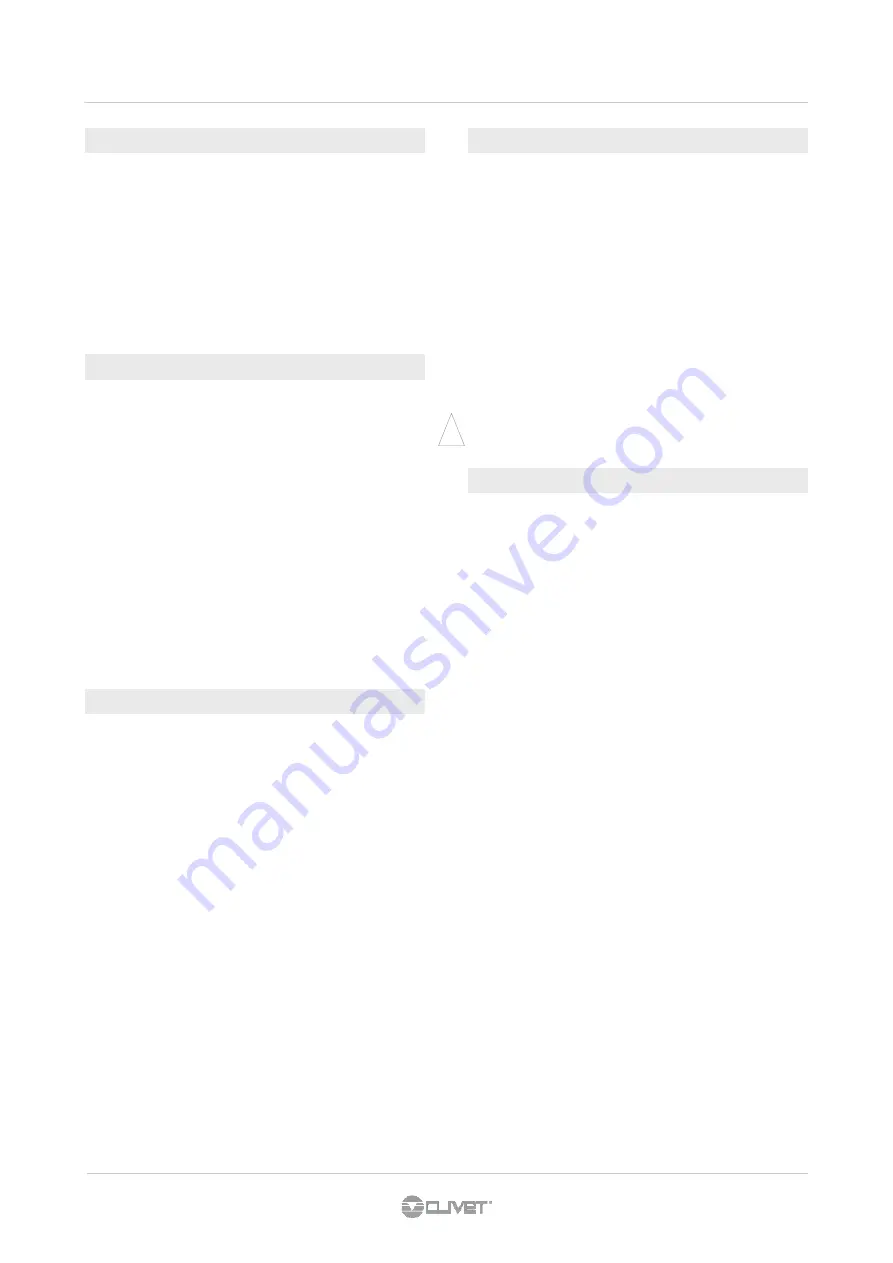
17
7- START-UP
Check the air and water temperatures are within the operatio-
nal limits.
Start the unit; refer to the "Adjustment" section for indications
on the control system.
With the unit running, meaning in stable conditions and near
the work ones, check:
•
power supply voltage
•
unit overall absorption
•
absorption of the individual electric loads.
7.7 VOLTAGES
The Scroll compressors have only one rotation direction.
In the event it is reversed, the compressor is not immediately
damaged, but increases its noise and jeopardises pumping.
After a few minutes, the compressor blocks due to intervention
of the thermal protection. In this case, disconnect power
supply and invert 2 phases on the machine power supply.
Avoid the compressor working for a long time with contrary
rotation: more than 2-3 of these anomalous start-ups can
damage it.
To ensure the rotation direction is correct, measure the
condensation and suction pressure. The pressures must
significantly differ: upon start-up, the suction pressure
decreases whereas the condensation one, increases.
The phase monitor optional, controlling the phases sequence,
can also eventually be installed subsequently.
7.8 ROOM PRESSURE CALIBRATION
Check the remote controls (ON-OFF, etc.) are connected
and, if necessary, enabled with relative parameters
(ELECTRIC CONNECTIONS sections and following pages)
Check the probes or optional components are connected and
enabled with the relative parameters.
7.9 REMOTE CONSENTS
i
7.10 START-UP REPORT
To detect the objective operational conditions is useful to
control the unit over time.
With the unit running, meaning in stable conditions and near
the work ones, detect the following data:
•
Overall absorptions and voltages with unit in full load
•
Absorptions of the various electric loads
(compressors, fans, pumps etc)
•
Temperatures and flow rates of the various fluids
(water, air) at input and output of the unit
•
Temperatures and pressures in the feature points of
the cooling circuit (compressor, liquid, suction drain/
unload)
The detections must be kept and made available during
maintenance interventions.
7.11 EC DIRECTIVE 97/23 PED
From Directive 97/23 EC PED derive the prescriptions for the
installers, the users and the maintenance operators of the unit
also.
Refer to the local implemented standards; in synthesis and for
merely indicative purposes:
•
Compulsory check of first system:
only for units assembled on site by the installer (e.g.
cond direct expansion unit)
•
Declaration of start-up:
for all units
•
Periodical checks:
to be carried out as frequently as defined by the
Manufacturer
(see MAINTENANCE section) .