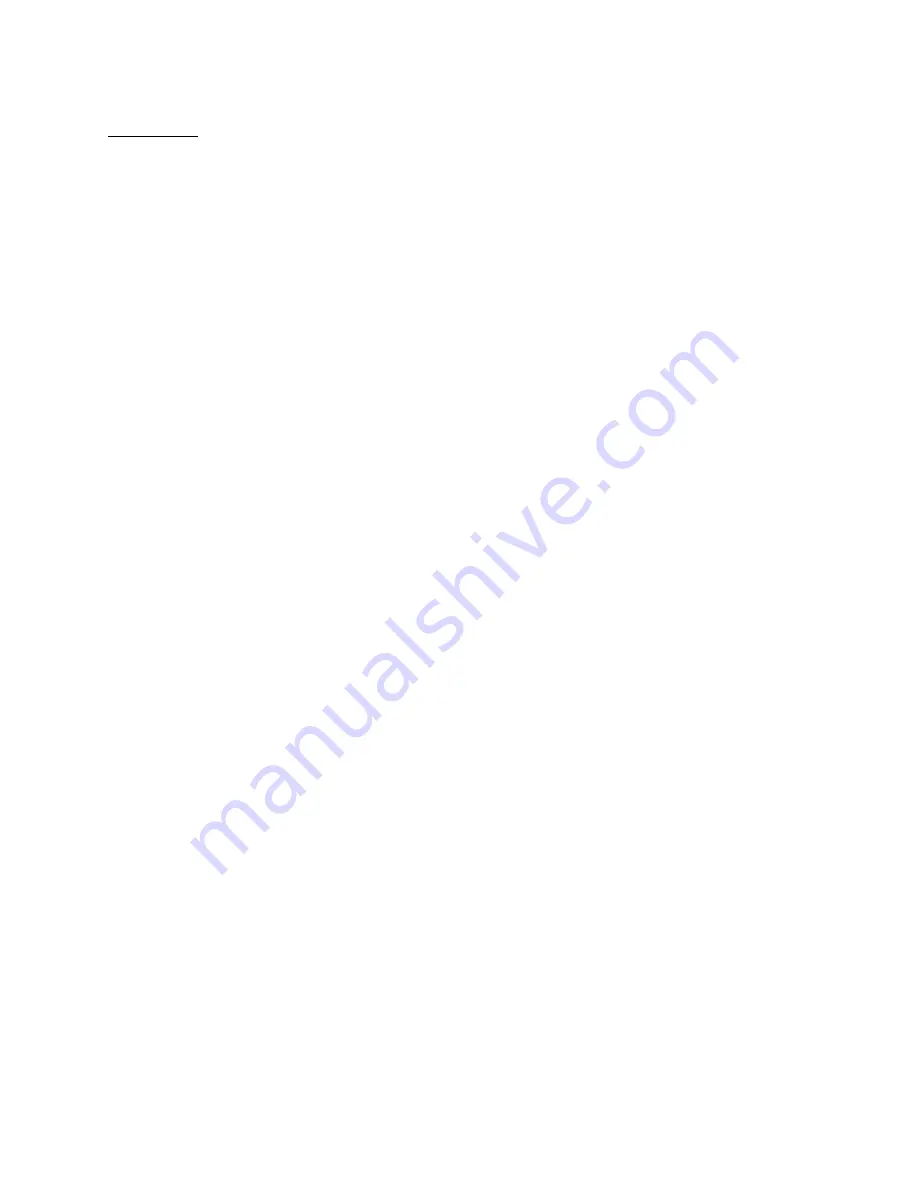
LOCATION
Careful consideration must be given to selecting the proper location for the cleaner or the
best results in efficiency and convenience cannot be expected. All models should be
fastened to a solid, level floor or foundation
. THE ENTIRE BASE OF THE MACHINE
SHOULD BE SUPPORTED. 3/4-8 grade 5 bolts are recommended. If an exiting
machine is being replaced, in almost all cases the exiting mounting stand will not be
built heavy enough to support the new machine being installed
.
The cleaner should be placed with the fan discharge opening facing, and a short distance
away from an outside wall. Screens are inserted and withdrawn at the front of the cleaner.
Allow clearance for the operator to make screen changes. The largest single piece screen
is 54" x 26 ". Allow room around the cleaner for the operator to make adjustments and
service the machine. Do not install spouting in a position that will interfere with the controls
or maintenance. Eventually worn parts must be replaced so allow room to pull all shafts
and spouts.
The cleaned grain discharges from the under side of the cleaner, so it should be placed on
a floor with a pit or basement underneath so that an elevator with its receiving spout three
or four feet below the floor can be used to raise the grain. If the elevator cannot be carried
below the floor, and there is sufficient headroom, the cleaner may be placed on a solid
platform high enough above the floor to allow the grain to flow into the elevator or sacking
spout. Screenings and air lifting’s discharge from built-in spouts in the cleaner. Provision
must be made to handle this material.
The Cleaner hopper is a feeder mechanism - not a storage bin. Cleaners work best when
equipped with a surge bin above the hopper to provide a steady supply of the commodity
to the hopper. The grain supply to the surge hopper may be by spout from bins located on
the floor above or by means of an elevator from a sink of dump hopper on the same level
or lower than the cleaner. Spouts must have a fall of at least seven feet in ten to provide
free flow and should be carried directly at an angle instead of making right angle jogs.
The
feed hopper works best when it is feed across the width of the hopper inlet opening.
If a full width feed cannot be used, a inverted y transition with a 24” distance
between the spouts is the second best style. This would drop the product to each
side of the hopper