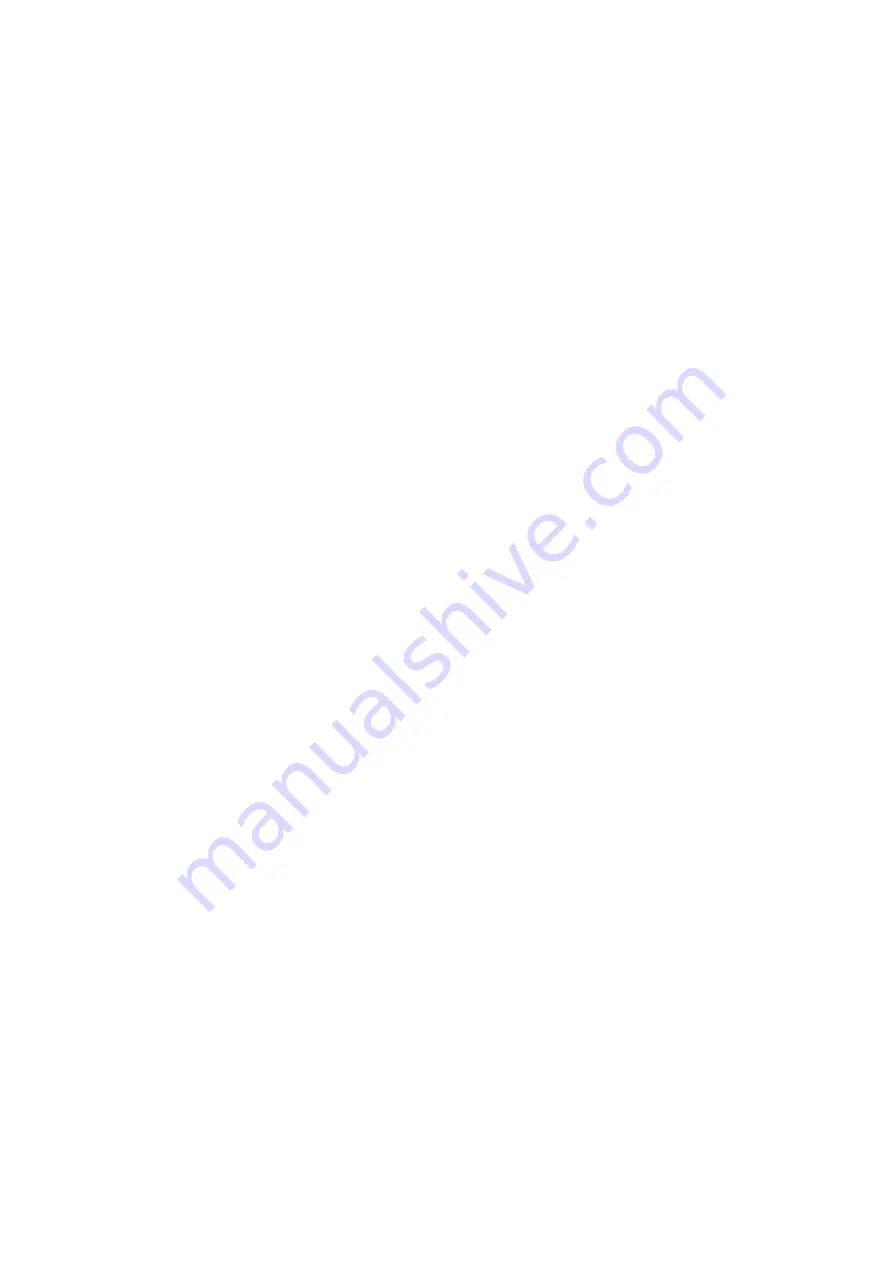
8
CLIMIA
Safety instructions for certified
specialist personnel
•
Check the work area
Before starting work on units
with combustible refrigerants,
ensure that any potential
ignition sources are removed
and the risk of igniting the
refrigerants is eliminated. The
aforementioned safety notes
for repairing the units must
be observed at all times. Work
may only be carried out by
authorised specialist personnel
with knowledge of handling
combustible refrigerants!
•
Prepare the work area
Any persons present must
be informed about the repair
process accordingly and
persons not involved must
vacate the work area. Working
in rooms with limited space
is prohibited. Ensure that
sufficient space is available at
the workplace. Ensure that the
ambient conditions are suitable
for working with combustible
refrigerants.
•
Identify refrigerant leaks, check
the atmosphere
Refrigerant may unexpectedly
escape when working on the
refrigerant circuit. Ensure that
the atmosphere in the workplace
is not combustible at all times
by using suitable refrigerant
detectors. Be sure to ensure
that the refrigerant detector
used is suitable, approved
and calibrated for use with
refrigerant R290.
•
Provide fire extinguishers
Provide appropriate fire
extinguishers before starting
work. For this purpose, dry
powder or CO
2
fire extinguishers
are suitable.
•
Remove any potential ignition
sources
Leaking refrigerant in
combination with corresponding
ignition sources can lead to an
explosion. All ignition sources
must therefore be kept away
from the work area at all times!
This also includes the smoking
of cigarettes. Inform all persons
present that this includes the
affixing of safety notes and the
closing off of the work area.
•
Sufficient ventilation
Before starting work, ensure
that the work area is outdoors
or has sufficient ventilation. A
continuous ventilation stream
is required while working.
The safety of the persons
working must be guaranteed
by the exhaust air equipment:
potentially leaking refrigerant
must be lead away safely and
drained into the atmosphere in
an optimum manner.
•
Checking the refrigerant circuit
If electronic components need
to be replaced, ensure that
the spare parts have the same
function and identical technical
specifications. The maintenance
and replacement regulations of
the manufacturer must always
be observed and complied with.
Please contact the support of the
manufacturer with any problems
or queries.
The following safety checks
must be carried out when using
combustible refrigerants:
- The fill level adjusts to the size
of the rooms in which the unit is
located.
- The exhaust air equipment and
its outlets function properly and
are not blocked or obstructed.
•
Checking the electronic
components
A component and safety check
must be carried out before
repairing and maintaining
electronic components. If
safety cannot be ensured due
to a defect on a component,
installation must not take place
until safety can be guaranteed
again. If the defect on the spare
part cannot be remedied and
downtime of the unit is no
longer acceptable, an adequate
temporary solution must be
arranged. The owner/operator
of the unit must be informed
about this. The detailed safety
check must include the following
aspects:
- Capacitors are discharged. A
safe discharge process must
be employed to prevent flying
sparks.
- There must be no electronic
components active or
uninsulated wires while filling,
repairing or cleaning.
- There must be no earthing of
the system.