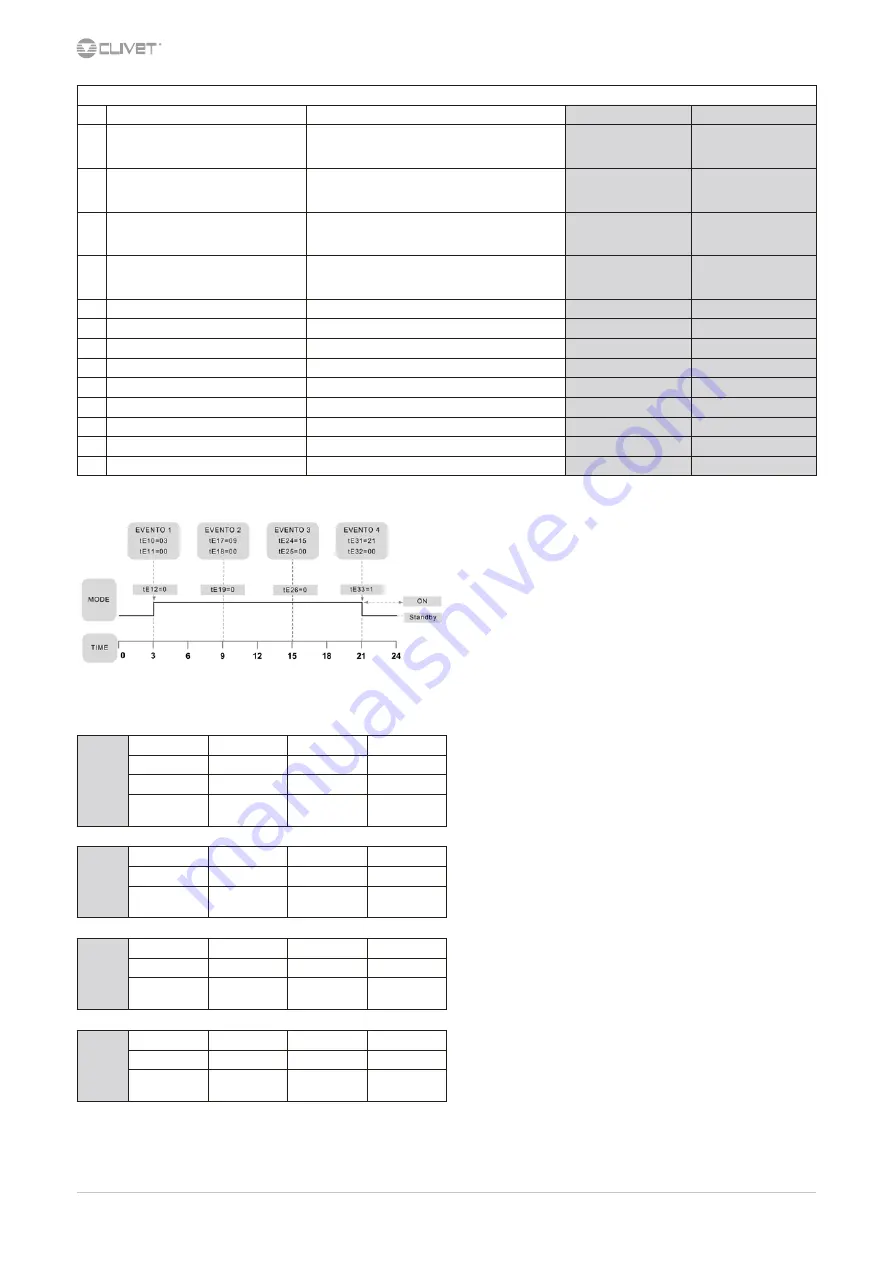
22
MSAT-XEE 8.2-30.2
M09G60E14-04
Set the scheduling
1
set the scheduling num.1
scheduling 1 parameters
scheduling 2 parameters scheduling 3 parameters
1.1
set event 1
Event hour → par. tE10
Event minutes → par. tE11
Unit mode → par. tE12 (0=On, 1=standby)
tE38
tE39
tE40
tE66
tE67
tE68
1.2
set event 2
Event hour → par. tE17
Event minutes → par. tE18
Unit mode → par. tE19 (0=On, 1=standby)
tE45
tE46
tE47
tE73
tE74
tE75
1.3
set event 3
Event hour → par. tE24
Event minutes → par. tE25
Unit mode → par. tE26 (0=On, 1=standby)
tE52
tE53
tE54
tE80
tE81
tE82
1.4
set event 4
Event hour → par. tE31
Event minutes → par. tE32
Unit mode → par. tE33 (0=On, 1=standby)
tE59
tE60
tE61
tE87
tE88
tE89
2
set the scheduling num.2
column → scheduling 2 parameters
3
set the scheduling num.3
column → scheduling 3 parameters
4
assign the scheduling to monday
tE01 = 1 scheduling 1
= 2 scheduling 2
= 3 scheduling 3
5
assign the scheduling to tuesday
tE02 = 1 scheduling 1
= 2 scheduling 2
= 3 scheduling 3
6
assign the scheduling to wednesday
tE03 = 1 scheduling 1
= 2 scheduling 2
= 3 scheduling 3
7
assign the scheduling to thursday
tE04 = 1 scheduling 1
= 2 scheduling 2
= 3 scheduling 3
8
assign the scheduling to friday
tE05 = 1 scheduling 1
= 2 scheduling 2
= 3 scheduling 3
9
assign the scheduling to saturday
tE06 = 1 scheduling 1
= 2 scheduling 2
= 3 scheduling 3
10
assign the scheduling to sunday
tE07 = 1 scheduling 1
= 2 scheduling 2
= 3 scheduling 3
Example: scheduling 1
Events parameters
Event 1
Sched. 1 (par.)
Sched. 2 (par.)
Sched. 3 (par.)
Time
tE10
tE38
tE66
Minutes
tE11
tE39
tE67
Mode 0= on
1= standby
tE12
tE40
tE68
Event 2
Time
tE17
tE45
tE73
Minutes
tE18
tE50
tE74
Mode 0= on
1= standby
tE19
tE47
tE75
Event 3
Time
tE24
tE52
tE80
Minutes
tE25
tE53
tE81
Mode 0= on
1= standby
tE26
tE54
tE82
Event 4
Time
tE31
tE59
tE87
Minutes
tE32
tE60
tE88
Mode 0= on
1= standby
tE33
tE61
tE89
Summary of Contents for MSAT-XEE 10.2
Page 41: ...43 Letter Seite...