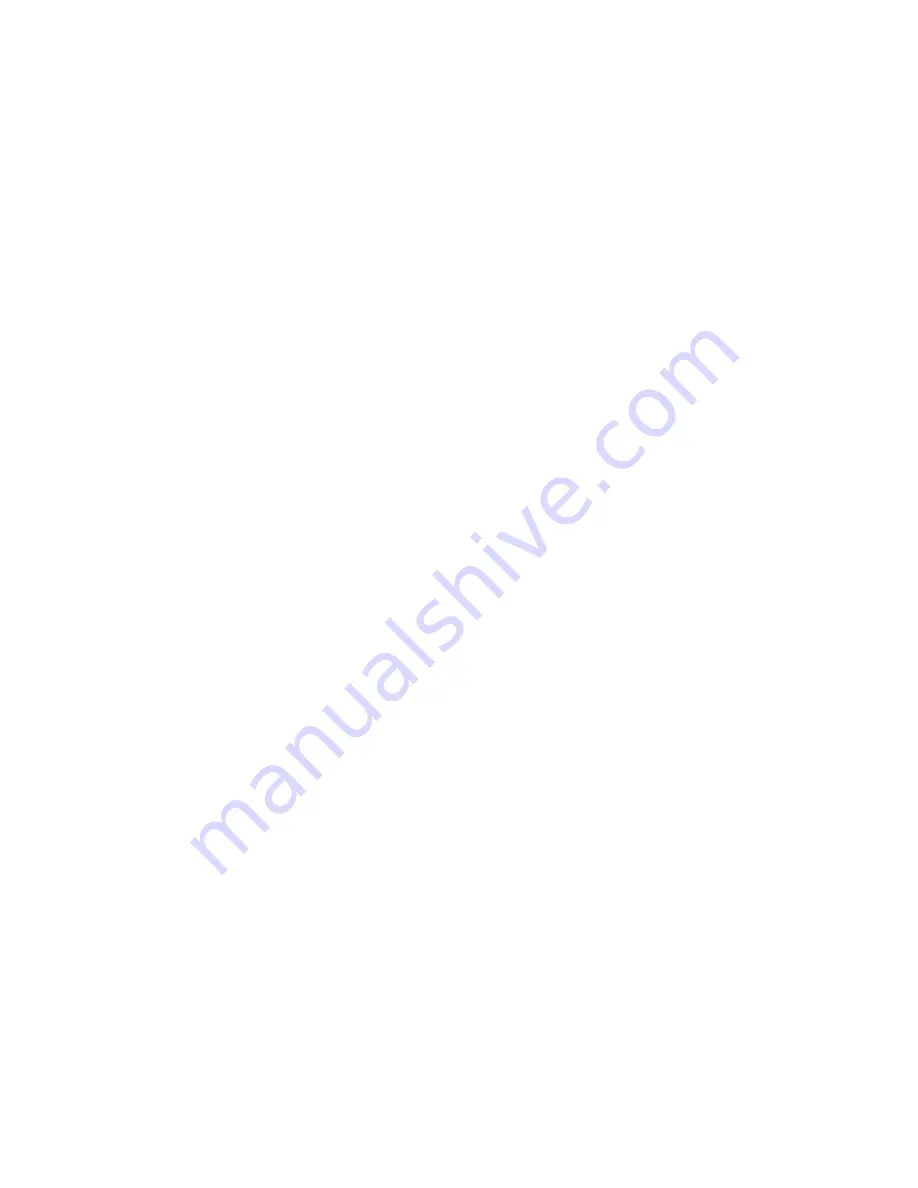
16
7. Line up the straight edge along the outside face of both pulleys as shown
in the drawing.
8. Misalignment will show up as a gap between the pulley face and the
straight edge.
9. Make sure that the width of the outside land (area between the belt and
the edge of the pulley) is equal on both pulleys.
D. Depth Control
The depth control (raising screw) consists of a threaded rod, which feeds into
a brass nut. In order to keep the two parts working smoothly it is necessary
to keep the rod free from dirt and sludge as much as possible. Cleaning the
threaded rod with a rag after each use will prevent sludge from collecting in
the tube assembly and protect the threads. It is a good practice to keep the
raising screw threads lubricated, as the slurry generated during cutting will
cause premature thread wear.
The bearing used to support the raising screw should be checked after each
use to make sure it is turning freely and lubricated. If the bearing requires re
lubrication lithium base grease is recommended.
Summary of Contents for C13E
Page 1: ...OWNERS MANUAL Small Concrete Saw MODEL C13E FORM C13E 11 2005...
Page 18: ...18 C13E Parts Drawing...
Page 19: ...19 C13E Parts Drawing...
Page 21: ...NOTES...