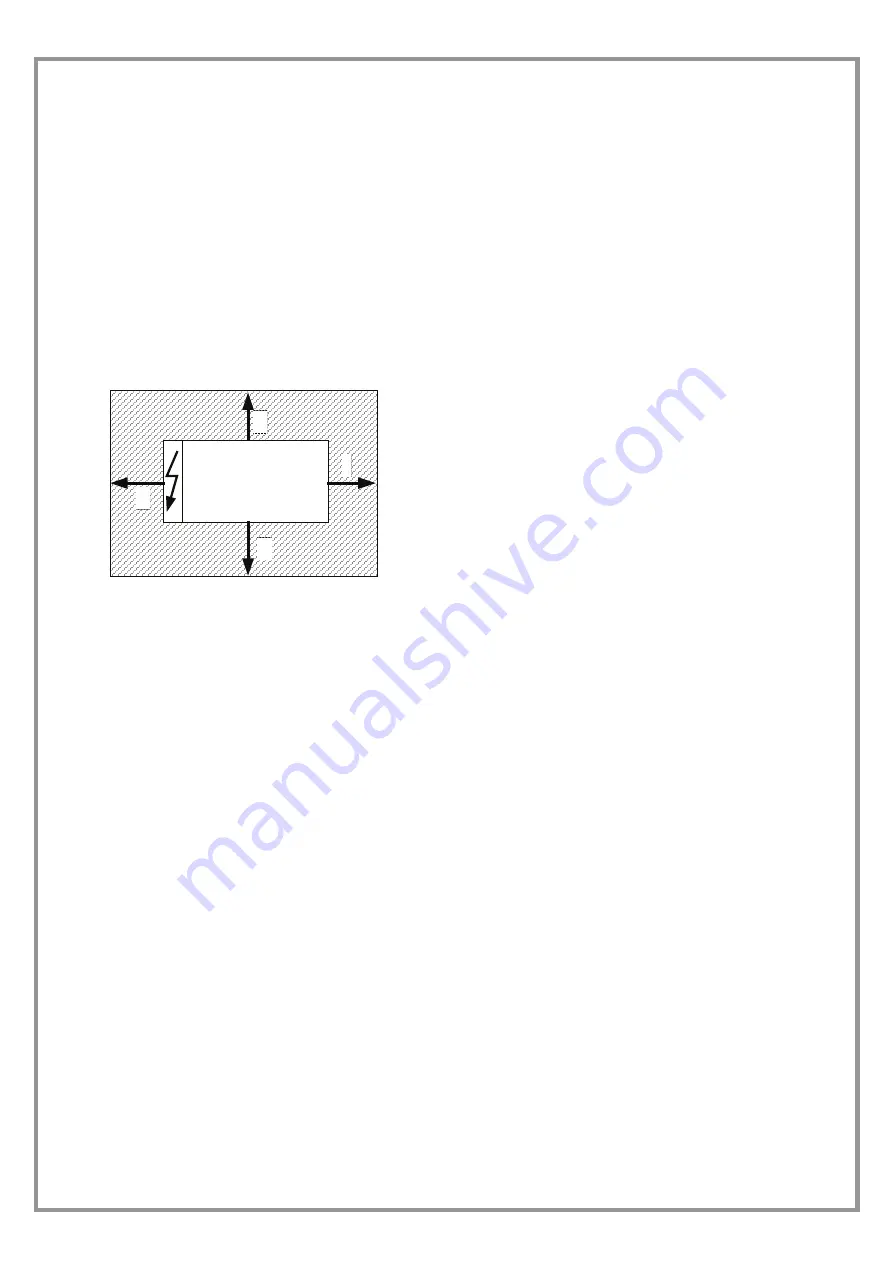
M0G140F7-01 06/11/07
pag
9
RESIDUAL RISKS
GENERAL
This section lists some of the more common situations
which, being beyond the control of the manufacturer, could
be a source of risk to persons or property.
DANGER AREA
The figure below highlights the area in which only
authorised personnel may operate.
•
External danger zone
, identified by a precise area
around the unit and its vertical projection on the
ground in the case of hanging unit.
•
Internal danger zone
, identified by the area that can
be entered only after having intentionally removed the
protecting panels or parts of these.
A
B
C
D
A = 2000 mm
B = 2000 mm
C = 2000 mm
D = 2000 mm
HANDLING
If handling operations are undertaken without adopting all
the necessary safety procedures and exercising due care,
the unit can fall or topple, causing damage — possibly
extremely serious — to persons and/or property, and to the
unit itself.
Ensure the unit is handled and manoeuvred as directed on
the packing and in the present manual, and in accordance
with local regulations.
In the event of refrigerant gas escaping, refer to the “Safety
datasheet” for the particular refrigerant.
INSTALLATION
Incorrect installation of the unit can result in water leaks,
accumulation of condensate, escape of refrigerant, electric
shocks, fire, as well as irregular operation or damage to the
unit itself.
Make certain that the installation is carried out only by a
qualified technician, also that the directions contained in
this manual are followed and local statutory regulations
observed.
In the event of the unit being installed in a site where there
is even the slightest risk of inflammable gas escapes and
consequently the possibility of such gases accumulating in
area around the unit, the risk of explosion and fire cannot
be discounted.
Take every care and precaution when selecting the
installation site.
Installation on a structure not able to bear the weight and/or
afford a secure anchorage of the equipment may cause the
unit to fall and/or topple, resulting in damage to persons or
property, or to the unit itself. Make certain that every care
and precaution is taken when positioning and securing the
unit.
If the unit is easily accessible to children, unauthorized
persons or animals, this is a situation that can give rise
accidents and injuries, perhaps serious. Install the unit in a
place where access is allowed only to authorized persons,
or install barriers or guards preventing unauthorized entry.
GENERAL RISKS
A smell of burning, smoke or other indications of serious
irregularity could signal the onset of situations liable to
cause damage to persons or property or to the unit itself.
Isolate the unit from the electrical power supply (red-and-
yellow) switch.
Contact an authorized service centre so that the source of
the problem can be identified and remedied.
Accidental contact with heat exchange coils, compressors,
pressure pipelines or other components can result in
wounding or burns, or both.
Always wear suitable clothing, including protective gloves,
when working in the danger area.
Maintenance or repairs carried out by unskilled operatives
can result in harm or damage to persons and property, or to
the unit itself. Always contact an authorized service centre.
Failure to close the panels of the unit, or to check that all
the fixing screws of the panels are properly tightened, can
result in harm or damage to persons or property, or to the
unit itself.
Verify periodically that all panels are closed and made
properly secure.
In the event of fire, the temperature of the refrigerant can
rise to the point that pressure will exceed safety levels and
perhaps cause fluid to be projected. It may also happen
that parts of the circuit isolated by closed valves will
explode.
Do not stand near safety valves, and never leave the valves
of the refrigerant circuit closed.
ELECTRICAL SYSTEM
If the power line connecting the unit to the a.c. supply is
incomplete, or if the connection is made with cables of
incorrect cross section and/or with insufficiently rated
protective devices, this can result in electric shock, toxicity
hazard, damage to the unit or fire.
All work on the electrical system should be carried out
referring to the wiring diagram and to the directions given in
this manual, and the system itself must be dedicated.
Failure to secure the cover enclosing electrical components
can lead to the infiltration of dust and water, ultimately
causing electric shocks, damage to the unit, or fire.
Always fasten the cover securely to the unit.
If live metal parts of the unit are not connected properly to
the earth system, they can cause electric shock or even
death by electrocution.
Make absolutely certain that the connection to the earth
system is made in accordance with correct practice.
Contact with live parts rendered accessible internally of the
unit when the guards are removed can result in electric
shock, burns or death by electrocution.
Before exposing these parts, make certain the isolating
switch on the power line to the unit is set to the OFF
position and padlocked, and post a warning sign.