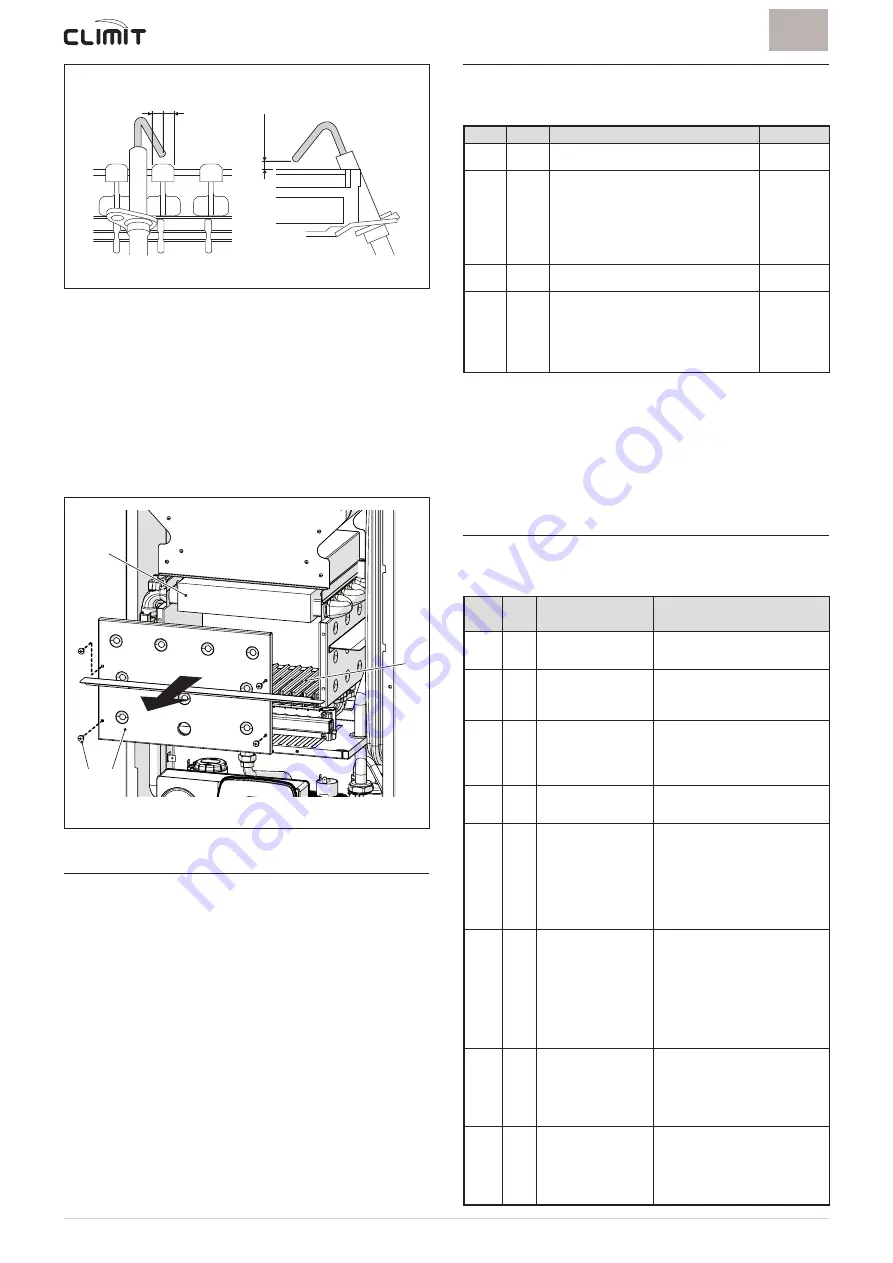
56
IT
EN
= =
3,5mm
+0,5 -0,5
Fig. 41
m
CAUTION
The position of the electrode is essential for the correct
detection of current ionization.
4.3.4
Final operations
After having cleaned the heat exchanger and the burner:
– remove any carbon residue using a vacuum cleaner
– check that the gasket and the insulation of the front panel (4)
of the combustion chamber are integral. If this is not the case
then replace it
– refit the panel (4) secure it with fastening screws.
3 4
5
6
Fig. 42
4.4
Checks
4.4.1
Checking the smoke duct
It is recommended that the user checks that the smoke outlet
duct is integral and airtight.
4.4.2
Checking the expansion vessel pressure
It is recommended that the expansion vessel on the water side
is drained and that the prefilling pressure is not less than
1 bar
.
If this is not the case, pressurize it to the correct value (see
Once the checks described above have been completed:
– refill the boiler as described in section "REFILL operations"
– start the boiler up and carry out a smoke analysis and/or
measure the combustion efficiency
– refit the front panel securing it with the two screws which
were removed previously
4.5
Unscheduled maintenance
If replacing the
electronic board
, the user MUST set the
parameters as indicated in the table and in the sequence shown.
Type
No.
Description
Setting
tS
0.1
Index showing boiler power in kW
0 = 24
0
tS
0.2
Hydraulic configuration
0 = rapid
1 = storage tank with thermostat or
heating only
2 = hot water tank with sensor
3 = bithermic
4=instant with solar power input
0
tS
0.3
Gas Type Configuration
0 = G20; 1 = G31
0 or 1
tS
0.4
Combustion configuration
0 = sealed chamber with combustion
control
1 = open chamber with smoke
thermostat
2 = low NOx
1
To enter "Parameter setting and display"refer to the indications
provided in the specific section.
Once the parameters in the table have been set, you must carry
out the "Automatic calibration procedure".
If the
gas valve
and/or the
ignition/detection electrode
, are
replaced, the user must still carry out the entire phase of "
Automatic calibration procedure" described in the specific
section.
4.6
Malfunction codes and possible solutions
LIST OF MALFUNCTION/FAULT ALARMS
Type No. Fault
Solution
AL
01 Smoke thermostat
- Contact the Technical
Assistance Centre
AL
02 Low water pressure
in system
- Restore pressure
- Check for any leaks in the
system
AL
04
Domestic hot water
sensor fault (return
sensor fault for T
models)
- Check connections
- Check the sensor is working
AL
05 Delivery sensor fault - Check connections
- Check the sensor is working
AL
06 No flame detection
- Check the integrity of the
electrode and check that it is
not grounded
- Check gas availability and
pressure
- Check the integrity of the gas
valve and the card
AL
07
Sensor or safety
thermostat
intervenes
- Check the sensor or
thermostat connections
- Deaerate the system
- Check the bleed valve
- Replace the sensor or the
thermostat
- Check that the pump impeller
is not blocked
AL
08 Fault in the flame
detection circuit
- Check the integrity of the
electrode and check that it is
not grounded
- Check the integrity of the gas
valve and the card
AL
09 No water circulating
in the system
- Check the rotation of the pump
rotor
- Check the electrical
connections
- Replace the pump
Summary of Contents for 24 OF
Page 114: ...114 ...
Page 115: ...115 ...
Page 116: ...Via Garbo 27 37045 Legnago Vr Tel 39 0442 631111 Fax 39 0442 631292 ...