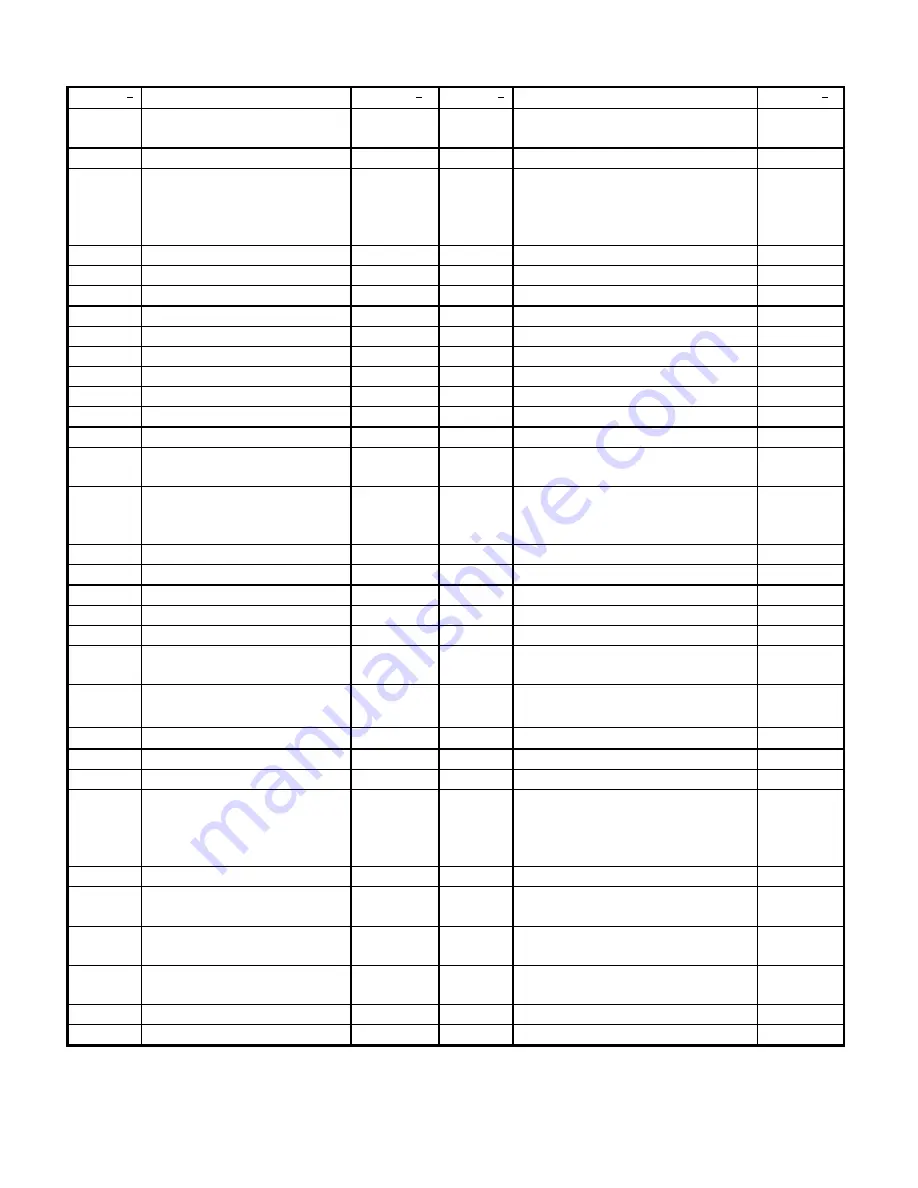
18
BBH Masonry Saw Parts
Item N
o
Description
Part N
o
Item N
o
Description
Part N
o
1
Drain Plug
213622
33
Lower Stay Level Arm
Assembly
219074
2
Frame Weldment
219026C
34
Bearing Kit Pivot Head
219070
3
Water Pump Kit
Screen
Hood
Impeller (Not Shown)
216138
216641
216642
216658
35
Water Curtain Assembly
219038
4
Conveyor Cart
216286
36
Protection Plate Kit
218047
5
Sheaves, Cart [4]
213621
37
Bushing Bearing Nylon
213631
6
Back Stop, Cart
216288
38
Support Blade Shaft
214129C
7
Wood strip, Cart
216287
39
Bearing Blade Shaft (1)
218049
8
Hardware Kit, Back Stop
216293
40
Blade Shaft Kit
218050
9
Guide A Cut Assembly
216128
41
Loose Collar
218016
10
Scale Kit
216291
42
Screw Loose Collar
8042096
11
Wrench 3/4"
213643
43
Belt Guard Assembly
218051
12
Wrench 7/8"
214124
44
Pulley Blade Shaft
76132
13
Stop Rubber
210051
45
Bracket Belt Guard
218052
14
Tensioning Eye-Bolt
73277
46
V-Belts 20” Blade Guard
V-Belts 14” Blade Guard
216662
216663
15
Spring, Foot Pedal
72567
47
Pulley Motor 14” 5HP
Pulley Motor 20” 5HP
Pulley Motor 20” 7.5HP
76130
76131
210926
16
Decal Kit (Not Shown)
219062
48
Screw Belt Tensioning
73277
17
Raising Screw Assembly
219063
49
Cutting Head Weldment
219015C
18
Raising Screw Kit
219064
50
Clamp Kit Cable
214029
19
Hand Wheel
219034
51
Stay Level Pivot Weldment
219009
20
Set Collar
101132
52
Splash Guard Kit
218053
21
Bearing Kit Raise Screw
219065
53
Blade Guard 14”
Blade Guard 20”
214102C
218007
22
Cover, Raise/Lower
219010
54
Water Distribution Assy. 14”
Water Distribution Assy. 20”
214052
218055
23
Foot Pedal Weldment
219029
55
Cam Kit Stay Level Arm
214132
24
Horizontal Link
219031
56
Stay Level Arm
218014
25
Drain Hose & Clamp
219066
57
Pin Kit Stay-Level Arm
214131
26
Vertical Link Assembly
219067
58
Motor 5HP 230/60Hz/1ph
Motor 5HP 230-460/60Hz/3ph
Motor 7.5HP 230-
460/60Hz/3ph
211038
219040
219041
27
Diagonal Link Weldment
219032
59A
Receptacle Water Pump
212168
28
Yoke Weldment
Assembly
219068
59B
Pigtail Water Pump
212168
29
Connecting Link
Assembly
219069
60
Switch Assembly 230/60/1
Switch Assembly 230-460/60/3
218093
218094
30
Pivot Bar Rear
219071
-NA-
Switch Box Only (NO
SWITCH)
219060
31
Swing Arm Assembly
219072
-NA-
Electrical Switch & Box Only
219059
32
Set Collar Kit
219073
Summary of Contents for BBH255
Page 1: ...OWNERS MANUAL Clipper Masonry Saw Models BBH455 BBH255 BBH275 FORM 5316 rev9 00 ...
Page 6: ...5 I PEPARATION C Wiring Diagram ...
Page 7: ...6 ...
Page 18: ...17 V PARTS LIST SECTION D Assembly Drawing ...
Page 20: ...19 ...
Page 21: ...20 ...
Page 22: ...21 ...
Page 23: ...22 ...
Page 24: ...23 ...
Page 25: ...24 ...
Page 26: ...25 ...
Page 27: ...26 ...
Page 28: ...27 NOTES ...