end
pin, (1) washer, and (1) cotter pin from the packaging. It should be
noted that the suspension includes a dead end bolt and block for
supporting the dead end of the load chain as shown in Figure 3.
Place the suspension assembly into the recess on top of the hoist.
The dead end block should project through the bottom of the hoist
with the pin hole and slot aligned to the underside of the hoist as
shown in Figure 4.
If these are not aligned as shown, lift the head of the bolt from
the hex recess in the adapter and turn the bolt and block assembly
and reseat the bolt head to obtain the proper alignment.
DO NOT
change the position of the dead end block on the bolt to attain
this alignment.
Check the position of the pin hole in the dead end block to make
sure it has not been disturbed from its factory setting. The distance
from the top of the pin hole to the bottom of the hoist should not
exceed 7/16" (11.11 mm) for the Models R and RR. If the distance
is not correct, adjust the position of the dead end block to obtain
the proper distance (see Figure 3).
Now, insert the suspension screws through the holes in the adapter
and hand thread these into the self-locking nuts enclosed in the
hoist frame.
DO NOT apply any type of lubricant to the threads of
these screws.
The screws will turn freely into the nut until the last
1/4" (6.35mm) of travel during which the resistance of the nut
locking collar will be encountered. Securely tighten the screws to the
recommended seating torque (see Table 11) using a 12 point socket
3/8" for Models B, C & F and 1/2" for Models J, L, LL, R and RR.
The dead end of the load chain is temporarily positioned (a few
links from the end) by a wire tie.
DO NOT remove this tie before
attaching the chain to the dead end block
.
Using other than CM supplied high strength suspension screws to
attach the suspension adapter to the hoist may cause the screws
to break and allow the hoist and load to fall.
TO AVOID INJURY:
Use only the CM supplied suspension screws to attach the
suspension to the hoist and hand torque these screws to the
recommended seating torque as specified in tables 11a, 11b,
11c, & 11d.
DO NOT apply any type of lubricant to the threads of these
screws. Lubricating the threads will reduce the effort to seat
the screws and as a result, tightening the screws to the above
recommended torque may break the screw, damage the
suspension adapter, strip the nuts and/or damage the hoist frame.
SUSPENSION BOLT SHOULD BE REPLACED ANY TIME THE
SUSPENSION IS REMOVED FROM THE HOIST.
UNDER SIDE
OF SUSPENSION
ADAPTER FLANGE
DEAD END BOLT
DEAD END BLOCK
5.45in
(138.43mm)
Models R & RR
Figure 3. Double Reeved Suspension Assembly
Figure 4. Suspension Components
(Chain Plate not shown for clarity.)
1. Dead end block
2. Suspension assembly
3. Suspension self-locking nut
4. Dead end bolt
5. Dead end link
6. Chain guide
7. Lift-wheel
8. Gear housing
9. Loose end screw
10. Loose end link
11. Loose end