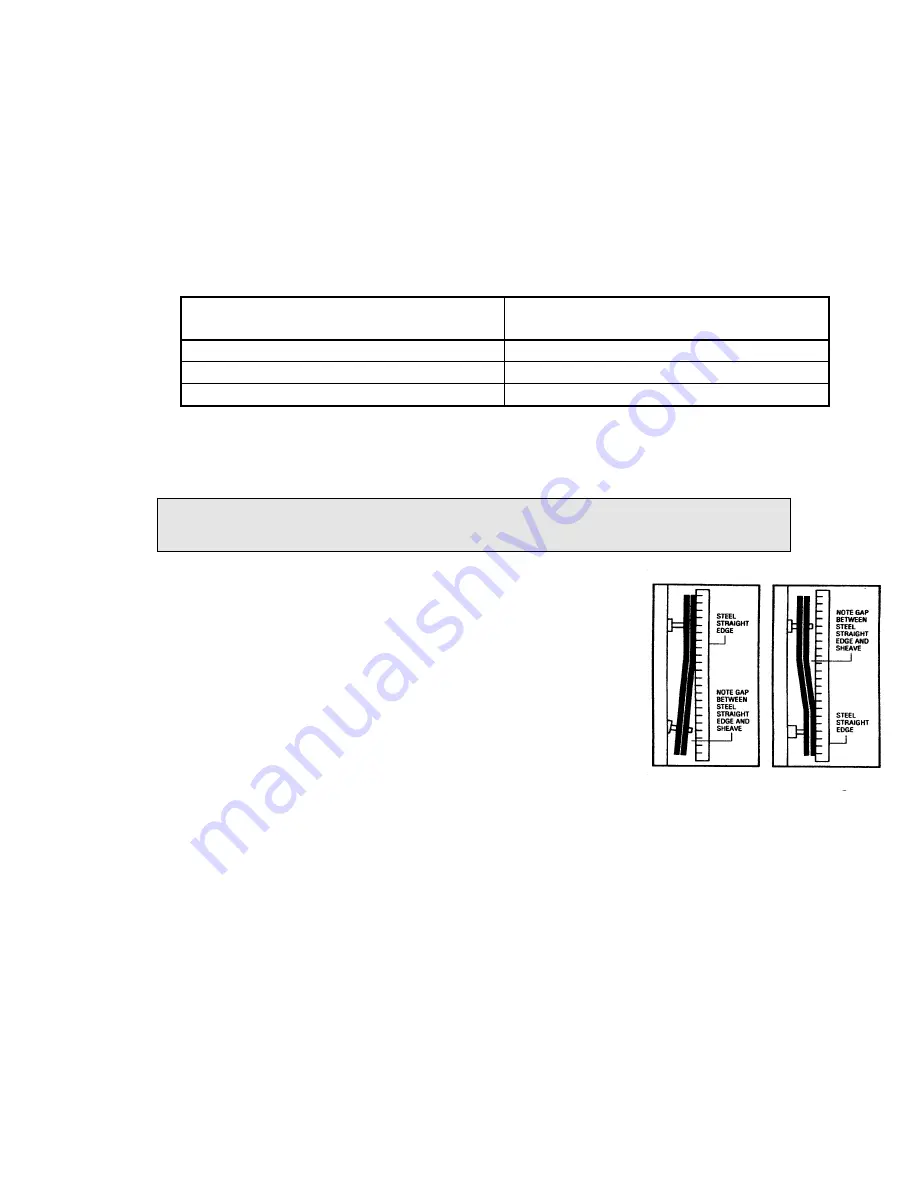
15
For best results, bearings should be relubricated while in operation.
Note:
Due caution for personal safety must be observed when servicing
rotating equipment.
The grease should be pumped in slowly until a
slight bead forms around the seals. This bead, in addition to acting as an
indicator of adequate relubrication, provides additional protection against
the entry of foreign matter. If necessary to relubricate while the bearing is
idle refer to relubrication table for maximum grease capacity for the
various size bearings.
Shaft Size
Maximum Grease Capacity of
Bearing Chamber in Ounces
1/2"' to 3/4"
1/8
7/8" to 1-3/16"
3/8
1-1/4" to 1-1/2"
5/8
C. V-Belts
Warning: Never make adjustments to belts or pulleys while
engine is running!
1. The best tension for a belt drive is the lowest tension at
which the belts will not slip under full load.
2. Simply take up the drive until the belts are snug in the
grooves. Run the drive for about 15 minutes to "seat" the
belts. Then impose the peak load. If the belts slip, tighten
them until they no longer slip at peak load.
3.
Remember, too much tension shortens belt and
bearing life!
4. Check the belt tension frequently during the first day of operation. Check
the belt tension periodically thereafter and make any necessary
adjustments.
5. The two most common causes of misalignment are shown in the drawing.
a). The engine drive shaft and the blade shaft are not parallel.
b). The pulleys are not located properly on the shafts.
6. To check alignment, all you need is a steel straight edge.
FIGURE 1
FIGURE 2
Summary of Contents for C9
Page 1: ...OWNERS MANUAL Small Concrete Saw MODEL C9 FORM 7418 3 2005 ...
Page 18: ...18 C9 Parts Drawing ...
Page 19: ...19 C9 Parts Drawing ...
Page 21: ...NOTES ...